Special considerations for welding Stainless Steel

Stainless steels possess many properties that make them different from those of carbon steels. These differences provide certain advantages, such as corrosion resistance, but we must be aware of some of the intricacies of welding stainless steel to avoid problems. Many welding professionals, including welding engineers, that have worked primarily with carbon steels develop welding […]
How to write AWS D1.1 Prequalified Welding Procedure Specifications
Troubleshooting Welding Burn-through
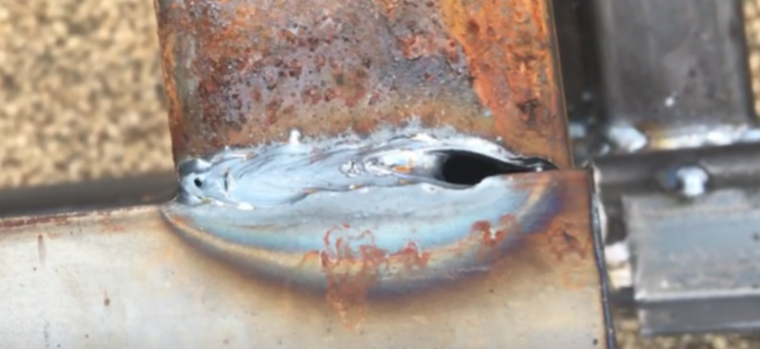
Burn-through is a common defect in welding of light gauge materials. It is typically results in costly scrapping of parts since it can be difficult to fix. Or, if left in place when there are not structural integrity concerns it looks awful and portrays extremely poor quality. The following is an excerpt from our guide: […]
Understanding the Difference between Qualified and Prequalified Welding Procedures
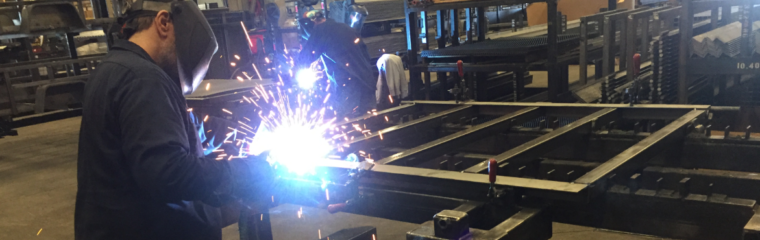
One of the most common questions we get around the topic of welding procedure qualification is regarding the differences between qualified and prequalified welding procedures. The main question is typically: is one better than the other? Before we answer this question, let’s first discuss the need for qualified, or prequalified, welding procedures. If you have […]
The Importance of Contact Tip to Work Distance in GMAW
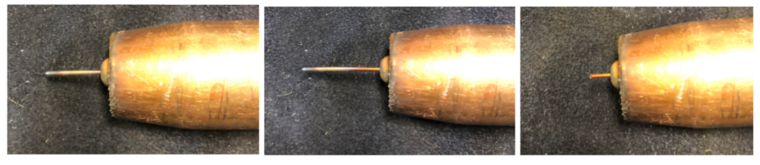
If you look at any of the structural welding codes you’ll notice that contact-tip-to-work-distance (CTTWD) is a variable which must be listed in welding procedure specifications (WPSs). However, it is not an essential variable, meaning that changes to CTTWD of any amount do not require requalification. This can seem puzzling to some, especially those […]
