High strength steels are becoming more and more popular in steel construction. Higher strength means we can reduce the thickness of the base material and thus reduce weight. This is very important not just in vehicles but in static structures as well. However, higher strength steels usually bring about a few issues that if not understood can create more harm than good.
One of these issues is the assumption that we must always use a matching filler metal. This means that if we are welding T-1 steel (Arcelor Mittal’s trade name for ASTM A514) which has a yield strength of 100ksi and tensile strength ranging from 110 to 130ksi we would at the very least use a filler metal with 100Ksi minimum tensile strength. If we are using the SMAW process we would chose an E10018. If we are using GMAW we would go with an ER100S-G. And if we prefer SAW we would use a wire flux combination such as F11A6-ECM2-M2-H8 to provide matching strength.
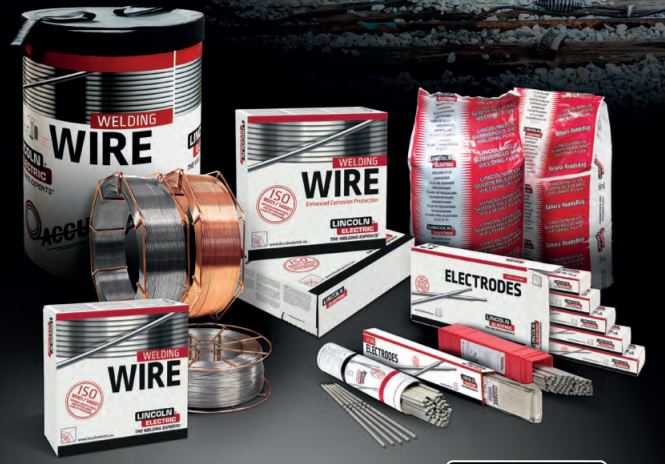
Filler metal selection does not always need to be based on the tensile strength of the base material.
When we receive calls from our customers asking for filler metal recommendations to weld steels such as T-1 we are typically asked for a matching filler metal. We respond with the following question:
Do you need to match the strength of the base metal?”
Why do we ask this? We do because undermatching may be beneficial. Undermatching simply means to use a filler metal whose specified tensile strength is less than the specified tensile strength of the base metal.
Unless you are required to make a complete joint penetration (CJP) weld, you don’t necessarily need to match the filler metal to the strength of the base metal. So if you are making partial joint penetration (PJP) welds or a fillet welds you should be able to use an undermatching filler metals.
Why undermatch? If nothing else, undermatch for one simple reason: It reduces the risk of cracking because it reduces the concentration of stresses in the base metal. The lower strength base metal will be more ductile than a matching filler metal and thus would reduce the magnitude of the residual stresses.
Keep this in mind; a weld only has to be strong enough to transfer the loads that are passed between the two members which are welded. We can increase the strength of the weld by increasing any of the three variables below.
- Weld length
- Weld effective throat
- Weld metal strength
In the case of fillet PJPs and fillet welds, we may not be able to increase the length of the weld if the joint is already fully welded, but we can certainly increase the effective throat. This can be achieved in one of two ways:
- For both PJPs and fillet welds we can get deeper penetration – we can accomplish this through better welding procedures or by modifying our joint preparation. This will produce a larger effective throat. For more information on why this is you can read The Importance of Root Fusion and Fillet Weld Leg Sizes Are Meaningless.
- For fillet welds we can make the weld bigger (i.e. going from a ¼” fillet to a 5/16” fillet). If our root penetration remains the same the bigger weld will have a larger effective throat.
The advantage of going with option one above is that by not adding more filler metal, we do not run the risk or increasing our susceptibility for distortion. The second option creates a bigger weld which may increase our heat input and create or increase the magnitude of distortion.
So before you choose a matching filler metal for your high strength steel ask yourself this question: Do I really need to match the strength of the base metal? This may be a design question you are not qualified or don’t have enough information to answer. But seek counsel. You may be much better off.
As stated above, the use of undermatching filler metals will reduce the risk of cracking because it reduces the concentration of stresses in the base metal. The undermatching filler metal will have lower tensile strength, but higher ductility than the matching filler metal. We want our weld to be able to have some give, especially on highly restrained joints.
Reference: Welding Innovation Journal Vol. XIV, No. 1, 1997
Are you tasked with developing, qualifying and approving welding procedures? Are you in need for procedures that adhere to AWS D1.1 Structural Welding Code – Steel? If so, the use of prequalified Welding Procedure Specifications will help you save time and money. It will also help with quality and consistency. Qualification testing for a single welding procedure can cost over $1,000 depending on the necessary tests. Prequalified WPSs are exempt from testing and ready to use.