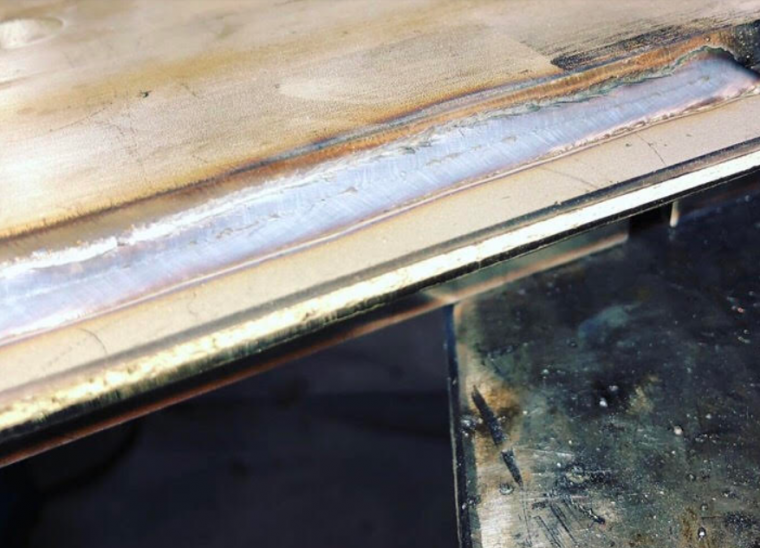
Many ‘experts’ in the welding industry talk about high heat input as something that should always be avoided. Unfortunately, this is not good advice. High heat input can be detrimental in many cases, but other times we want to have higher heat input.
Heat input is directly related to amperage and voltage and inversely related to our travel speed. For a detailed explanation read on how to determine heat input read How to Calculate Heat Input.
A few instances were high heat input in undesirable are:
- Welding austenitic stainless steels – the higher the heat input the slower the cooling rate which in turn increases the amount of time in the sensitization range.
- Welding materials highly susceptible to distortion – the higher the heat input the more a metal can distort. This is especially true for stainless steel as it has a very low thermal diffusivity and high thermal expansion.
- Annealing of hardened carbon steels – the higher the heat input the lower the cooling rate, which will increase the amount of time certain areas of the heat affected zone (HAZ) are in a temperature range that can experience microstructural changes. Hardened material may be annealed.
- Welding of thinner section – this is an obvious one but worth mentioning. High heat input is not good on thin materials as it can create burn trough.
Now, here are a few instances when you do want high heat input:
- Welding medium to high carbon steels – these steels are susceptible to cracking due to embrittlement of the weld and HAZ. This is due to the formation of martensite experience when the weld and HAZ experience rapid cooling. High heat input has a similar effect to preheating; it slows down the cooling rate. This is the reason why the structural welding code for steel (AWS D1.1) has minimum fillet weld sizes. For further details on this read The Reason behind Minimum Fillet Weld Sizes.
- Welding thick sections – the higher heat input will help with penetration provided the travel speed is adequate for the deposition rate of the welding procedure.
- Getting rid of porosity – porosity can sometimes be caused by the rapid solidification of the weld puddle. Gases may be trapped and internal porosity may result. If we weld with high heat input we would create a larger puddle and one that does not solidify as quick, thus allowing any gases in the weld to exit prior to solidification.
The determination of whether the heat input should be controlled, either with a maximum or a minimum, starts with the base metal being welded. We then have to consider the mechanical properties that we need out of the weld and how heat input can affect these properties. As mentioned above, rapid cooling due to low heat input may be desirable when welding austenitic stainless steels but undesirable when welding medium carbon steels. If you are not sure consult with a knowledgeable industry professional.
Thank you for the informative summary. I have two questions on heat input.
1. Is there any basis or general practice about heat input “value” according to base material and welding process?
2. For hardened carbon steel, I agree with the point mentioned. However, when I think about cooling rate, it seems that hardned carbon steel is also susceptible to cracking due to embrittlement of the weld and HAZ. Could you advise the effect of higher cooling rate on hardned material?
Hello Kim.
1. The base material can dictate maximum or even minimum heat input. It depends highly on the welding application as well. But a quick example for materials: Steel such as 4140 needs to be preheated to slow the cooling rate. However, it is possible to weld it with extremely high heat input from the welding process (maybe using SAW) and be able to achieve welds without cracks. The higher the heat input, the more the plate gets heated, the slower the cooling rate. I’m not suggesting you forgo preheat, but structural steels in general do well with high heat input and not so good with low heat input. AWS D1.1 Structural Welding Codes (Steel) dictates minimum fillet weld sizes. This is done not for strength, but to achieve a minimum heat input in order to prevent rapid cooling. Read The Reason Behind Minimum Fillet Weld Sizes for further explanation.
2. When you weld on hardened material you are still susceptible to cracking. As a matter of fact, welding on quenched and tempered steels is not always advisable due to this reason. When you weld a hardened material you will end up annealing it in the HAZ, so you’ll end up with properties significantly different than what you started with. The cooling rate still controls the amount of martensite that will form. So you will have a material that has significantly different hardness levels in the weld metal, heat affected zone and unaffected base metal. This is can be very dangerous.