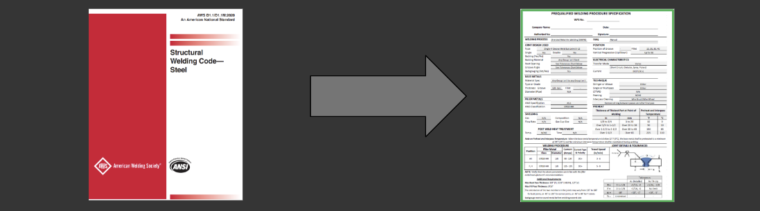
The structural welding code for steel, AWS D1.1, allows the use of prequalified welding procedures. This results in a tremendous advantage to the steel fabricator. Prequalified welding procedure are necessary and extremely useful for any fabricator looking for consistency in quality and productivity. This instructional article will walk you step by step in writing a prequalified WPS.
A common misconception is that one needs to be a certified welding inspector (CWI) in order to write prequalified welding procedures. This is not true. However, CWIs write most prequalified WPSs because they understand the code and following all the requirements for prequalification is something they understand well.
But anyone that takes time to read and understand the code can write prequalified welding procedures. We’ll show you how. But before we get into the steps to follow let’s review a couple of important aspects of prequalified WPSs.
First, why are they necessary?
Prequalified WPSs…
- Are exempt from testing to achieve qualified status – this saves a lot of time and especially money. Qualifying a single procedure by testing can range between $500 to $1200.
- Assure that you are using a WPS that will produce sound welds, rather than guess or go simply by the way a weld looks to gauge its quality.
- Don’t need to be developed or written by a welding engineer or a certified welding inspector (CWI) – all you need is to follow the requirements of the Prequalification clause in AWS D1.1 Structural Welding Code
Second, what is needed to develop, write and use a prequalified WPS?
- You need a copy of the latest edition AWS D1.1 Structural Welding Code (Steel). Without the code book it is extremely difficult to do so. As of the writing of this guide, the cost of AWS D1.1/D1.1M:2020 Structural Welding Code – Steel is $509 for AWS members and $679 for non-members. Write a couple of prequalified WPSs and it pays for itself!
And that’s it. That’s all you need!
8 Steps to Write Prequalified Welding Procedures
AWS D1.1 Structural Welding Code (Steel) provides all the instructions on how to write prequalified welding procedures. In the latest edition of the code (2020) the Prequalification clause was arranged in a manner that helps the user in putting together the procedures.
There are 8 main steps to write prequalified WPSs. These are:
- Selecting an approved Base Metal for prequalified WPSs
- Selecting a prequalified Weld Joint
- Selecting a prequalified Welding Process
- Selecting the appropriate filler metals and shielding gases
- Determining the necessary (if any) Preheat and Interpass Temperature
- Determining the necessary (if any) Post Weld Heat Treatment
- Understanding all Mandatory WPS Requirements
- Writing your first Prequalified WPS
STEP 1: Selecting an approved Base Metal for Prequalified WPSs
Prequalified Welding Procedure Specifications (WPSs) can only be used on approved base metals. A list of approved base metals is provided in Table 5.3 – Approved Base Metals for Prequalified WPSs of AWS D1.1/D1.1M:2020 Structural Welding Code (Steel).
If a base metal is not listed in Table 5.3 it cannot be used in a prequalified WPS. If this is the case it must be qualified by testing per Clause 6 – Qualification of AWS D1.1/D1.1M:2020.
Below are approved base metals for prequalified WPS commonly used in general steel fabrication. This is not an exhaustive list, please refer to Table 5.3 for a complete list.
- ASTM A36
- ASTM A106
- ASTM A500
- ASTM A516
- ASTM A572
- ASTM A573
- ASTM A588
- ASTM A709
- ASTM A710
- ASTM A1008
- ASTM A1011
- API 5L
- ABS Grades A, B, D, E
Now that you have selected an approved base metal for your prequalified WPS the next step is to select a prequalified weld joint.
STEP 2: Selecting an approved Weld Joint for Prequalified WPSs
Prequalified WPSs must use approved welding joints. Figure 5.1 through 5.5 of AWS D1.1/D1.1M:2020 provide the joint details for all prequalified weld joints. It is important to follow not just the types of joints but also all tolerances.
When using weld joints from Figures 5.1 and 5.2 you must also pay special attention to the footnotes. Footnotes provide additional instructions and limitations. Not adhering to the instructions and requirements of footnotes can make a prequalified WPS noncompliant.
Below is an example of a prequalified weld joint being used in a prequalified WPS.
