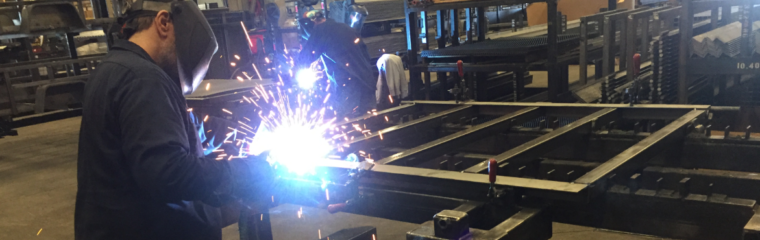
High carbon steels are those containing 0.45% carbon or higher. They are typically considered “hard to weld” because they are crack sensitive and are susceptible to undergoing significant changes in their physical and mechanical properties after welding. However, high carbon steels can be welded successfully and without problems by having a sound understanding of the properties of high carbon steels that make different welding procedures necessary.
Understanding these properties, understanding the problems associated with high carbon steels, and knowing the rules to follow will help you weld these steels without problems.
Properties of high carbon steel and their effects:
- High carbon steel will not stretch as much as low carbon steel
- High carbon steels harden significantly more than low carbon steels at a given cooling rate
- High carbon steels have a lower transformation range than low carbon steels which results in a deeper heat affected zone (HAZ)
- High carbon steels are more susceptible to porosity than low carbon steel since more carbon is available to react with other elements and form gases under some welding conditions
The above differences in high carbon steels as compared to low carbon steel give rise to a variety of problems.
The main problems with welding high carbon steels are:
- Cracking of the weld metal – driven by the expansion and contraction during welding on a base metal (high carbon steel) that doesn’t stretch very much. Differences in expansion rates between weld metal and base metal can lead to cracking.
- Porosity – as explained above, there is more carbon available to form more gases.
- Excessive hardening of the base metal – when cooling rates are high, the excess carbon facilitates the hardening of the weld and HAZ.
- Cracking of the base metal (primarily in the HAZ) – if excessive hardening occurs the resulting microstructure is very susceptible to cracking due to its low ductility. This is made worse with the presence of hydrogen (using a non-low hydrogen welding process). The high strength of the base metal will also provide a high enough level of restraint to promote cracking.
- Excessive softening of the base metal – in order to weld high carbon steels we need to apply preheat to slow the cooling rate. When we do this we may reduce the hardness of the base metal which in many cases is desired due to its intended service. At times these high carbon steels have been quenched and tempered. By having a slow cooling rate (desired to avoid cracking) the adjacent base metal will soften.
Rules for welding high carbon steels
Rule 1 – Avoid excessive penetration. When we weld high carbon steels we almost always will be using an undermatching filler metal, that is a filler metal with lower tensile strength than the base metal. We do this in order to have a ductile weld that will not be stressed to the point of fracture.
Even with an undermatching filler metal we may still end up with a weld that has low ductility if we pick up enough carbon from the base metal. This can happen if we have deep penetration. The goal should be to assure fusion to root and side walls but not much more than that. This can be a dangerous game to play as we would then be susceptible to lack of fusion. So make sure that your welding procedure is properly qualified and keep your amperage, voltage and travel speed ranges very tight.
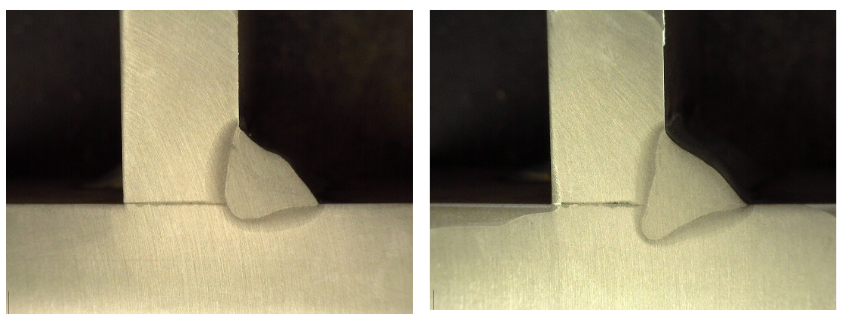
Deeper penetration as seen on the image on the right allows for more admixture (mixing of the base metal with the filler metal). This increases the carbon content in the weld which makes it increase in strength and hardness while losing ductility.
Rule 2 – Use undermatching filler metals when permitted. As stated above, we want to use undermatching filler metal to have a ductile weld that will have some “give” in order to avoid cracking. If you are making partial joint penetration (PJP) welds or fillet welds, the use of undermatching filler metal is probably OK. Additional load carrying capacity may be gained by making the welds bigger without using much or any ductility.
If you are making complete joint penetration (CJP) welds then the use of a matching filler metal may be required.
Rule 3 – Deposit large weld beads. The highest heat input possible is desired when welding high carbon steels. This will slow the cooling rate down and prevent hydrogen induced cracking. Weaving is preferable to using stringers so weave when possible.
Rule 4 – If welding on quenched and tempered (Q&T) steels anneal before welding. This may not be possible, but if you can you should anneal the base metal before welding. The reduced strength will be much less susceptible to cracking. After welding the finished product may be post weld heat treated in order to regain the original mechanical properties.
Rule 5 – Develop, qualify and follow a welding procedure specification (WPS). As you should be able to tell by now, extreme care must be taken when welding high carbon steels. These steels are not very forgiving. Once you have determined a way to successfully weld these high carbon steels you must document it so that this same procedure may be followed in the future.
The developed welding procedure should be very specific as to what filler metal will be used, what preheat and interpass temperature is required (minimum and maximum) as well as what kind of post weld heat treatment is necessary. This post weld heat treatment may be as simple as cooling the part slowly or more involved requiring quenching and tempering.
References:
Steel Design Guide 21: Welded Connections – A Primer for Engineers
Welding Metallurgy and Weldability by John C. Lippold
hi, I am trying to solder(iron) two pieces of hcs (like exacto knifebade thin) together with varying results
.. any tips on how to stabilize and strengthen the weld would be much appreciated
The key is to maintain consistent heat input and consistent travel speed. Anything that makes these two variables inconsisten will provide inconsistent results. If you have access to a TIG (GTAW) welding machine you can use that process which will make this a lot easier.
What a wonderful experience. Thank you very much