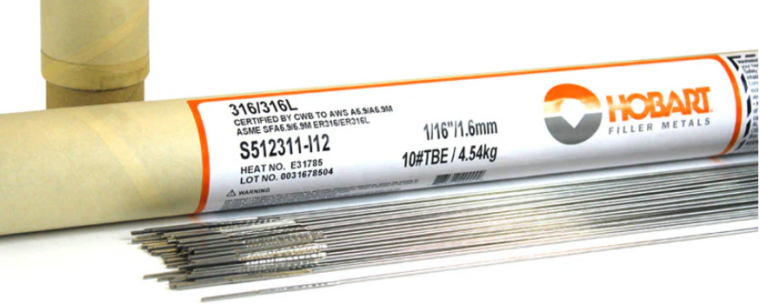
Welding engineers know how crucial the right filler metal is, especially when joining dissimilar metals. It’s not just about welding two pieces together and getting them to hold; it’s about creating a welded connection that can withstand the intended service conditions. In the case of stainless steel and other nickel alloys we also want corrosion resistance. It may require service at extremely high or low temperatures, and many more complexities. When welding dissimilar metals, choosing the right filler metal can be a bit complicated. There are fillers that are good for dissimilar metals, such as E309L, but it is not always the best choice. And in some cases may create problems. Choosing the wrong filler metal can lead to a host of problems, from cracking and weakness to premature failure.
Why is Filler Metal Selection So Important?
When we weld, we’re essentially creating a new material at the joint. This weld metal must be compatible with both base metals, not just in terms of ease of welding but also in terms of mechanical properties, corrosion resistance, and metallurgical compatibility. Dissimilar metal welding introduces added complexity because the two base metals have different chemical compositions and physical properties. In some cases these differences can be extreme.
The filler metal acts as the bridge between these two different materials. It must be carefully selected in order to:
- Ensure adequate strength: In general, we want the filler to match the strength of the base metal with the lower yield/tensile strength. Keep in mind that matching the strength of the stronger base metal may seem like a good idea, but it can actually be detrimental.
- Prevent cracking: Differences in thermal expansion and contraction rates between the base metals can cause cracking, especially if the filler metal doesn’t accommodate these differences. Certain filler metals will have additions of certain elements, such as titanium (Ti), columbium (Cb), aluminum (Al) and others that prevent cracking in certain base metals.
- Maintain corrosion resistance: The weld should be as corrosion-resistant as the base metals, particularly in harsh environments. Sometimes differences as subtle as using an E308 instead of a E308L can significantly impact the corrosion resistance of a welded structure.
The Dangers of Using the Wrong Filler Metal
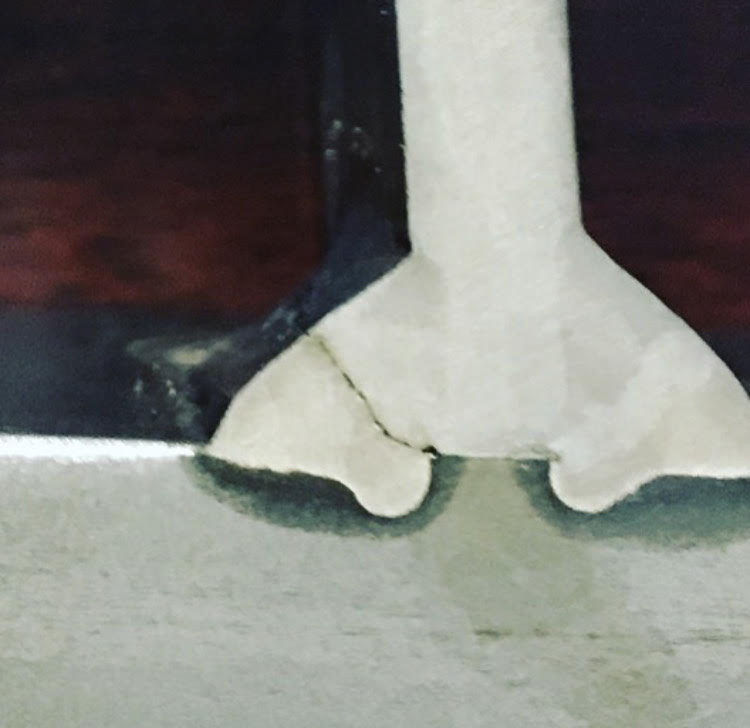
Using the wrong filler metal can lead to significant problems:
- Cracking: This is a common issue, often due to differences in thermal expansion or the formation of brittle phases. Cracks can weaken the joint and lead to failure.
- Reduced strength: The weld may not be able to withstand the intended loads, leading to failure under stress.
- Corrosion: The weld may corrode at a faster rate than the base metals, weakening the joint and potentially leading to leaks or failure.
- Brittle fractures: In some cases, the wrong filler metal can create a brittle weld that is prone to sudden fracture.
- Service failure: Ultimately, using the wrong filler metal can lead to the failure of the entire assembly, which can have serious consequences, especially in critical applications.
