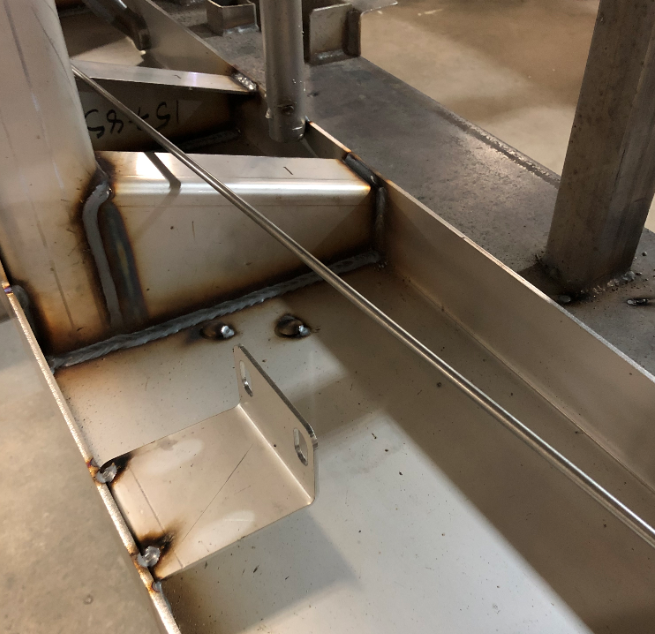
The following information is for welding austenitic stainless steels to carbon steel. Austenitic stainless steels are very common in structural applications and include 304, 304L, 309, 309L, 316, 316L and 347. There are other considerations when welding ferritic, martensitic, precipitation hardening and duplex stainless steels to carbon steel which are beyond the scope of this article.
The primary concern in welding austenitic stainless steel to carbon steel is avoiding solidification cracking. For this reason, the selection of the filler metal is of utmost importance. For welding stainless steel to carbon steel the filler metal you should use in the vast majority of applications is 309. The reason for using 309 is that it provides a solidification condition in which ferrite is the first phase to freeze.
In order to have this condition the weld deposit should have a ferrite number (FN) of at least 3. Some publications say it should be at least 5, but we’ll stick to the recommendations offered in AWS D1.6 Structural Welding Code – Stainless Steel. The ferrite number can be estimated by using WRC-1992 Diagram (see image below). A common mistake in welding stainless to carbon steel is using 308 filler metal. Unfortunately this is very common as the thought process is that the main concern is corrosion, so with 308 being much more resistant to corrosion than carbon steel it should be OK to use. This, as you can probably guess, can lead to solidification cracking due to a lower than desired ferrite content.
So, when welding stainless steel to carbon steel the filler metal to be used should be 309. This can also be 309L (lower carbon) or 309LSi (addition of silicon). This filler metal is specially formulated for welding dissimilar metals. It contains ferrite stabilizers which counter the weld deposit’s tendency to form austenite after picking up carbon from the carbon steel base metal. This is what prevents hot cracking.
At times, the required weld deposit when welding dissimilar steels cannot have any ferrite. In this case you must be careful in order to avoid cracking. One way to do this is to produce a weld bead that is convex (ropey). Other recommendations may include the use of higher nickel alloy filler metals such as AER320LR or ERNiCrMo-3.
There is a possibility of getting a ferrite number of less than 3 even when using 309 filler metal. This happens if there is a lot of dilution of the carbon steel into the weld deposit. Welding processes such as submerged arc welding are susceptible to this due to them being high penetration processes. Proper welding parameter selection and joint design are important considerations in this case.
References:
AWS D1.6/D1.6M:2017 Structural Welding Code – Stainless Steel
Metals and How to Weld Them