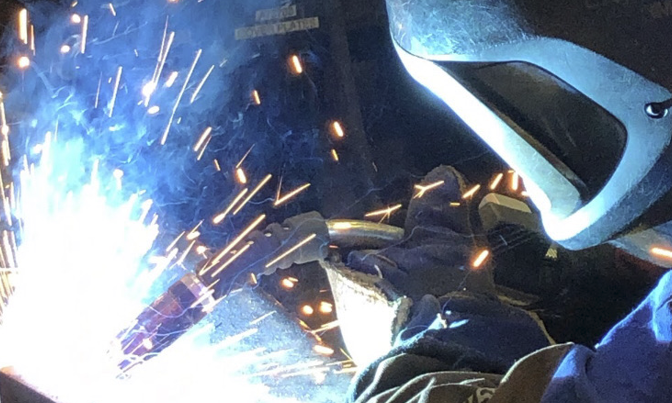
When a weld fails in the field, the consequences can be catastrophic. Our experience as welding engineering consultants has shown us that such failures often expose deeper issues within a company’s welding operations. These situations can lead to fears of additional failures in other products or structures, potential harm or fatalities, litigation, and even bankruptcy. For some businesses, these failures serve as a stark reminder that shortcuts taken in the past are now becoming serious, costly problems.
Many welding operations that experience failures have relied on the reasoning that “nothing has ever failed before,” using this assumption to justify the absence of proper quality control measures. However, this mindset can lead to devastating consequences. Common shortcuts we’ve encountered include:
- Disregarding the creation of internal welding quality standards
- Not qualifying welding procedures
- Failing to qualify welders’ performance
- Lacking a proven process for weld inspection
- Overlooking the need for proper welder training programs
When we receive calls from fabricators in crisis, our first priority is to identify the cause of the failure and determine whether similar failures are likely in other welded products or structures. The process begins with a failure analysis.
The Failure Analysis Process
Failure analysis starts with collecting data and conducting interviews with welders, supervisors, quality control (QC) personnel, owners, and anyone else involved in welding operations. Key pieces of information we request include:
- The welding procedure used for the failed weld
- The welder performance qualification record of the individual who made the weld
- The inspection log for the failed part
- The company’s quality control manual
Unfortunately, many fabricators lack these essential documents. In such cases, we explain that if this issue ends up in court, the absence of proper documentation almost guarantees liability. Beyond legal concerns, these missing documents make it difficult to pinpoint the exact root cause of the failure.
Identifying Deficiencies and Potential Causes
Even when documentation is unavailable, we can often identify several deficiencies in the fabricator’s processes that contributed to the failure. For example, evidence from the failure itself might indicate a specific failure mechanism, such as hydrogen-induced cracking. While understanding the failure mechanism doesn’t always reveal the root cause, it provides valuable clues and allows us to outline potential causes.
After completing our analysis, we provide the fabricator with a comprehensive list of recommendations. These recommendations are designed to address the deficiencies we’ve identified and prevent future failures.
Recommendations for Preventing Failures
- Develop a Welding Quality Standard Establishing an internal welding quality standard is foundational to improving welding operations. This standard should outline the minimum requirements for welding procedures, inspection processes, and welder qualifications.
- Qualify Welding Procedures Every welding procedure used in production should be qualified to ensure it can consistently produce sound welds. Properly qualified welding procedures account for variables such as welding parameters, joint details, welder technique, filler metal selection, preheat requirements, post weld heat treatment requirements and much more.
- Train and Qualify Welders A proper training program is essential for ensuring welders have the skills needed to follow qualified welding procedures. Once trained, welders’ performance should be tested and qualified according to established standards.
- Implement a Robust Inspection Process A proven inspection process is critical for identifying potential defects before they lead to failures. This includes visual inspections, non-destructive testing (NDT), and thorough documentation of all inspection activities.
- Address Specific Deficiencies Beyond these foundational recommendations, we provide specific instructions to correct the issues that likely contributed to the failure. For example, if the failure mechanism indicates hydrogen-induced cracking, we might recommend preheating procedures, improved material storage, or adjustments to welding parameters.