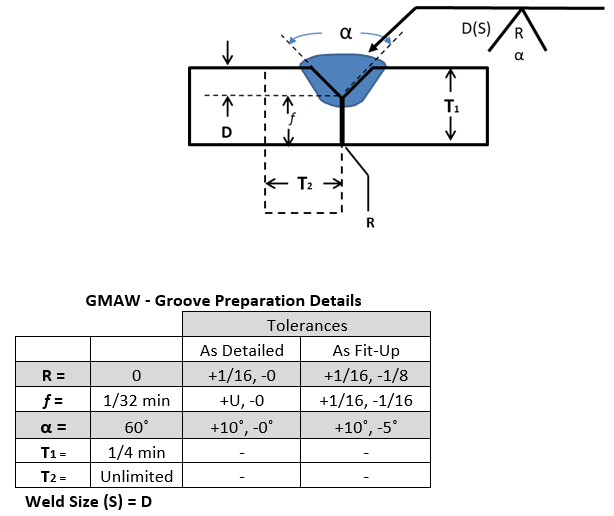
This prequalified weld joint is for a single V-groove weld butt joint (BC-P2-GF). AWS D1.1/D1.1M:2020 Structural Welding Code (Steel) provides prequalified weld joints for fillet welds, complete joint penetration (CJP) welds and partial joint penetration (PJP) welds. Refer to Figures 5.1 through 5.5 of your code book.
As stated above, it is important to pay attention to the footnotes when looking at the code book. For this particular joint and for the GMAW process the footnotes specify the following additional requirements:
- The joint shall be welded from one side only.
- Minimum weld size (S) as shown in Table 5.5. Depth of groove (D) as specified on drawings
- The orientation of the two members in the joints may vary from 135˚ to 180˚ for butt joints, or 45˚ to 135˚ for corner joints, or 45˚ to 90˚ for T-Joints
As seen above, the prequalified joint has “as detailed” and “ as fit-up” tolerances. These must be strictly kept to remain compliant.
So, there you have it. Now you know how to select an approved base metal and a prequalified weld joint for your prequalified WPSs.
STEP 3: Selecting a Prequalified Welding Process
AWS D1.1 Structural Welding Code – Steel allows certain arc welding processes for use with prequalified WPS.
Welding process which are permitted for used with prequalified WPSs are:
- Shielded Metal Arc Welding (SMAW)
- Submerged Arc Welding (SAW)
- Gas Metal Arc Welding (GMAW), except GMAW-S
- Metal Cored Arc Welding (MCAW)
- Flux Cored Arc Welding (FCAW)
The welding processes below are NOT approved for prequalified WPS but which may be used if qualified by testing following the requirements of Clause 6 – Qualification of AWS D1.1/D1.1M:2020 Structural Welding Code (Steel).
- Gas Metal Arc Welding – Short Circuit (GMAW-S)
- Gas Tungsten Arc Welding (GTAW)
- Electroslag Welding (ESW)
- Electrogas Welding (EGW)
Once you have selected a prequalified welding process you need to choose welding consumables (electrode, shielding gas and flux) approved for use with the base metal selected earlier.
STEP 4: Selecting filler metals, shielding gases and fluxes
Although it may be advantageous to use an undermatching filler metal, AWS D1.1 provides a list of matching filler metals for all approved base metals.
When using prequalified WPSs the filler metal must be selected from Table 5.4 – Filler Metals for Matching Strength for Table 5.3 Groups I, II, III and IV Metals from AWS D1.1/D1.1M:2020.
These filler metals provide matching strength, that is they match the minimum specified tensile strength of the base metal.
In general, the specified minimum tensile strength for the four base metal groups is as follows:
- Group I 70,000 psi
- Group II 70,000 psi
- Group III 80,000 psi
- Group IV 90,000 psi
Refer to Table 5.4 of AWS D1.1 for additional information.
If you are using weathering steel you must follow the requirements of Table 5.6 – Filler Metal Requirements for Exposed Bare Applications of Weathering Steels when selecting the right filler metal.
For processes that use shielding gas such as GMAW and FCAW, an approved shielding gas must be used. Table 5.7 – Prequalified WPS Shielding Gas Options for GMAW Electrodes Conforming to AWS A5.18/A5.18M for AWS D1.1 provides a list of the permitted gases and the composition ranges.
These ranges are as follows:
For electrode classifications ER70S-X (except ER70S-G) and E70C-X metal cored electrodes the following shielded gases are permitted for use with prequalified WPSs.
- Argon / Carbon Dioxide with composition ranges of Argon 75-90%, balance Carbon Dioxide
- Argon / Oxygen with composition ranges of Argon 95 – 98%, balance Oxygen
- Carbon Dioxide
In addition to the shielding gases listed in Table 5.7, any shielding gas that has been tested in accordance with the applicable A5 filler metal specification and which has demonstrated to be capable of meeting all the mechanical and chemical properties and NDT requirements for the electrode classification may be used. A way to ensure this is to ask the manufacturer of the filler metal for a certificate of conformance. If a certificate of conformance shows a specific shielding gas for which the necessary results have been achieved then it may be used for prequalified welding procedures.
