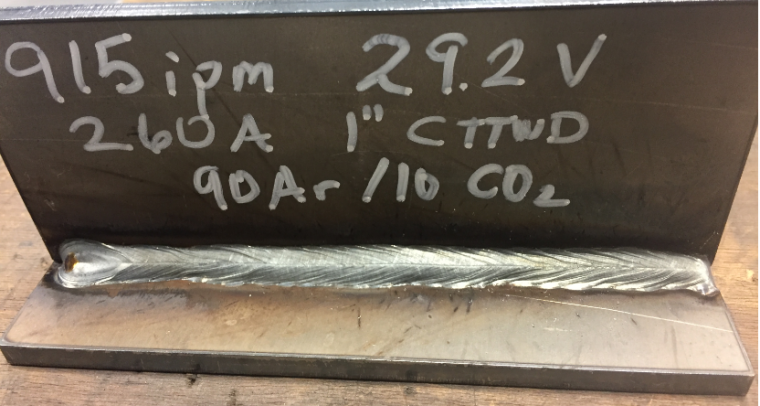
Before getting into today’s topic we wanted to make you aware of a new resource we are creating and which will be available soon. Prequalified Welding Procedures for Steel Fabricators will provide a list of prequalified procedures written in conformance with AWS D1.1 Structural Welding Code which can be used in the fabrication of carbon steel structures. To learn more about what this publication will include click here.
Now on to the topic at hand: the eight most common mistakes made when developing and using prequalified welding procedure specifications.
Codes such as AWS D1.1 (Steel), AWS D1.3 (Sheet Metal) and AWS D1.6 (Stainless Steel) permit the use of prequalified welding procedures (WPSs). A prequalified welding procedure is exempt from the testing requirements mandated by the qualification clauses in these codes. This exemption can save the fabricator thousands of dollars. The qualification of a single welding procedure specification can cost more than $1,000 since a lot of testing is required. The tests required by AWS D1.1 to qualify a welding procedure include:
- Visual inspection
- Bend tests (groove welds)
- Macroetch tests (fillet welds)
- Fillet Break test (fillet welds)
- Reduced section tension test
- Ultrasonic or radiographic testing
In addition to the testing costs you have the costs of having your personnel tied up doing these tests instead of being in production. If a particular job requires 15 different welding procedures you may save as much as $20,000 simply by using prequalified welding procedures.
Unfortunately, you cannot just open any of these structural welding code books and find a written prequalified WPS. You have to develop the prequalified WPS in accordance with the requirements and limitations set forth in these codes. Here is where many go wrong and develop a prequalified WPS that violates code requirements creating issues if audited, but more importantly creating potential quality problems.
Below are the most common mistakes made when developing prequalified welding procedures.
- Using a welding process that is not allowed for use in prequalified WPSs. An example of this is using gas tungsten arc welding (GTAW). Although GTAW produces a high quality weld it is not allowed for use in prequalified WPSs per AWS D1.1 Structural Welding Code – Steel. However, AWS D1.6 Structural Welding Code – Stainless Steel does allow the use of GTAW for prequalified WPSs.
- Not staying within the operating parameters specified by the manufacturer of the filler metal. If you look at the specification sheet of a common ER70S-6 wire you may find that the manufacturer provides typical operating procedures. If they list a wire feed speed range of 175 – 475 in/min for an .045” wire for spray transfer as seen in the image below, but you specify 150 – 300 in your prequalified WPS you are violating one of the requirements in Table 5.1 of AWS D1.1 (2020) – Prequalified WPS Requirements due to the low end of your procedure.
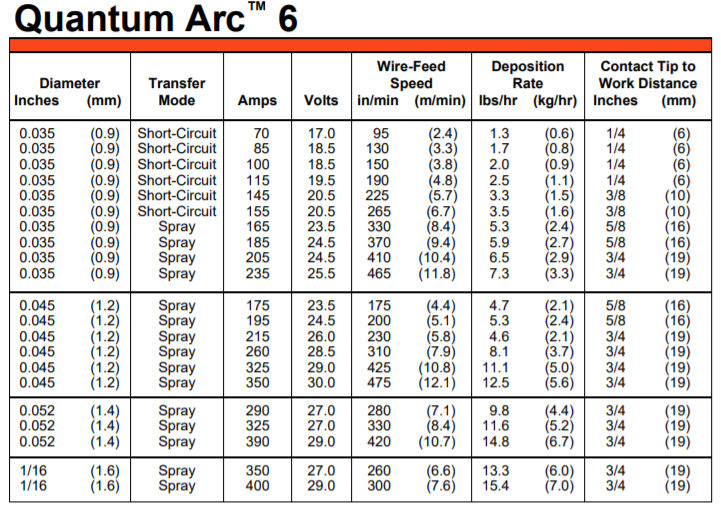
The parameters used in a prequalified WPS must be those recommended by the manufacturer of the filler metal.
