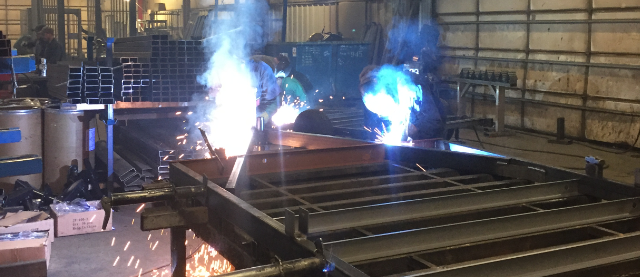
Our previous article discussed the importance of having a specification for weld quality. In this article we’re talking about the importance of one of its basic components: Welding Procedure Specifications (WPSs). Many fabricators don’t have WPSs. They rely in the experience of their welders to select the right parameters. As much as we want every fabricator to have written WPSs not all of them will. Some have been getting by without WPSs for many years and will continue to do so. But everyone must pay attention to what is at stake.
Most fabricators that have and use WPSs are required to do so by their customers. This could be a product of the industry they are in or because these customers want assurance that the fabricator’s work will meet a minimum quality level. So if you are not required to use WPSs why should you consider having them?
A welding procedure can do so much more than simply help you with the documentation needed to land a contract or defend an audit. Here are the areas of welding operations that a WPS will have a definite impact on.
- Productivity – A WPS specifies values for wire feed speed and/or amperage amongst other variables. These values will determine the deposition rate which in turn determines how fast you weld. Consider a shop that runs 0.045” solid wire for GMAW and multiple welders. If no WPSs are followed then the welders will default to procedures that they feel comfortable with. Some welders may run this wire at 200 inches per minute while others will feel comfortable running it at 500 inches per minute. The deposition rates for these wire feed speeds are 5.3 lb/hr and 13.1 lb/hr respectively. This means that the cost per foot of weld produced by one welder may be twice as much, if not more, than that of another.
Of course this may also be a problem with a WPS with large ranges. This can sometimes be an issue with prequalified welding procedures. Prequalified WPSs allow you to run any parameters (wire feed speed/amperage and voltage) so long as they fall within the recommendations of the manufacturer. An 0.045” ER70S-6 electrode will be in short circuit transfer (not allowed for prequalified WPSs) up to a wire feed speed of about 175-200 in/min depending on shielding gas selection and voltage. This means that you can probably run a wire feed speed of 200 to 550 for most brands of this type of wire. So even though you have a welding procedure you may still have that huge swing in cost per foot of weld from one welder to another. The key is to select a tight range which maximizes quality and productivity. Less skilled welders should work up to being able to run the higher wire feed speed comfortably.
- Quality – Welding codes such as AWS D1.1 provide instruction on how to qualify welding procedures and welder performance. The premise behind doing this is to ensure quality. Acceptance criteria are provided and must be met in order to perform code work. The idea behind a qualified welding procedure is that it will produce identical results day in and day out. The only variable should be the skill of the welder. With the proper performance qualification tests we can then be assured that the welders will be able to take the qualified WPS and turn it into sound welds.
- Cost – It should go without saying that fabrication costs will decrease if our productivity and quality increase. Producing parts faster with lower rework rates will positively impact the bottom line.
- Training time – When new welders start working, having WPSs in place will help them understand the requirements and more quickly adapt to what is expected. This is even more important with new welders that are less skilled. Rather than having them struggle trying to figure out the best procedure why not provide that from the start?
- Avoiding BIG mistakes – The wonderful thing about welding low carbon steel such as ASTM A36 is that it is extremely forgiving to welding variances. But what if you are welding a medium carbon steel such as AISI 4140? Is this one you want to rely on your welder’s experience to figure out? Plenty of welders can tell you exactly how to weld 4140. They can tell you what preheat to apply for a given material thickness, what interpass temperature should be maintained, what kind of cooling rate is necessary, what filler metal to use for joining to low carbon steel, what filler metal to use when welding 4140 to 4140, and what filler metal to use when post weld heat treatment is to be carried out for the purposes of achieving certain hardness and/or strength levels. However, this is a decision that should be the responsibility of your engineering department. You may be lucky to have experienced welders that know this, but will know how to weld everything that comes into your shop?
