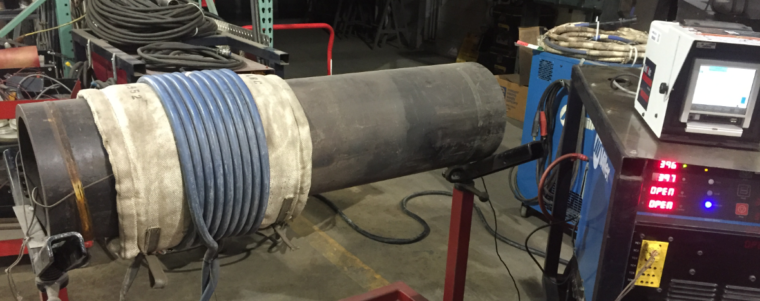
Preheat is necessary in certain carbon and low alloy steel applications to prevent hydrogen induced cracking, also known as cold cracking. Cold cracking susceptibility increases as the amount of carbon in steel and the thickness go up. The higher the carbon content the easier it is for the steel to harden. And, the thicker the material the faster the cooling rate (bigger heat sink) which may facilitate the formation of martensite. Martensite is a very hard microstructure which is highly susceptible to brittle fracture.
So how do we know if preheat is necessary? The easiest way is to find the steel you are welding in AWS D1.1 Structural Welding Code – Steel, which will tell you when preheat is necessary and will give you minimum values for it. However, if you are not welding a structural steel covered by AWS D1.1 what can you do?
As a rule of thumb, we can say that any time the carbon content of steel is 0.30% or more we must preheat. This is a conservative approach, but when we are manufacturing steel structures being conservative is not such a bad thing. As stated above, as the carbon content increases so does hardenability.
There are other elements that also contribute to hardenability and must be taken into account when determining if preheat may be necessary. These other elements include manganese, silicon, chromium, molybdenum, vanadium, copper and nickel. Some affect hardenability more than others and thus receive appropriate weights in the calculation of the carbon equivalent.
The carbon equivalent (CE) is used to understand how the alloys mentioned above affect the hardness of the steel being welded. There are many different CE formulas, but the two most commonly used are those accepted by the American Welding Society and the International Institute of Welding.
The formulas are as follows:
The only difference between the two is that the AWS formula includes silicon. These formulas are meant to provide a value for weldability. Weldability does not simply refer to whether or not a metal can be joined by welding. This term, unfortunately, is interpreted to mean many different things. However, the weldability of a base metal describes both the ability to successfully fabricate a component using welding and the capacity for that component to perform adequately in its intended service environment.
The lower the value of the CE calculation the higher the weldability. Because the problem with high values of CE is increased hardenability, preheat is used to successfully weld those materials that have high values. The chart below provides ranges for CE and its effect on weldability. It also provides recommendations of when to consider preheating.
WARNING: The CE method does not take into account the thickness of the base material. Any time the thickness exceeds ½ in [13 mm] you should consider the use of preheat.
Determining if preheat is necessary is half the battle. You must then figure out what preheat and interpass temperature must be used. For information on different methods to determine preheat and interpass values read 5 Methods to Determine Preheat Temperature.
There are other CE formulas that provide more specificity to certain applications. There is one that was specifically developed for spot welding of high strength steels. This formula also considers the thickness of the base material along with the ultimate tensile strength.
Understanding weldability, susceptibility for cracking, need for preheat and other important aspects related to the base metals we will weld is very important. This allows us to develop a welding procedure that has a high probability of success. It is always important to prove that our welding procedure is adequate by properly qualifying it using acceptable methods such as those provided by welding codes.
References:
Qualification of Welding Procedures, Welders and Welding Operators
Welding Metallurgy and Weldability by John C. Lippold
Does your operation need welding procedures? Are you looking for consistency in quality and productivity in your welding operations? Don’t forget that we offer an extensive library of ready-to-use prequalified carbon steel welding procedures specifications in conformance with AWS D1.1 Structural Welding Code – Steel.
____________________________________________________________________
Are you looking to qualify welding procedures and/or welders? Are you using AWS D1.1 Structural Welding Code -Steel as your quality standard?
“Qualifying Welding Procedures, Welders and Welding Operators” is a guide developed to help you peform your own qualifications in full compliance to AWS D1.1 Structural Welding Code. It provides step-by-step instructions on how to qualify welders and welding procedures. It also provide step-by-step instruction on the proper use of prequealified welding procedures.
An area of welding information or the lack of information, is the welding of tool steels and cast iron used in molds in the tool and die industry.
Steels such as A2 and D2 along with the cast irons are difficult to repair with high drgrees of success.
It would be nice to see accurate information from the pros as to types of filler materials required, shielding gasses, processes used, such as GTAW and GMAW, tungstens and weld parameters.
Postheat and preheat techniques for those repair shops that dont have the funds for elaborate ovens,etc. Of course examples and methids of grinding the repair area should be included .
Thanks for the comment. This certainly would make a great topic for a few articles. You are correct in that there isn’t much accurate information available for these types of repair. If you are able you can email us a specific application and we can write the article based on that.