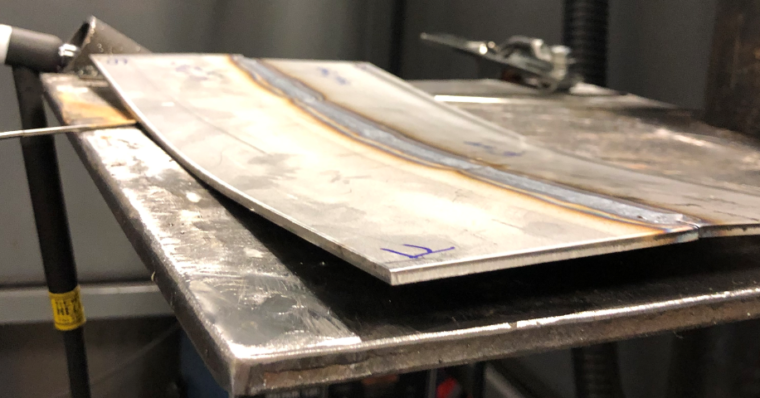
Austenitic stainless steels, renowned for their corrosion resistance and aesthetic appeal, are a staple in numerous industries. However, welding these materials often presents a significant challenge: distortion and warpage. This isn’t just a cosmetic issue; it can lead to dimensional inaccuracies, compromised functionality, and costly rework. So, why are austenitic stainless steels so prone to distortion? Let’s delve into the underlying physical and mechanical properties that contribute to this phenomenon.
Physical and Mechanical Properties that affect distortion
The primary drivers of distortion in welded austenitic stainless steels are rooted in their inherent material characteristics:
- High Coefficient of Thermal Expansion:
- Austenitic stainless steels possess a significantly higher coefficient of thermal expansion compared to carbon steels. This means they expand and contract more substantially with temperature changes.
- During welding, the intense heat causes localized expansion. As the weld cools, the contraction is also substantial, leading to residual stresses and deformation.
- This amplified expansion and contraction cycle exacerbates distortion, as the material struggles to return to its original shape.
- Low Thermal Conductivity:
- Austenitic stainless steels exhibit lower thermal conductivity than carbon steels. This means heat doesn’t dissipate as quickly, resulting in concentrated heat zones around the weld.
- The localized heat intensifies the temperature gradients, creating uneven expansion and contraction. This unevenness is a major contributor to warpage.
- The heat stays in a smaller area for a longer period of time.
- Lower Yield Strength at Elevated Temperatures:
- The yield strength of austenitic stainless steels decreases significantly at elevated temperatures. This means the material becomes more susceptible to plastic deformation under the stresses induced by welding.
- The high temperatures in the weld zone reduce the material’s resistance to deformation, allowing the contraction forces to permanently alter the shape of the component.
- Austenitic Microstructure:
- The austenitic microstructure itself, while providing excellent corrosion resistance, contributes to distortion.
- The phase transformations that can occur in other metals during welding are less prevalent in austenitics, meaning the stresses are more likely to result in plastic deformation.
The Chain Reaction that lead to distortion
Here’s how these properties interact to create distortion:
- Localized Heating: The welding arc introduces intense heat into a small area.
- Rapid Expansion: The high coefficient of thermal expansion causes the heated area to expand quickly.
- Restricted Expansion: The surrounding cooler material restricts this expansion, creating compressive stresses.
- Yielding: The reduced yield strength at elevated temperatures allows the material to yield under these compressive stresses.
- Contraction and Residual Stress: As the weld cools, the material contracts. The restricted contraction creates tensile residual stresses.
- Distortion: The combination of residual stresses and plastic deformation results in distortion and warpage.
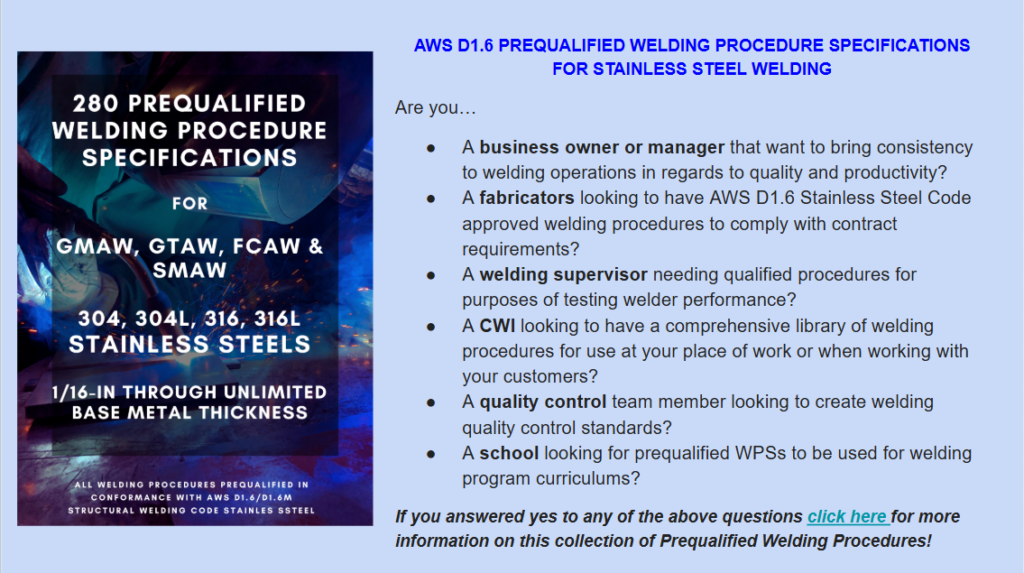
How to minimize distortion in stainless steels
While eliminating distortion entirely is often impossible, several techniques can minimize its impact:
- Heat Input Control: Use lower heat input welding processes (e.g., pulsed GTAW, GMAW), reduce weld sizes, increase travel speed and minimize the number of weld passes.
- Welding Sequence: Employ backstepping, skip welding, or balanced welding techniques to distribute heat evenly.
- Fixturing and Restraint: Use rigid fixtures to restrain the workpiece during welding and cooling. This does not completely elminate distortion, but can reduce it. When clamps and fixturing are removed the parts will still distort to some extent.
- Preheating and Interpass Temperature Control: While less common with austenitics than carbon steel, controlled preheating can help to reduce thermal gradients. Interpass temperature control is very important.
- Post-Weld Heat Treatment (PWHT): In certain applications, PWHT can relieve residual stresses and reduce distortion.
- Proper Joint Design: Design joints to minimize weld volume and stress concentrations.
- Symmetrical Welding: Weld on both sides of a joint, if possible, to balance the stresses.
- Peening: In some applications, peening can be used to induce compressive stresses that counteract tensile residual stresses. Keep in mind that seveal codes do not allowed peening in prequalified procedures. This may need to be approved by the engineer in charge or qualified by testing.
In summary, understanding the physical and mechanical properties of austenitic stainless steels is crucial for mitigating distortion during welding. By implementing appropriate welding techniques and control measures, welding professionals can minimize warpage and ensure the integrity and functionality of their welded components. It is very important to remember that every welding project is unique and requires a tailored approach.
Welding Procedures for Stainless Steel
Need AWS D1.6 Prequalified Welding Procedures for welding 304, 304L, 316 and 316L. This collection of 280 Prequalified WPSs for Austentic Stainless Steel covers the 14 most common joints used in production for GMAW, GTAW, FCAW and SMAW. Also, instruction on how to revise these prequalified procedures to accomodate many other weld joints, other stainless steel grades and different filler metals.