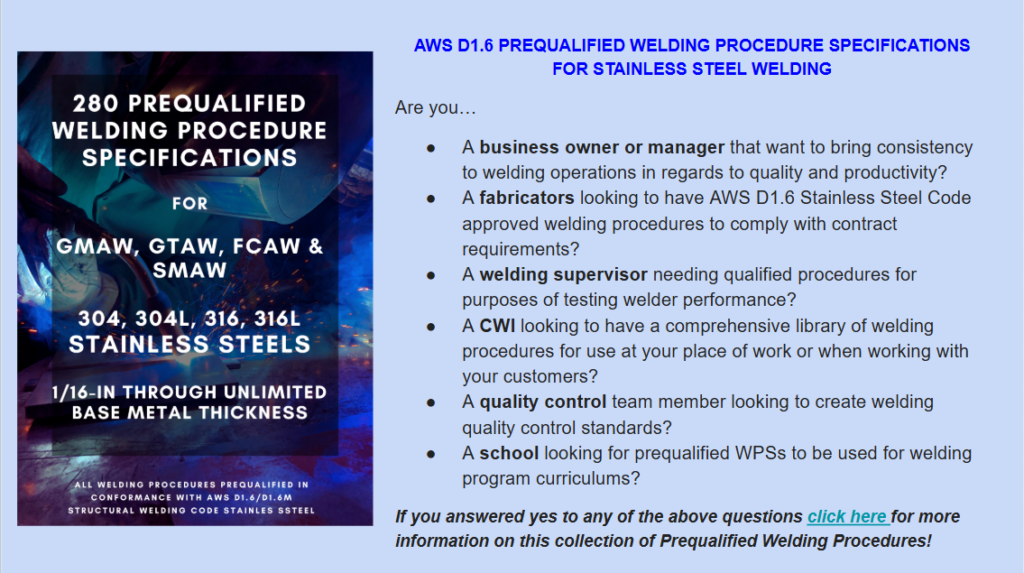
Examples of Dissimilar Metal Welding and Filler Metal Selection
Let’s look at a couple of examples to illustrate the importance of choosing the right filler metal:
1. Welding 304 Stainless Steel to ASTM A572 Grade 50 Steel
- Base Metals: 304 stainless steel (an austenitic stainless steel with excellent corrosion resistance) and ASTM A572 Grade 50 steel (low-alloy steel).
- Challenge: These materials have significantly different chemical compositions and mechanical properties. 304 stainless steel has a high chromium and nickel content, while A572 Grade 50 is primarily carbon steel.
- Recommended Filler Metal: ER309LSi. This filler metal has a higher alloy content (chromium and nickel) than 304 stainless steel, which helps to accommodate the dilution from the carbon steel. The “L” signifies low carbon, which helps to prevent carbide precipitation and maintain corrosion resistance. The “Si” indicates the presence of silicon, which improves weldability.
- Why this filler metal is correct: The ER309LSi filler metal provides a weld deposit that is compatible with both base metals. The higher alloy content compensates for the dilution from the carbon steel, preventing a loss of corrosion resistance in the weld. It also provides adequate strength and ductility to the joint coming for the addition of molybdenum. Using a filler metal designed for only carbon steel would result in a weld deposit that is susceptible to cracking and corrosion. Using a 308L filler metal would be close but because of the carbon steel would lead to carbon migration and corrosion issues in the fusion zone.
2. Welding Low to High Carbon Steel
- Base Metals: ASTM A572 Grade 50 (low alloy steel) to AISI 4140 (mid to high carbon steel with high strength).
- Challenge: AISI 4140 is highly susceptible to cracking and the welding procedures that may work for ASTM A572 Grade 50 may not be the best to use with AISI 4140. 4140’s high carbon content necessitates a preheat temperature that is much higher than anything ASTM A572 would ever need.
- Recommended Approach: ER80S-D2 would be the recommended filler metal if using the GMAW. Note that this is an overmatch for the ASTM A572 but a severe undermatch for the 4140. The reason why we want this is to have a weld that is ductile and prevents cracking. If more strength is needed out of the weld then the weld is made bigger. The only time this is not possible is if the weld is already a complete joint penetration weld. In this case going to a 90 ksi filler metal may be the best option.
- Why this approach is correct: It is important to note that matching the strength of the strongest base metal is almost never a good option. Many failures occur because the thought process dictates that a stronger filler metal provides a stronger weld. This may be true, the tensile strength and hardness of the weld will be high, but we don’t always want that. Many times we prefer ductility of hardness or strength.
In summary, filler metal selection is critical in all welding applications, but it’s especially important when welding dissimilar metals. The wrong filler metal can lead to cracking, reduced strength, corrosion, and ultimately, failure of the welded joint. Always consult with a welding engineer or refer to welding codes and standards (such as AWS D1.6 Structural Welding Code (Stainless Steel)) when selecting filler metals for dissimilar base metal welding. And finally, consider the chemical composition, mechanical properties, and service conditions of both base metals when making your selection as there may be more than one option.
By understanding the importance of proper filler metal selection, you can ensure the integrity and adequate service performance of your welded joints, especially when working with dissimilar metals.
References:
Welding Procedure Development for Non-Welding Engineers
Welding Metallurgy and Weldability by John C. Lippold