The biggest problem with 4140 is that it looks just like A36 steel. It also welds the same. However, it is very susceptible to cracking if an adequate welding procedure is not used. If you are not following an adequate welding procedure you have a big problem staring to brew. If you’re lucky, the weldment will crack while still in the shop. If you’re unlucky, it will not crack and you may be sending out a product that will be very susceptible to failure due to excessive hardness and/or very low impact properties. Or susceptible to failure because the welding process lowered the tensile strength significantly.
Failures, sometimes catastrophic, may occur if adequate WPSs are not followed when welding certain base metals. Here are few of the mistakes which can be made when not WPSs are in place.
- Running a flux-cored wire such as an E71T-1 with a high argon content such as 90/10 (Argon/CO2). Most flux-cored wires cannot be run with more than 75% argon. Some are designed exclusively for use with 100% carbon dioxide. If you run 90/10 you significantly increase susceptibility for cracking due to excessive strength/hardness.
- Failing to preheat – medium to high carbon steels need to be preheated, but so do low carbon steels above certain thicknesses. In some cases you can compensate for lack of preheat with a welding process and procedure that produces high heat input, but how can you be sure it is enough? Failing to preheat will cause fast cooling rates which increase hardness and facilitate cracking.
- Exceeding interpass temperature – Low carbon steels that require a minimum preheat and interpass temperature typically don’t exhibit any issues if a certain interpass temperature is exceeded. However, other carbon steels such as high strength steels can be negatively affected with high interpass temperatures. ASTM A514 is a prime example. If you exceed the maximum interpass temperature you will be softening the heat affected zone and hurting its in-service performance.
- Using the wrong filler metal – We know we must weld carbon steel with carbon steel electrodes, stainless with stainless electrodes and aluminum with aluminum electrodes. But what about more subtle instances like welding 304 stainless to carbon steel? Should we use a stainless wire or a carbon steel wire? If we use stainless should it be 308, 309 or 316? What about welding 304 stainless to 316? Should it be 308, 309 or 316? If you use the wrong electrode you may end up with premature rusting which can increase warranty costs. You could also end up with a deposit that may be susceptible to cracking.
If we are lucky, the problems above will manifest themselves as cracks or other defects while the products are still in our facilities. Or, our inspector may find out something was not done properly. Unfortunately, that is not always the case. When we make the mistakes above we’ll find out several months later when our customers call us with problems. We have helped countless fabricators perform failure analysis in their failed parts. The majority of the time they come to us to help them prove that the failure was due to customer abuse; however, this isn’t always the case.

The microstructure of a weld and the heat affected zone is a product of the base material composition and the heat effects of the welding process and cooling rates.
When we come in to perform failure analysis, the first thing we ask for is a copy of the welding procedure that was followed while welding the part that failed. This will give us insight as to whether or not there could be an issue with our welding process that caused the failure. If there is no WPS in place then we rely exclusively on interviews, asking welders and supervisors to remember how they welded a specific part 6, 12 or 24 months ago. As you can imagine this information is not always reliable.
Some failures unfortunately end up going to court due the huge losses that are incurred. A fabricator that has no way of showing the processes and procedures that were used will have a hard time proving they did things correctly. In this case, it doesn’t matter if their customer required qualified WPSs or not. At this point the fabricator must prove they were not negligent. It is sometimes an uncomfortable conversation to have with our customers. But, just like writing your will in case of an untimely death, you must also have all the documentation if something where to fail and you have an upset customer demanding compensation. Ideally, the WPS will prevent you from getting to this place.
Need help qualifying welding procedures specification to AWS D1.1 Structural Welding Code? Or are you evaluating the use of prequalified welding procedures to save time and money? If so, take a look at Qualification of Welding Procedures, Welders and Welding Operators. This guide has helped hundreds of users navigate the requirements of AWS D1.1 to comply with qualification requirements.
Please note: I reserve the right to delete comments that are offensive or off-topic.