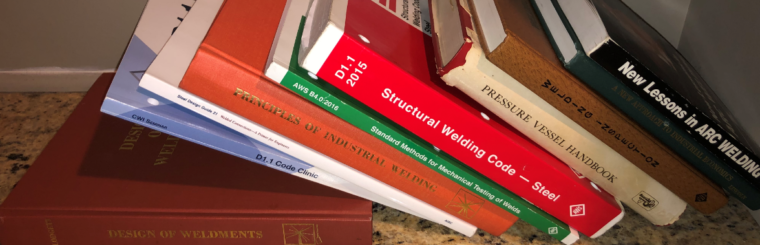
Today we are faced with a tremendous shortage of welding professionals. This includes welders, fitters, cutters, inspectors, supervisors, robotic technicians and welding engineers to name a few. Although every fabricator can benefit from having a welding engineer on staff, most welding engineers tend to work in specific industries such as Oil & Gas, Aerospace, Automotive and other high profile industries. This is due to the complexity of the materials used in production in these industries, to the potential danger to users of the products being built if flaws are present, and to multitude of changes in product design. Welding engineers are in very short supply and extremely high demand.
For most general fabrication shops having a welding engineer on staff is not affordable. If they focus on welding carbon steels and only once in a while dabble with stainless, aluminum or other exotic alloys they can get by with hiring outside assistance on an as-needed basis. However, there are several welding engineering topics and areas of interest that do not require a welding degree to learn, understand and apply to the job.
Regardless of the background of the person that is in charge of welding operations, the following topics must be learned. Not surprisingly these are not always taught in school in a way that makes them easy to apply, even at schools that have welding engineering programs.
- Metallurgy – some materials can be weld with any process and with wide open welding procedures without any issues. Other materials are very sensitive to heat input, filler metal selection, shielding gas selection, weld sequence and many other welding related variables. Having knowledge of basic metallurgy, and more specifically welding metallurgy, can prevent a lot of problems and help with decisions when developing welding procedures.
- Welding Economics – welding has a significant impact on the cost of fabricated products. Most of the cost comes from labor. A poorly written welding procedure may cost a company a lot of money EVEN if it provides acceptable quality. Understanding how welding procedures affect costs, quality and productivity is extremely important. In a recent project we discovered that a customer had welders that ran significantly different welding procedures (filler metal diameter and wire feed speed). Taking into account labor, efficiency and material costs there was a range from $1.17 to $4.56 per foot of weld. That means that the most efficient welder was producing the same amount of weld as the least efficient at fraction of the cost. The other 12 were somewhere in between. Yet these welders are being paid the same. They all have comparable skills. They all are extremely hard workers. The difference was the welding procedure they chose to use. A lack of understanding of how this impacts costs is what never prompted this fabricator to consider keeping a tighter control on welding procedures.
- Effects of Welding Variables – understanding the effects of welding variables (the variables in a welding procedure) we can more easily diagnose problems, troubleshoot welds and lower operation costs. It is extremely important to understand how the many different welding variables can affect the quality of our welds, and as stated above, the cost.
In just a couple of weeks we will be releasing Developing Welding Procedures for Non-Welding Engineers. This is something that we work on with our customers almost on a daily basis and we are now making it available to our readers based on multiple requests.
- Weld inspection – visual inspection is the most cost effective method of weld inspection. Welders and quality inspectors alike must be able to recognize welding discontinuities and understand their severity. Welding inspection is a viable means of inspection if we have qualified welding procedures in place. In the absence of welding procedures a good looking weld (external appearance) is not sufficient to assure quality.
Welders are the first and most important line of defense when it comes to inspection. They can perform inspection before, during and after welding. Inspection while they are welding is critical. They can see problems such as lack of fusion, internal porosity, lack of penetration and other problems that cannot be detected by visual inspection once the weld is completed.
- Testing methods – welding procedures and welded connection must be tested to ensure they will perform adequately in service. Following testing procedures from structural welding codes and those from quality standards and other specifications is critical. It is also important to be able to select the right testing methods and understand when testing to codes does not provide enough specificity.
- Code application – welding engineers and those in charge of welding must be able to adhere to codes and standards when dictated by contract documents. Certified welding inspectors (CWIs) are experts in this area. However, familiarity with codes that must be followed is essential to those managing welding operations.
- Failure analysis – being able to determine the root cause of a failure is one of the most important responsibilities of welding engineers. It is crucial to understand what caused a problem in order to prevent it from happening again. This was explained in detail in last week’s post Why Welds Fail.
- Ethics – Shortcuts have no place with a welding engineer or whoever is in charge of welding. Whenever changes that deviate from an established process are needed they need to be approved after careful analysis. Welding engineers and CWIs are often faced with having to make tough decisions. At times, these professionals have a lot of pressure from their own companies to approve products that did not meet the quality standard in order to avoid significant losses. This is unfortunate and it happens a lot.
Welders, welding supervisors and leaders, CWIs and other welding professionals make decisions, knowingly or unknowingly, whose impact is affected by the level of knowledge of the topics above. Therefore, it is critical that we encourage our welding staff to participate in continuous learning.
As welding consultants we spend a lot of our time developing welding procedures, developing quality standards, auditing for code compliance and conducting failure analyses. It is very rewarding to see that with proper instruction and full commitment from our customers we can teach them how to perform these tasks on their own. Or at least, some of them. This is part of what we do through our weekly articles and by answering questions you send us via email.
Any additional knowledge gained in these topics, whether through a class, a book or onsite training can yield significant benefits to any welding operation.
So if you hold a welding engineering position, whether you have a formal education or not, you must always continue to learn. Seek out help from those that have gone before you and proven to be some of the best in their field. Look up information from reputable sources. The American Welding Society has an endless number of valuable resources on all of the above topics. Many of the major manufacturers of welding equipment and consumables do as well. There is no excuse to not continue to learn. Good luck to all.
I really liked this post because I am also a person with no formal training. I still learn from day to day. Thank you very much.