Key Components of Effective Welder Training Programs
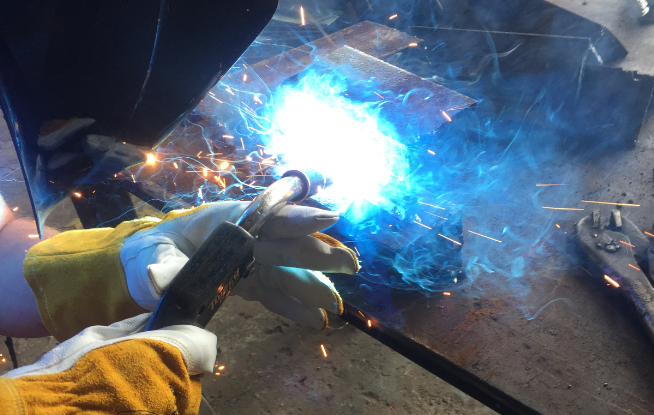
Continuous learning is something that is very important for both personal and professional development. This applies to all industries and to all positions. The welding industry, as many of its counterparts, is challenged with a workforce that is lacking the skills necessary to do the job. This is driven by the increased demand for welders, […]
The Challenges of Welding in Cold Temperatures
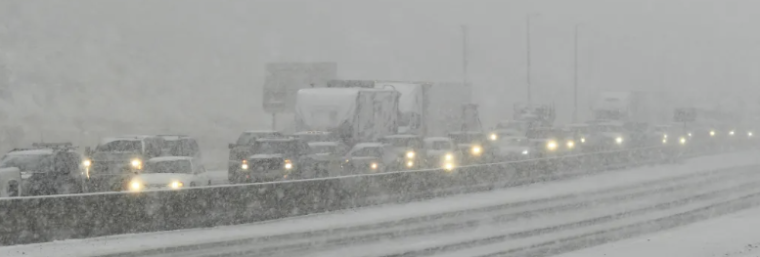
Welding in cold temperatures poses two critical challenges. First, the brutal conditions welders must endure and second, the performance of steel structures in cold temperatures. Many times we forget about the former by focusing too much on the latter. If you ever get a chance to talk to welders that have welded in both extreme […]
Who is responsible for determining weld size?
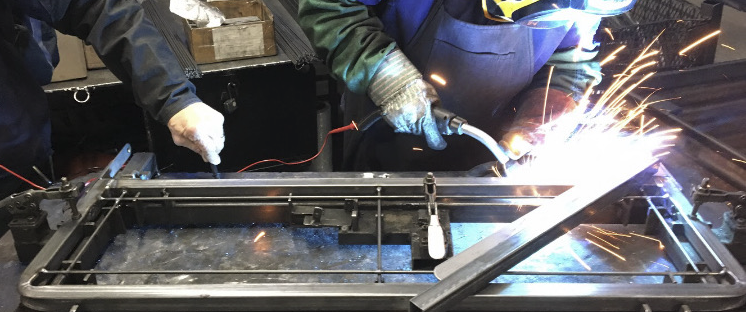
Who determines what size a weld should be? This is a question we ask many of our customers. And we never seem to get a straight answer. In a perfect world, the design engineer should specify all weld sizes and clearly communicate this through welding symbols on the print. But that is hardly ever the […]
Demystifying Fatigue Fractures in Welding: The 3 Stages of Fatigue Fracture
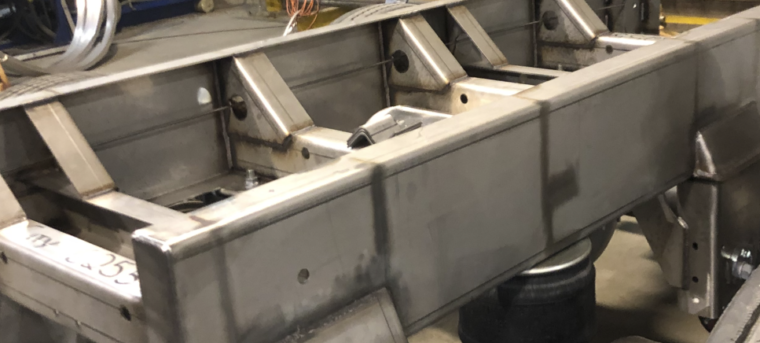
In today’s article we’ll be discussing a critical aspect of welding which is crucial in ensuring the safety and long useful life of structures. When engineers conduct a fitness for service analysis of structures they are looking for flaws. These flaws may be cracks, loose bolts, deformations, rust damage (thinning of structural members) and other […]