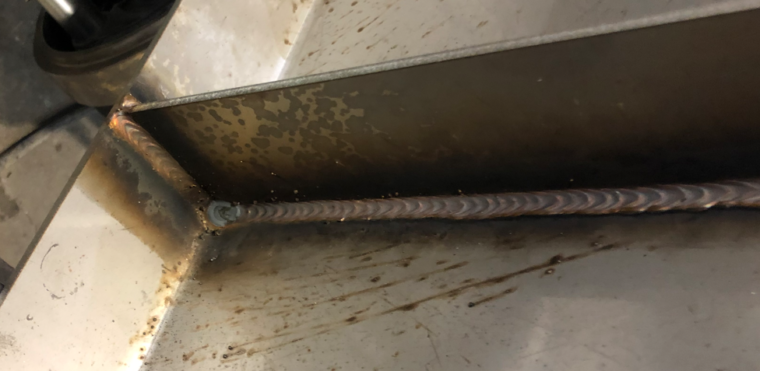
In our previous post, we introduced the basics of weldng austenitic stainless steels (304, 304L, 316, and 316L). Now, let’s dive deeper into the metallurgy of these alloys. Understanding their composition and grain structure is crucial for achieving sound, high-quality welds. This knowledge empowers welding professionals to make informed decisions about welding processes, filler metals, and techniques.
Key Alloying Elements and Their Roles
The properties of 300 series stainless steels are largely dictated by their alloying elements:
- Chromium (Cr): As mentioned before, chromium is the cornerstone of stainless steel’s corrosion resistance. It forms a passive oxide layer on the surface, protecting the underlying metal. In 304/316, chromium content typically ranges from 18% to 20%.
- Nickel (Ni): Nickel stabilizes the austenitic phase, enhancing toughness, ductility, and corrosion resistance. It’s particularly effective in resisting corrosion in reducing environments. Nickel content is generally 8% to 14% in these grades.
- Molybdenum (Mo): 316 and 316L contain 2% to 3% molybdenum. This addition significantly improves resistance to pitting and crevice corrosion, especially in chloride-rich environments.
- Carbon (C): Carbon content is a critical factor. 304 and 316 have higher carbon levels compared to 304L and 316L. Higher carbon can lead to carbide precipitation during welding, reducing corrosion resistance. Low-carbon versions minimize this risk.
- Other elements: Small amounts of elements like manganese (Mn), silicon (Si), and sulfur (S) are also present, influencing various properties like strength and machinability.
Welding engineers understand the role of these and other elements in stainless steels. Significant variations in any of these can cause welding related problems. In many failure analyses it is found that cracking and other defects occur due to the base metal being outside of the permissible ranges for these alloys. Carbon is one that you need to pay special attention to as it can reduce corrosion resistance, especially if paired with a high heat input welding procedure.
The Austenitic Grain Structure
The face-centered cubic (FCC) austenitic structure is what gives these steels their desirable properties.
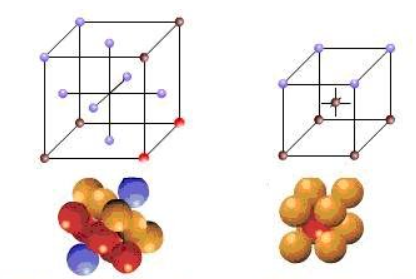
This FCC structure in austenitic stainless steels contributes to:
- Ductility and Toughness: The FCC lattice allows for significant plastic deformation without fracturing, making these steels tough and ductile.
- Weldability: The austenitic structure generally exhibits good weldability, but it also presents challenges that welders need to be aware of.
- Corrosion Resistance: The uniform distribution of alloying elements in the austenitic structure supports the formation of the protective chromium oxide layer.
