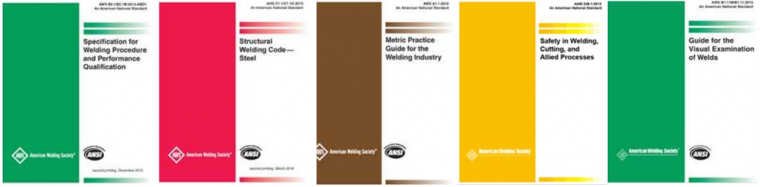
If you have taken or hope to take the CWI exam you probably have searched for some practice exam questions. In practicing for the code book portion of the test you may have come across a few questions for which you could find the answer, but didn’t really understand the importance of the question or the reasoning behind the answer. These are fundamental questions. Ones we constantly have to explain to our customers as part of sound fabrication instruction.
So without further ado here they are:
- Welding shall not be done when the ambient temperature is…
Answer: Below 0˚F [-20˚C]
Explanation: The question many have after knowing there is a temperature below which welding shall not be done is why you can’t just preheat the base metal. And the answer to that is that AWS must impose certain guidelines and limits to prevent fabricators from entering dangerous situations. When the ambient temperature is that cold even a preheated part can cool too quickly. So if under normal conditions the code calls for a preheat temperature of 225˚F you are not allowed to preheat to this temperature when the ambient temperature is below 0˚F. Even if you do, and you weld immediately, the weld and heat affected zone (HAZ) can still cool too quickly causing embrittlement and increasing cracking susceptibility.
Additionally, please note that 0°F [-20˚C] does not mean the ambient environmental temperature, but the temperature in the immediate vicinity of the weld. So if you are able to have some sort of shelter over the area were the weld is to take place and you can keep that temperature inside at or above 0˚F you can follow standard preheat guidelines and weld.
This answer can be found in Clause 7 section 7.11.2 of AWS D1.1/D1.1M:2020.
2. What is the minimum fillet weld size for joining two half-inch [12mm] thick members with a low-hydrogen process?
Answer: 3/16 in [5mm]
Explanation: The question here is why are there minimums? Most fillet welds in real world application are not transferring full loads, rather they are there to add rigidity. When FEA software is used and a weld size is calculated it must always be checked against Table 5.7 of AWS D1.1. The reason for the minimum is not because a minimum amount of strength is required from the welds. It is because the smaller the weld the lower the heat input. It is possible to create localize hardening of the HAZ even on materials that are considered low carbon such as ASTM A36 or ASTM A572 Gr 50. If the weld is too small the heat input will be very low and cooling rate extremely high. Therefore, limits on the weld size are imposed.
This answer and subsequent explanation can be found in Table 7.7 and in the commentary section C-7.13 of AWS D1.1/D1.1M:2020.
3. What is the maximum fillet weld size allowed for prequalified welding procedures for a single pass done with the GMAW process?
Answer: 3/8 in [10mm]
Explanation: The reason behind maximum sizes for fillet weld is to ensure quality. If you try to make a 1/2in [12mm] fillet weld with spray transfer (short circuit is not permitted for prequalified welding procedures) chances are you will have a nasty case of overlap. This is true even of a 3/8in [10mm] fillet weld in the horizontal position. Overlap is when gravity forces the puddle to sag against the horizontal member being joined as can be seen below.
Overlap is a very dangerous discontinuity that must be repaired. As you can see in the image above it creates a mechanical notch with a relatively sharp tip. This is a stress concentrator that can easily initiate a crack. This problem is extremely dangerous in cyclically loaded applications.
The answer to this questions is found in Table 5.1 – Prequalified WPS Requirements of AWS D1.1/D1.1M:2015. Section 7.23 further explains that no amount of overlap is permitted.
4. What is the required preheat temperature for welding 1in [25mm] thick ASTM A572 Grade 50 steel?
Answer: 50˚F [10˚C]
Explanation: Preheat temperature aren’t usually questioned, but what some fabricators want to know is why they need to do it. In short, it is done in order to slow down the cooling rate after welding. If the cooling rate is too high we risk embrittlement of the HAZ due to the formation of martensite. When we preheat we slow down the cooling rate.
This answer is found on Table 5.8 of AWS D1.1/D1.1M:2020. For more on why we need preheat you can read: Why Is Preheating Necessary.
5. Which of the following welding processes cannot be used with Prequalified WPSs: SMAW, FCAW, GMAW-S, GMAW, SAW.
Answer: GMAW-S
Explanation: GMAW-S stands for Gas Metal Arc Welding – Short Circuit Transfer. More commonly referred to as short arc. In order to use prequalified welding procedures you must abide by a set of rules and limitations. These rules and limitations are there to ensure sound welds. Prequalified welding procedures allow you to forgo testing of your WPS. If too much freedom is given we would run into a situation where prequalified welding procedures are producing welds of poor quality.
Short arc is a relatively cold process which is great on thin materials but is extremely susceptible to lack of fusion (cold lap) on thicker members. AWS D1.1 covers structural steels having a minimum thickness of 1/8in [3mm]. Short arc is not really recommended for thickness over 1/8in, so to be safe it is completely prohibited in the use of prequalified welding procedures. The image below was collected as part of a welding survey. This was on 1/8 in [3mm] thick ASTM A36. As the red line indicates there is no root fusion. As a matter of fact, the welder wasn’t even close to fusing to the root.
However, you can certainly qualify a welding procedure on thick sections with short arc. Clause 6 of AWS D1.1/D1.1M:2020 allows you to do this. But you have to qualify the procedure by testing. If you try this you’ll find that it is extremely difficult to achieve root fusion and in some cases side wall fusion with short arc on materials thicker than 3/16in [5mm].
In the CWI exam you are never asked to explain anything. All questions are multiple choice. However, it is important to understand why the code has so many requirements. They are all geared towards ensuring the safety of those using and those in the proximity of welded structures. Fabricators must understand these principles in order to produce sound welds.
Our next article will cover 5 more fundamental principles and CWI exam questions along with detailed explanations. These questions will be in the areas of bead contour, lap weld size requirements, cracks, qualification when charpy v-notch (Charpy v-notch) testing is required, and welding symbols.
References:
Qualification of Welding Procedures, Welders and Welding Operators
Thank you for all this information, it really feed my knowledge needed about welding processes, I’m a welding instructor and this information help me a lot.
Great to hear Milton! Thanks for the note.