We recently helped out a customer in determining why some of their welds were cracking. It was determined that cracking on their parts was due to rapid cooling and improperly sized welds. The discussions we had before and after determining the cause were quite interesting. We went over the typical causes for cracking with our customer. Here is a brief summary of our meetings. Please note that these are not all the causes for cracks.
Generally speaking we can separate cracks in two groups, which have to do with the timing of the cracks: hot cracking and cold cracking. Essentially hot cracking occurs as you weld or shortly thereafter while cold cracking can occur hours or even days after welding is completed.
Hot Cracking
Hot cracking is mainly due to high amounts of elements with low melting temperatures in the base material. Slightly elevated amounts of these elements is usually not enough to cause cracking, but rather it couples with other issues such as improper width to depth ratio of the weld bead. Some elements used in steel making like sulfur and phosphorus have low melting points. Because of these low melting points these elements are pushed to the center of the weld bead as it is solidifying. These elements can then get trapped in the middle of the weld when the puddle does not stay in a molten state long enough. When this occurs we get a centerline crack as the one pictured below.
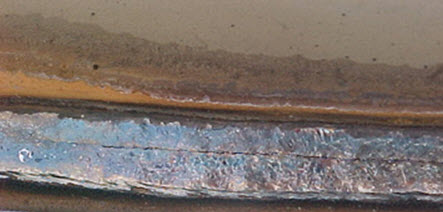
Top view of a centerline crack. Sometimes these cracks are barely visible to the naked eye and thus non-destructive inspection methods like liquid dye penetrant are used.
The molten puddle will solidify from the outside towards the middle of the weld. If the weld is too deep compared to its width it will trap low melting point elements in the middle of the weld regardless of whether or not the amounts in the base material are within specifications. This is referred to as bead shape induced cracking. The picture below shows how the weld bead solidifies.
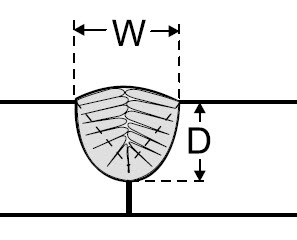
The same way in which water in a glass freezes the weld puddle solidifies from the outside edges towards the middle. Tramp elements are sometimes caught in the middle causing cracks.
To prevent hot cracking we want to do the following:
- Have proper width to depth ratio on weld beads (1:1 to 1.4:1 is ideal). Sometime joint redesign is needed to accomplish this.
- Select base materials carefully.
- Select the right process. Processes like SAW which provide the best penetration can sometime be an issue depending on the joint details.
Cold Cracking
Cold cracking is much worse than hot cracking simply because it may be hours or days before the crack appears. This means the welded assembly may already be out the door and in service. Cold cracking is characterized by a crack starting on the base material and not on the weld as is the case with hot cracking. It is sometimes referred to heat affected zone (HAZ) cracking or hydrogen assisted cracking.
Cold cracking occurs when three conditions are present: enough sensitive material involved, sufficient level of hydrogen, and a high level of residual stress. We typically have little control over the level of residual stress so the goal is to control the other two variables.
High cooling rates and materials with high carbon content create conditions susceptible to cold cracking. The faster the cooling rate the more likely we are to get cold cracks. Things like greater base material thickness, low heat input procedures and colder base metal temperatures all increase the cooling rate. High cooling rates create martensite in the HAZ which is hard and brittle. It also has lower ductility than the weld and the rest of the base material therefore shrinking at different rates as the weld cools. Hydrogen finds its way into the martensite and when stress is applied the crack occurs. Hydrogen eventually leaves the HAZ and weld metal; this is why the D1.1 Structural Code requires inspection to happen 48 hours after welding. This insures that the hydrogen will be gone from the welded structure in steels sensitive to hydrogen assisted cracking by the inspection is done.
To prevent cold cracking we want to do the following:
- Preheat the base material to slow the cooling rate – this also diffuses hydrogen and will allow the weld bead and the base material to contract at a similar rate when cooling.
- Run higher heat input procedures if preheating is not an option
- Select low hydrogen filler metals (typically have the designation H2, H4 or H8)
- Do post weld heat treatment (hydrogen bake off)
- Reduce the cooling rate by using heat blankets
There are other types of cracking that are caused by issues not mentioned here. Have you experienced problems with welds cracking?
Source: Fabricators’ and Erectors’ Guide to Welded Steel Construction
Please note: I reserve the right to delete comments that are offensive or off-topic.