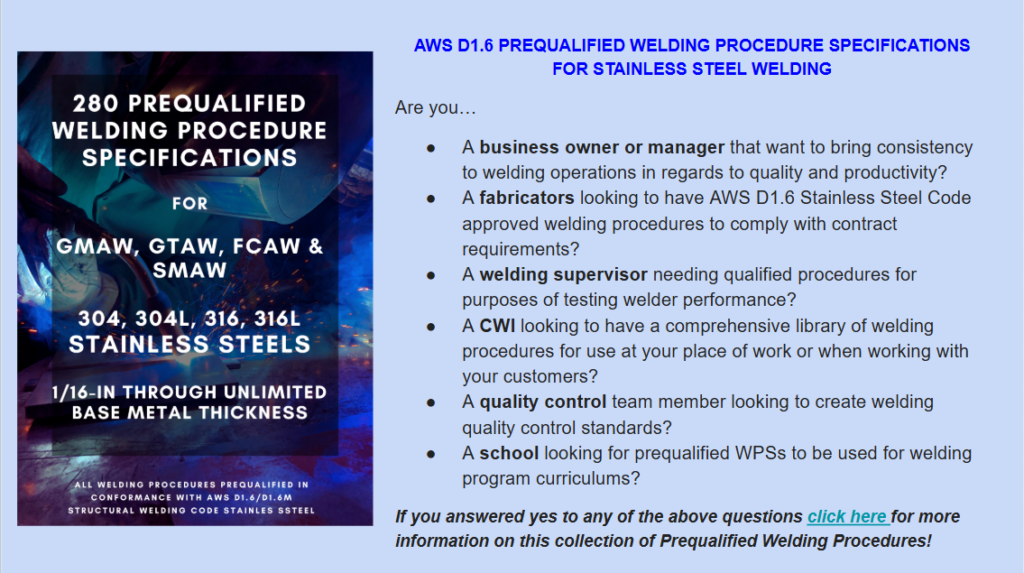
Impact of Metallurgy on Weldability
The metallurgical characteristics of 304 and 316 series stainless steels directly affect their weldability:
- Carbide Precipitation (Sensitization): As previously stated, when these steels are heated within a specific temperature range (800-1500°F or 427-816°C), chromium carbides can form at grain boundaries. This “sensitization” depletes chromium and reduces corrosion resistance. Low-carbon grades (304L and 316L) are designed to mitigate this.
- Heat Input: Controlling heat input is paramount. Excessive heat can exacerbate carbide precipitation and cause distortion. Conversely, insufficient heat can lead to lack of fusion and other defects.
- Solidification Mode: Austenitic stainless steels typically solidify in a primary austenitic mode. This can sometimes lead to microfissuring, especially in highly restrained welds. Careful control of welding parameters and filler metal selection is essential to minimize this risk.
- Residual Stress: Welding introduces residual stresses, which can affect the long-term performance of the weldment. Stress relieving may be necessary for critical applications.
- Distortion: The high coefficient of thermal expansion of stainless steel increases the chance of distortion. Proper clamping, fixturing, and welding sequences are crucial.
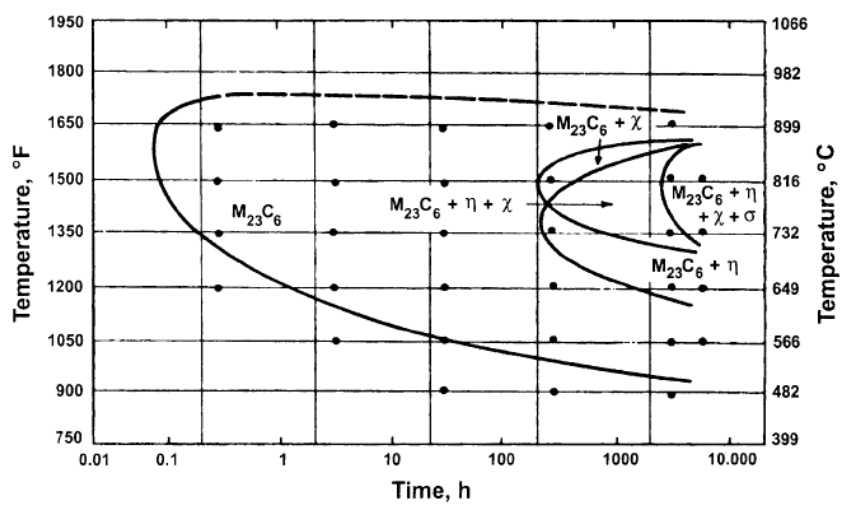
In general, austenitic stainless steels should be welded with low heat input (to facilitate rapid cooling and avoid sensitization and to reduce distortion). Special attention must be paid to weld size. Overwelding is wasteful but also a huge contributor to distortion. Keep welds as small as possible while still providing the design strength. Ensure the right filler metal is selected (more on this below). And be aware of potential residual stresses as these can significantly reduce the fatigue life of welded connections and structures.
Practical Implications for Welding Professionals
Understanding the metallurgy of these materials translates to better welding practices:
- Filler Metal Selection: Choose filler metals that match the base material to maintain corrosion resistance. For example, when welding 316, using a 316 or 316L filler is best practice. Sometimes the filler metal is not a direct match, so be sure to consult credible resources, such as AWS D1.6 Structural Welding Code (Stainless Steel) to ensure you are using the correct filler meta. For example, when welding 304 to 316 stainless steel the recommended filler metal is 308 (not 316).
- Heat Control: Minimize heat input by using appropriate welding parameters, smaller weld beads, and interpass rapid cooling (if allowed). This helps to reduce the risk of sensitization and distortion.
- Welding Techniques: GMAW welds can be a bit sluggish compared to welds made on carbon steel. The initial reaction to smooth the weld out may be to increase voltage. However, this is not always recommended as you can significantly increase the heat input. Performance is much more critical than looks. As long as weld passes the acceptance criteria of the code it does not matter if it is not the best looking weld.
