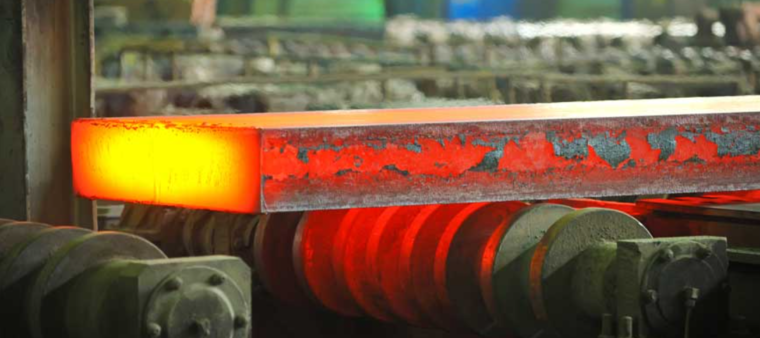
Both hot rolled and cold rolled steels can easily be welded. However, there are differences between the two that will impact which you choose to use. Making this choice depends on several factors such as strength, surface finish, dimensional accuracy and cost.
To understand the difference between hot rolled and cold rolled steel and how they can impact welding we need to look at 4 different areas: manufacturing process, surface finish, dimensional accuracy and mechanical properties.
Manufacturing Process
Hot rolled steel is produced by heating a steel billet above its recrystallization temperature (about 1700°F [927°C]) and then passed through a series of rollers to reduce its thickness. Cold rolled steel is produced by taking hot rolled steel and letting it cool to room temperature and then passing it through a series of rollers.
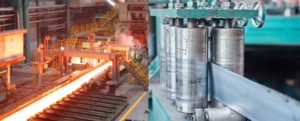
The hot-rolled process is considerably faster than the cold rolling process due to how malleable steel is at higher temperatures.
Surface Finish
Due to the high temperatures at which it is formed, hot rolled steel typically has a rough and scaly surface. Hot rolled steel can easily be identified due to the presence of mill scale. Cold rolled steel undergoes a much cleaner forming and rolling process since it is performed at room temperature. It ends up with a very smooth surface which is free of mill scale.
Dimensional Accuracy
Hot rolled steel is much less precise in terms of dimensional accuracy than cold rolled steel. Because the hot rolling process is less controlled, warping and shape variations are quite possible. The cold rolled process provides much better dimensional accuracy (thickness, width and shape) due to the process being much more controlled.
Mechanical Properties
Both hot rolled and cold rolled steels can provide adequate strength levels. However, hot rolled steel provides higher yield strength and ductility than cold rolled steel. Cold rolled steel has higher hardness levels which may be advantageous in some applications and a detriment in others.
As stated above, both hot rolled and cold rolled steels have good weldability. But the differences in their manufacturing process require welders to adjust their process. For instance, since hot rolled steel has mill scale, it requires welders to remove it by grinding, blasting or other processes. This extra operation adds cost to the manufacturing process, but it is necessary to avoid weld discontinuities such as lack of fusion. Welders can choose not to clean the mill scale and hope their welding process provides sufficient heat to achieve proper fusion, but this may be a dangerous game to play.
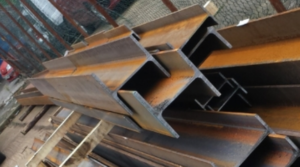
Mill scale is produced during the hot rolling process of steel. It is an iron oxide that sticks to the surface and may present problems in operations such as welding, coating and painting.
Another very important difference is that hot rolled steel will be more prone to dimensional inaccuracies, both before and after welding. The manufacturing process will produce variations and even warping in hot rolled steel, but it also introduces residual stresses that can cause distortion problems when welding. If we understand these effects, we can always deal with them by the use of preheat, post weld heat treatment, better fit up, pre-cambering, etc. This also adds to the cost of welding hot rolled steel compared to cold rolled steel which is less prone to distortion and has much better dimensional accuracy. In general, the uniformity of cold rolled steel provides a reduced risk of distortion.
When considering cost, hot rolled steel is more affordable. However, as stated above, it may require additional operations such as cleaning and preheating before welding and/or applying post heat after welding. With proper selection of welding processes, filler metal and welding parameters, fabricating costs can be kept relatively low and make welding of hot rolled steel a better option as compared to cold rolled. At times, the dimensional accuracy is what requires that cold rolled steel be used. Due to its different mechanical properties the welding procedure used may differ from the one used for hot rolled steel.
References:
Welding Metallurgy and Weldability by John C. Lippold
Are you tasked with developing, qualifying and approving welding procedures? Are you in need for procedures that adhere to AWS D1.1 Structural Welding Code – Steel? If so, the use of prequalified Welding Procedure Specifications will help you save time and money. It will also help with quality and consistency. Qualification testing for a single welding procedure can cost over $1,000 depending on the necessary tests. Prequalified WPSs are exempt from testing and ready to use.
Please note: I reserve the right to delete comments that are offensive or off-topic.