Category Archives: Processes
Troubleshooting Welding Burn-through
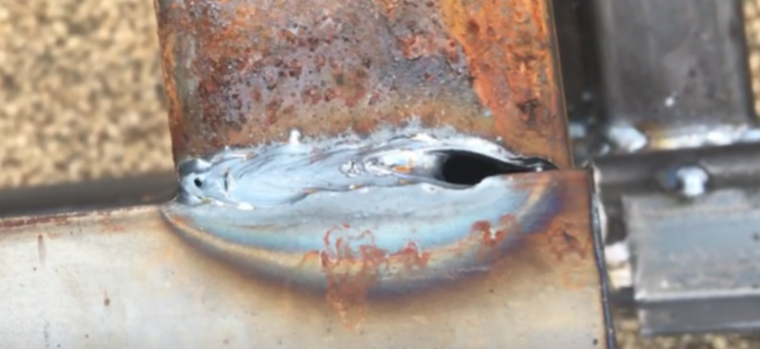
Burn-through is a common defect in welding of light gauge materials. It is typically results in costly scrapping of parts since it can be difficult to fix. Or, if left in place when there are not structural integrity concerns it looks awful and portrays extremely poor quality. The following is an excerpt from our guide: […]
7 Things to Consider When Choosing the Best Welding Process for your Welding Procedure
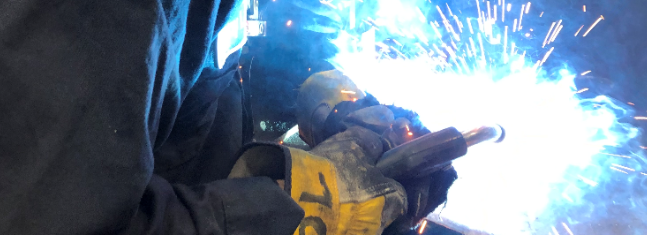
Selecting the best welding process is a critical step in developing a welding procedure that attains the desired quality and optimizes productivity. Many times we look for the welding process that can give us the highest deposition rate to optimize productivity. However, every welding process has limitations. For example, submerged arc welding (SAW) has extremely […]
How to Weld Cast Iron
Avoid cracking by following these recommendations
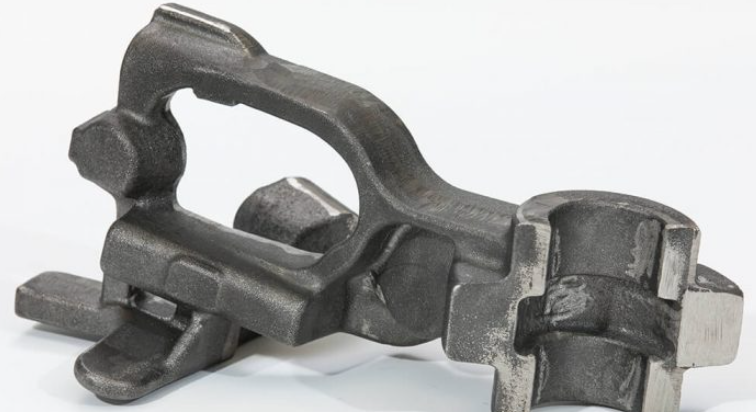
Cast iron is not impossible to weld, although many that attempt to do so end up with cracked welds. The reason welding cast iron is a big challenge is that it contains up to 4% carbon. This is an insane amount, considering that any material with a carbon content above 0.30% is already considered “medium […]
Which Welding Process Produces the Strongest Welds
SMAW, GTAW, GMAW, FCAW, MCAW or SAW?
The Importance of Weld Repair Procedures
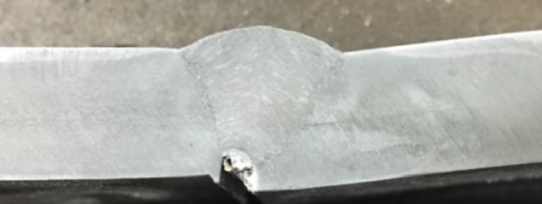
A repair procedure is necessary any time there is a defect in welding that must be corrected. The repair procedure is not just a welding procedure specification, but rather a set of instructions and rules on how to repair different types of defects. There is no standard format for a repair procedure, or a standard […]
AWS D1.1 Prequalified Welding Procedures
Prequalified WPSs for GMAW, MCAW, SMAW, FCAW & FCAW-S
Prequalified welding procedures must adhere to the strict requiremnts of the welding codes which permit their use. AWS D1.1 Structural Welding Code (Steel) is one that allows their use. Prequalified WPSs are exempt from testing becasue there is reasonable assurance that as long as all the requirements are met the deposited weld will be sound […]
7 Reasons to Consider Stick Welding Over Other Processes
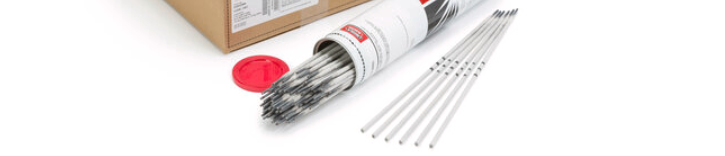
Shielded metal arc welding (SMAW), or what is commonly referred to as “stick welding,” is one of the oldest welding processes. Despite being one of the first welding processes developed, it remains one of the most used welding process worldwide. If you have been working in a fabrication shop for years using advanced GMAW (mig) […]
3 Ways to Improve Out of Position Welding

Welding out of position does not need to be overly complicated. It does present a challenge, especially for inexperienced welders, but there are things we can do to make this go well for everyone. When we talk about out of position welding we mean welding vertical up or overhead. Vertical down is also out of […]
Storing and Re-drying Low Hydrogen Electrodes
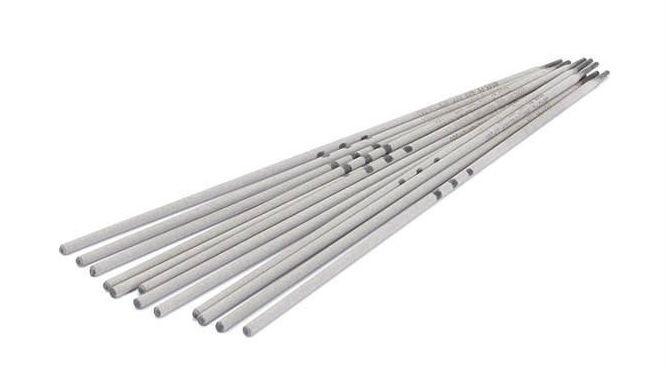
One of the dangers we should be aware of when welding high strength steels or even thick sections of low carbon steel is hydrogen induced cracking. Hydrogen induced cracking, also called hydrogen assisted cracking and cold cracking, is caused when three conditions are present. First, we need a susceptible microstructure (base material related). Second, we […]