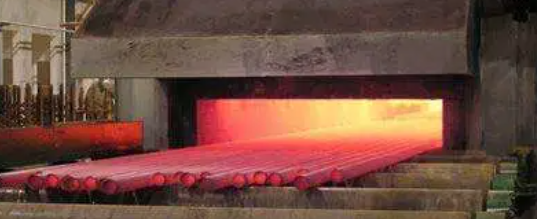
We frequently receive requests for help developing welding procedures for welding on quenched and/or quenched and tempered steels. Sometimes the call for help is to determine why these steels cracked after welding and how to prevent it from happening in the future. Understanding the supplied condition of the steel you are going to be welding is extremely important when developing a welding procedure.
The information below is an excerpt from Welding Procedure Development for Non Welding Engineers on the chapter relating to Base Metal Considerations.
Weldability does not simply refer to whether or not a metal can be joined by welding. This term, unfortunately, is interpreted to mean many different things. However, the weldability of a base metal describes both the ability to successfully fabricate a component using welding and the capacity for that component to perform adequately in its intended service environment.
To illustrate weldability think of welding cast iron. Cast iron is weldable because it can be joined by welding. However, it has poor weldability because it is extremely crack sensitive. Understanding the weldability of the base metal is key in developing the right welding procedure. Remember, a welding procedure is not simply selecting a welding process and parameters such as amperage and voltage. It may involve preheating, post weld heat treatment, specific welding sequences, specific bead placement, etc.
It is imperative that you have a thorough understanding of the supplied condition of the base metal you are welding, its chemistry, how it is affected by the heating and cooling cycles induced by welding, and what the service conditions of the fabricated product will be. Let’s look at the importance of understanding the supplied condition of the base metal.
Supplied Condition of Base Metal
A base metal may have different levels of weldability depending on which condition it is supplied. That is, annealed, normalized, quenched and/or tempered.
When steel is hot worked or cold worked during the manufacturing and forming processes, residual stresses are introduced in the steel. These residual stresses may not allow the steel to perform as intended. In order to attain the right levels of hardness, ductility and toughness the steel must undergo heat treatment to relieve internal stresses and to attain the desired mechanical properties.
The most common heat treatments are: annealing, normalizing, quenching, and tempering. The heat treatment performed will determine the condition of the steel you will receive and will affect its weldability.
Annealing involves heating the steel in a furnace to a temperature 100F [38C] above the critical temperature. This temperature is then held for a certain amount of time to allow the carbon to dissolve and diffuse throughout the metal. The steel is then allowed to cool slowly inside of the furnace at a controlled rate. Annealing helps refine the grain structure of the steel and make it more ductile. It also gets rid of most residual stresses, resulting in excellent weldability.
Normalizing involves heating the steel at a temperature above the annealing temperature and then taking it out of the furnace and letting it cool in air. The result is an increase in hardness and strength when compared to annealing. Normalized carbon and low alloyed steel will be less ductile than when annealed. Normalized steel also has excellent weldability.
Quenching involves the rapid cooling of steel in air, water or oil. Typically it is done in either water or oil. Oil provides slower cooling than water but it is very useful because it can prevent quenching cracks. Steel that will undergo quenching is typically medium carbon and alloyed steel. The result is very high hardness and strength, but this comes at the expense of ductility. Quenched steels are very brittle and very crack sensitive when it comes to welding. They also tend to have residual stresses that make welding even more complicated. It is not advisable to weld a quenched steel because they are highly susceptible to cracking.
Tempering is done after quenching in order to regain some ductility and eliminate residual stresses. Tempering is done by reheating the steel after the quenching process and allowing it to cool slowly in air. Hardness is reduced and the residual stresses are eliminated. The reheating temperature depends on the material type. Quenched and tempered steels have medium weldability. They can successfully be welded without problems but the welding procedure must be properly developed and tightly controlled. It is also important to know that welding will change the mechanical properties of the base metal in the heat affected zone. This may require additional heat treatment to restore the quenched and tempered properties.
Steel supplied in the annealed or normalized condition will typically have excellent weldability. This means it is not very crack sensitive, but care must still be taken. Steel can also be supplied in the quenched and tempered (Q&T) or hardened and tempered (HT) condition. Welding in the Q&T or HT condition is not recommended. The high strength and hardness coupled with low ductility of the base metal will have significantly different expansion and contraction rates than the weld metal. This may result in very high residual stress which may end up causing cracks.
If Q&T steels have to be welded, it is very important to follow proper preheat and interpass temperatures as well as understand what kind of postweld heat treatment (PWHT) may be necessary.
It is recommended that Q&T steels be annealed prior to welding to prevent cracking. Then, to regain the Q&T properties, the proper PWHT must be applied. Welding of Q&T steels without annealing is possible, but potential issues include cracking or loss of desired mechanical properties.
Reference: Welding Procedure Development for Non Welding Engineers