A Call to Action
Weld failures are preventable, but only if companies take proactive steps to improve their welding operations. Don’t wait for a failure to force your hand. Start now by:
- Developing and implementing a welding quality standard
- Qualifying your welding procedures and documenting them properly
- Training and qualifying your welders to ensure they can meet quality standards
Taking these steps today can save you from the catastrophic consequences of weld failures in the future. If you need guidance on where to begin, contact us for support in developing a comprehensive welding quality program.
References:
Weld Troubleshooting for Non-Welding Engineers
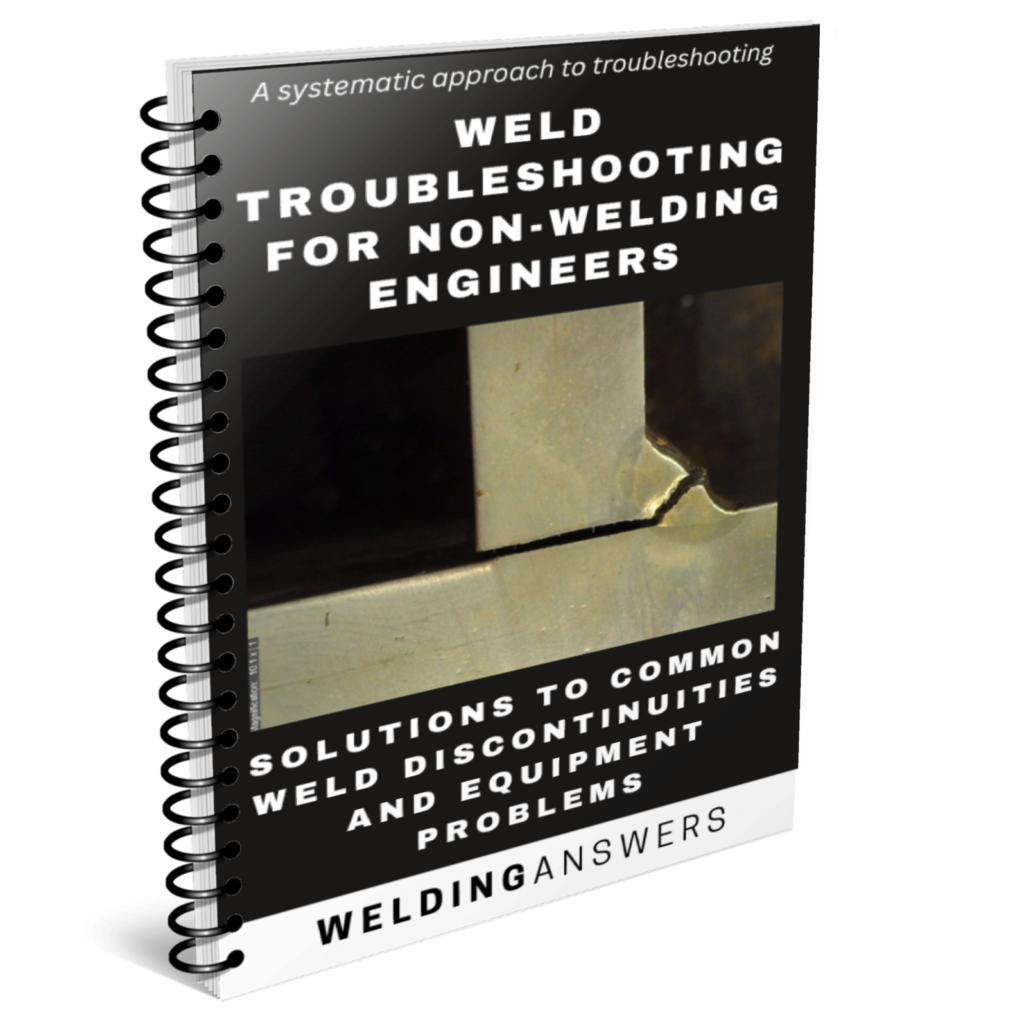
Please note: I reserve the right to delete comments that are offensive or off-topic.