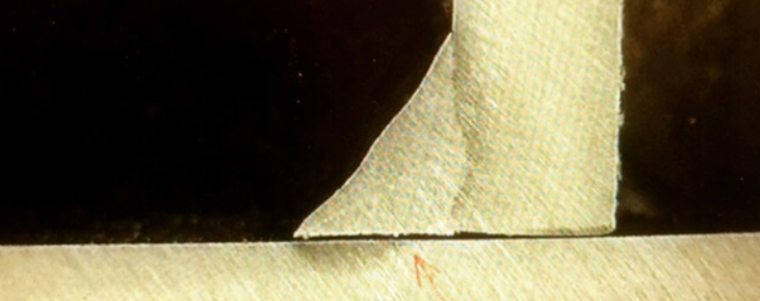
Maintenance-related problems are responsible for a large portion of bad welds in every day welding. However, these causes go unnoticed and unresolved because they happen slowly over time. A proper preventive maintenance program for welding machines, CNC cutting tables and other industrial equipment is absolutely necessary.
Many of the problems related to maintenance that cause bad welds are ones which can be easily fixed, but you need to perform a check of your welding system regularly in order to do so.
Below are 9 of the most common maintenance issues we see out there which are costing our clients a lot of money in the form of downtime.
- Damaged or frayed work connections – If you read the owner’s manual of any welding power source you will find an installation section which details the size of cables you need. If the manual calls for a 4/0 welding cable (0.46’ diameter) you would not use a 2/0 (0.37” diameter). If you use an undersized cable it may not be able to efficiently allow for the flow of current and start overheating. When this happens you lose voltage in the form of heat. In some cases a drop of 3 to 4 volts as the day progresses is common.
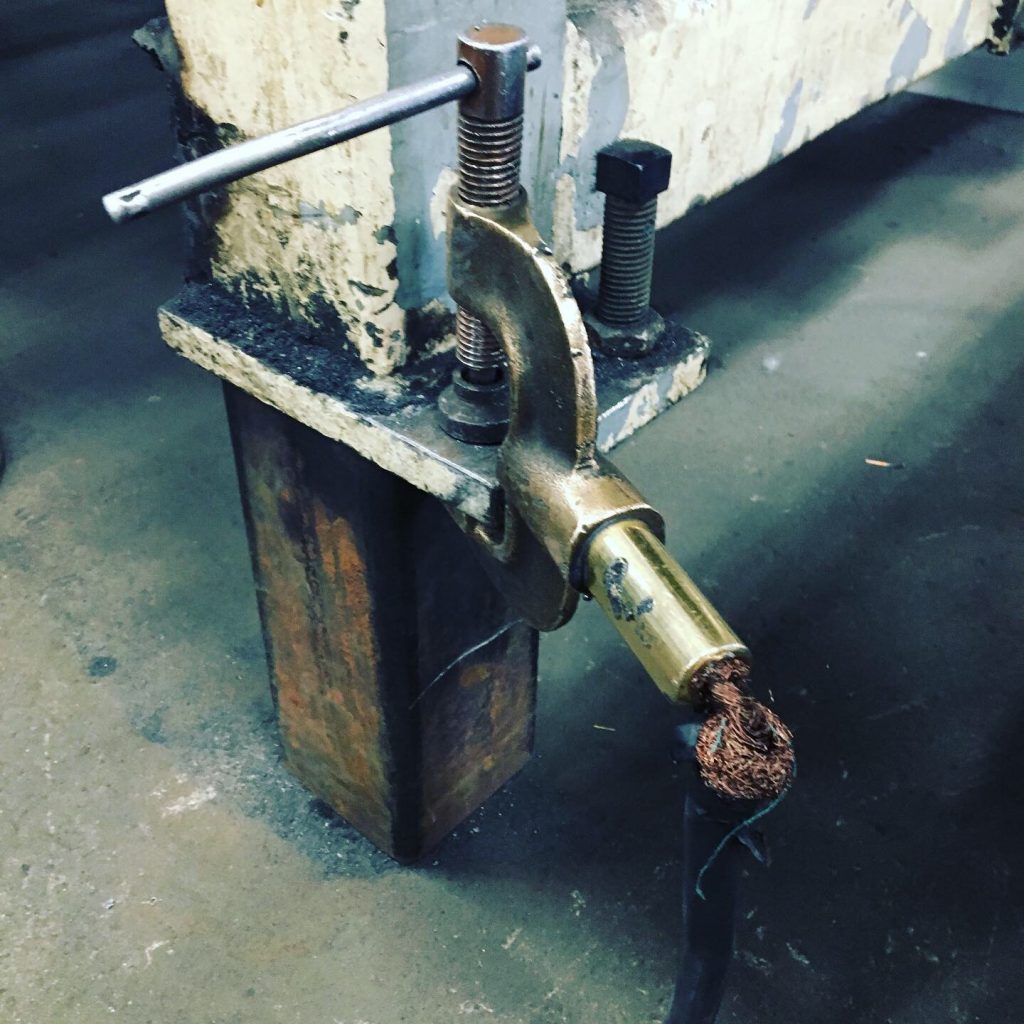
Frayed cables reduce the current carrying capacity of work and electrode cables creating a voltage loss.
