Understanding the Difference between Qualified and Prequalified Welding Procedures
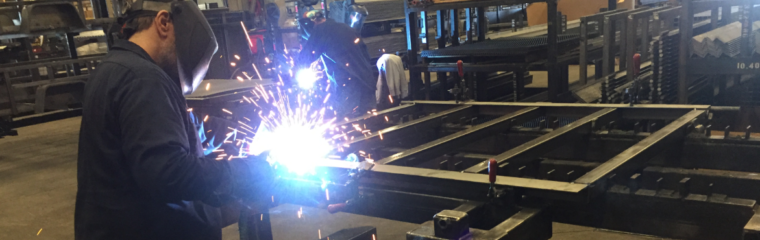
One of the most common questions we get around the topic of welding procedure qualification is regarding the differences between qualified and prequalified welding procedures. The main question is typically: is one better than the other? Before we answer this question, let’s first discuss the need for qualified, or prequalified, welding procedures. If you have […]