- Cleaning and Passivation: Thorough cleaning between passes and post-weld passivation are essential to remove contaminants and restore corrosion resistance.
- Awareness of Sensitization: Be aware of the temperature range that can cause sensitization and avoid prolonged exposure within this range. Use low carbon grades whenever possible. Both with filler metals and base metals the “L” as in 316L or 304L denotes “low carbon”. The lower the amount of carbon the better.
In summary, the specific alloying elements of 304/316 series stainless steels, particularly chromium, nickel, and molybdenum, dictate their properties. The austenitic microstructure contributes to their ductility, toughness, and corrosion resistance. Welding can alter the metallurgy of these steels, leading to issues like carbide precipitation, distortion, sensitization and residual stress and this is why understanding these metallurgical factors is essential for welding professionals to make informed decisions and achieve high-quality welds.
Reference:
Are you constantly facing welding problems such as porosity, undercut, burn-through, lack of fusion, overlap, distortion or cracks? Struggling to troubleshoot bad welds or faulty welding equipment? If so Weld Troubleshooting for Non-Welding Engineers can help. This guide is provides a comprehensive list of welding discontinuities, their root causes and how to solve them. It also provides a list of the most common welding equipment problem and how to stop or avoid them.
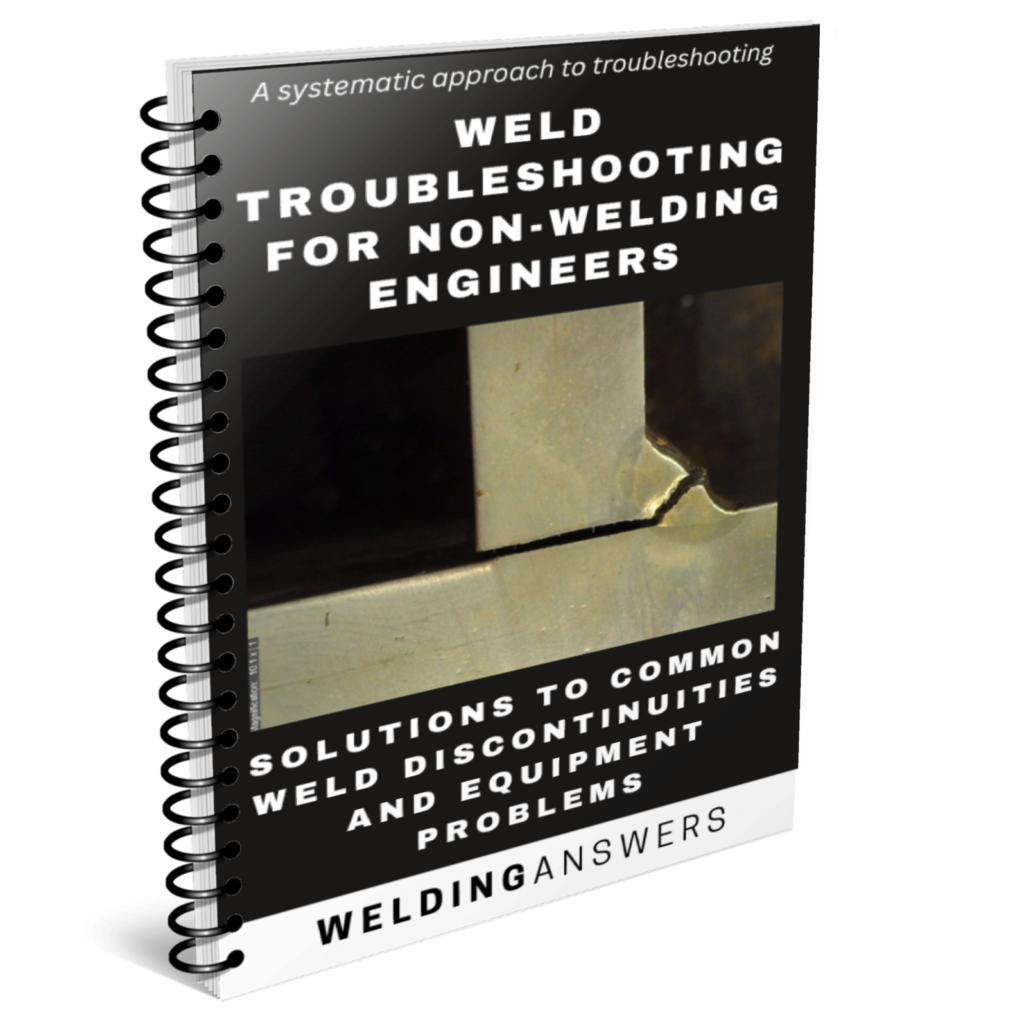