When the copper strands on a cable are fray it effectively reduces the cross sectional area and thus the amount of current it can carry without overheating. This occurs often in areas where the cable is constantly bent back and forth, as in the case of the work connection. If you have any of these in your shop the fix is easy, cut the cable and reattach to the work clamp properly.
- Worn drive rolls – Another issue that is hard to notice because it is hidden inside the wire feeder is a worn drive roll when using a wire process such as GMAW or FCAW. The grooves on the drive rolls are of a specific size depending on the diameter of wire you are running. When the groove wears out the wire will start slipping causing feeding issues. These feeding issues lead to erratic arcs and excessive contact tip usage.
- Excessively worn contact tips – The opening of a contact tip is larger than the diameter of wire it is meant for. However, if this hole gets much bigger it may cause the wire to be fed through the tip without making contact. When this happens the arc is extinguished immediately followed by it being bent and arcing inside and seizing the contact tip. This problem is more common when using an oversized tip (say using an 0.052” tip for 0.045” wire), but can be seen often in automated applications where a groove begins to be carved on the contact tip.
- Loose connections – work and electrode cables need to be tightly connected to lugs, Dinse connectors or quick disconnects. The best connection is one that has a large contact area and which is tight. Loose connections, such as a lug coming loose on the output studs of a power source, will create arcing and an erratic arc which in turn leads to bad welds. In some cases the loose connection will overheat and fuse itself, making it impossible to remove and causing the welding machine to be down and in need of repair.
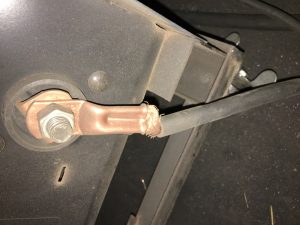
Ensuring all connections are tight is necessary to prevent arcing and damage to welding power sources and feeders
- Gas leaks – Welding shops are so loud that we never hear gas leaks. Having leaks in the pipes of your bulk gas delivery system is normal and typically not much of a concern. When it is a problem is when these leaks are severe and cause a significant lack of shielding gas at the arc. Leaks due to a loose connection of the backend of your welding gun to the receiving bushing on the feeder can make you lose all gas coverage and cause porosity. Sometimes the connection is tight but the O-rings are worn or missing causing leaks.
- Dirty machines – fabricating facilities generate a lot of welding fumes (metal particulate), grinding dust, shavings and other airborne particles. Welding machines have fans that suck shop air in to cool it down. When doing, these machines suck all the airborne particles in as well. If machines are not blown out (using compressed air, preferably with the sides off) there is the potential for arcing of electrical components in boards which can ruin a machine. Additionally, the thick layer of dust and metal shavings act as an insulator which reduces the machine’s ability to cool down properly.
- Undersized cables – As discussed in item one above, undersized cables will not be able to efficiently carry the current necessary. Many times when we replace cables we use what we have on-hand. Make sure you are using the size of cable specified by the manufacturer of the power source. Keep in mind that if you increase the length of the cable the size (diameter) should also be increased.
- Damaged work clamp – damaged work clamps prevent adequate contact and reduce contact surface area. This leads to the generation of heat and loss of voltage.
- Damaged/kinked liner – Liners are a consumable part, you should not try to get 2 years out of one liner. At the first sign of feeding issues you should consider changing the liner after all other potential feeding issues have been resolved.
REFERENCE: Weld Troubleshooting for Non Welding Engineers
Weld Troubleshooting for Non Welding Engineers goes beyond your typical troubleshooting charts on the back of an owner’s manual. The goal is not just to help you solve a welding problem, but to teach the concepts and theory behind it. Understanding why a recommended solution worked is just as important as solving the problem.
This guide addresses the most common weld discontinuities and defects as well as the most common welding equipment problems.
Reduce your downtime associated with troubleshooting welding defects and welding equipment problems by quickly identifying the causes and implemeting the recommended solutions. This guide will save you money and increase your productivity. Use it as a training tool increase the knowledge level of your welding personnel.