- Not staying within the dimensional tolerances provided in the prequalified joint details. A common example of this is using a prequalified WPS on a complete joint penetration groove weld with a 30-degree included angle and no root opening. These dimensions will violate most of the requirements for a prequalified joint. Typically a 30-degree included angle will require a root opening of 3/16-in or more depending on the welding process being used.

In order to use prequalified WPSs you must stay within the joint dimensional tolerances specified by the structural welding code.
- Failing to understand basic welding process principles. GMAW-S (short circuit transfer) is not allowed for prequalified WPSs according to AWS D1.1. So a prequalified WPS may use parameters that assure spray transfer. The WPS is then written to be used in all positions. If you have tried running GMAW spray transfer out of position you know it is close to impossible to do unless you have a power source capable of pulsing. This mistake does not violate any of the code requirements for prequalified WPSs, but it cannot be used in production.

AWS D1.1 provides limits on the maximum size of a fillet weld as well as maximum thickness of a root and fill pass based on the welding process and welding position.
- Failing to apply proper preheat and maintain adequate interpass temperature. The prequalification clause of AWS D1.1 provides the necessary preheat and interpass temperature for different structural steels based on their chemical composition and thickness. These are necessary to prevent hydrogen induced cracking (cold cracking). Failing to abide by these requirements constitutes a violation of the code, but most importantly can lead to catastrophic failure.
- Using a prequalified WPS on a carbon steel not listed in the code book. AWS D1.1 has a table where it lists all of the steels that can be used with prequalified WPSs. If the particular steel you are using is not listed you absolutely cannot use it with a prequalified WPS. You may still be able to use it but it must be qualified by testing and approved by the engineer in charge.
- Welding vertical down. Downhill progression in vertical welds is prohibited by AWS D1.1 for use with prequalified WPSs with a couple of exceptions:
- When repairing undercut
- When welding in tubular structures and the welder is qualified for downhill welding
These are just the requirements that are commonly violated. There are many more. The reason for all these requirements is that we are not testing our welding procedure, so we must comply with all requirements to ensure we deposit a quality weld. If we get too relaxed with the requirements chances are we will produce substandard quality. If you plan on using prequalified WPSs make sure you understand the code requirements. This may seem like a lot of work, but once you get familiar with the qualification clause and develop a few prequalified WPSs it will become second nature.
If you hire someone to write prequalified WPSs for you make sure they have a thorough understanding of the requirements set forth by the applicable structural welding code.
Are you looking to qualify welding procedure and/or welders? Are you using AWS D1.1 Structural Welding Code -Steel as your quality standard?
“Qualifying Welding Procedures, Welders and Welding Operators” is a guide developed to help you perform your own qualifications in full compliance to AWS D1.1 Structural Welding Code. It provides step-by-step instructions on how to qualify welders and welding procedures. It also provide step-by-step instruction on the proper use of prequalified welding procedures.
Are you in need of AWS D1.1 prequalified welding procedures? This collection provides welding procedures for several arc welding processes. These procedure cover 14 of the most common welding joints, all positions and the most common wire diameters for each process.
Did you find this article useful?
Subscribe to Welding Answers and get our latest content by email for FREE every week.
Hi , is it necesary to qualify a welder under a prequalified Welding Procedure?
The proper way is to used a qualified Welding Procedure. The procedure can be qualified by testing or it may be prequalified. The code (AWS D1,1) does not specifically say that the WPS must be qualified, but it does say that the welder must follow and WPS applicable to the qualification test required. So, we definitely recommend that the WPS use be qualified or prequalified.
Sorry, I am questioning #1. I can show you at least a few GTAW on CS SWPS
You are correct, you can find them in SWPSs (Standard Welding Procedure Specifications), but NOT on prequalified WPSs as allowed by AWS D1.1 as the article reads.