Always ensure that the requirements set forth in section 5.6.3 of AWS D1.1 are being met.
If using the submerged arc welding (SAW) process, a flux must be used. Table 5.4 – Filler Metals for Matching Strength for Table 5.3 Groups I, II, III and IV Metals from AWS D1.1/D1.1M:2020 provides the approved filler metal and flux combination. For example, an approved filler metal/flux combination for welding ASTM A36 steel is
F7XX-EXXXX
The “X’s” designate multiple values, for example F7A2-EM12K.
STEP 5: Determining preheat and interpass temperature
Preheat is necessary to prevent embrittlement and cracking of the weld and heat affected zone. The base metals approved for use with prequalified WPSs per AWS D1.1 have a relatively low carbon content and necessitate preheating only when exceeding a certain thickness.
Table 5.8 – Prequalified Minimum Preheat and Interpass Temperature of AWS D1.1 provides the minimum preheat and interpass temperature for all prequalified base metals. Keep in mind that the same base metal may require different preheat and interpass temperatures depending on its thickness. For example, the minimum preheat and interpass temperature for ASTM A36 is as follows:
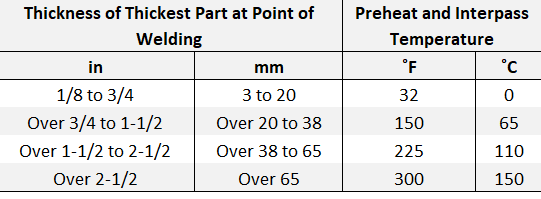
STEP 6: Determining post weld heat treatment (PWHT)
Post weld heat treatment (PWHT) is performed after welding to maintain or improve material strength and mechanical properties and to relieve residual stresses. In steel fabrication, the most common PWHT procedures applied are post heating and stress relieving.
Post heating is primarily done to avoid hydrogen induced cracking (HIC), also known as cold cracking and hydrogen assisted cracking (HAC).
Stress relieving is done at a much higher temperature and usually for a longer period of time than post heating. Stresses can develop in weldments due to high levels of restraint and shrinkage forces. These stresses may not cause the part to crack right away, but significantly reduce the fatigue life of the welded structure or component.
Stress relieving will reduce these residual stresses that are present after welding by carefully controlling the heating of the part to a specific temperature, holding it for a specific amount of time and then controlling the cooling rate.
When contract documents demand that PWHT is carried out the requirements of AWS D1.1 must be followed unless otherwise stated. In order for PWHT to be prequalified it must be approved by the engineer in charge and the following conditions must be met.
- The specified minimum yield strength of the base metal does not exceed 50 ksi [345 MPa]
- The base metal should not be manufacture by quenching and tempering (Q&T)
- There are no requirements for notch toughness
- There is enough data showing that the weld and HAZ provides adequate strength and ductility in the PWHT condition.
Additionally, PWHT needs to be conducted in conformance with Section 7.8 – Stress Relief Heat Treatment of AWS D1.1/D1.1M:2020 Structural Welding Code – Steel. This section provides instructions, temperatures and holding times for conducting PWHT
Most PWHT procedures are very well established and provided by contract documents. All you need to do is verify that the above conditions are met.
STEP 7: Understanding all mandatory WPS requirements
The reason why there are so many rules, requirements and limitations for the use of prequalified WPSs is because we are bypassing testing to qualify the procedure. However, if we follow all the rules we have reasonable assurance that we’ll be able to make sound welds. This is because these rules and requirements have been proven over and over to produce sound welds.
Table 5.1 – Prequalified WPS Requirements of AWS D1.1/D1.1M:2020 Structural Welding Code (Steel) provides limits for the following:
- Maximum electrode diameter
- Maximum current
- Maximum root pass thickness
- Maximum fill pass thickness
- Maximum single pass fillet weld size
- Maximum single pass layer width
As with many other tables in AWS D1.1 this table has several footnotes. Pay special attention to these footnotes as you write your prequalified WPS.
If you take a look at Table 5.1 you’ll see that for Maximum Current there is a note that reads “Within the range of operation recommended by the filler metal manufacturer.” This brings us to the final part of the course: Selecting the right welding parameters and writing your first prequalified WPS.
STEP 8: Writing your first prequalified WPS
So far this course has taught you how to select everything that goes into developing a prequalified WPS. The only missing pieces are the actual welding parameters (current or wire feed speed, voltage).
Before you select the welding parameters you need to know not just what filler metal you will be using, but what brand. Once you have this determined, simply go to the recommended operating parameters suggested by the manufacturer of the filler metal and use those for your prequalified WPS.
For example, if you choose to use the GMAW process and select Super Arc L-56 as your ER70S-6 filler metal you would need to consult Lincoln Electric’s literature on this filler metal to get your parameters. Upon doing so, you would see a table like this.
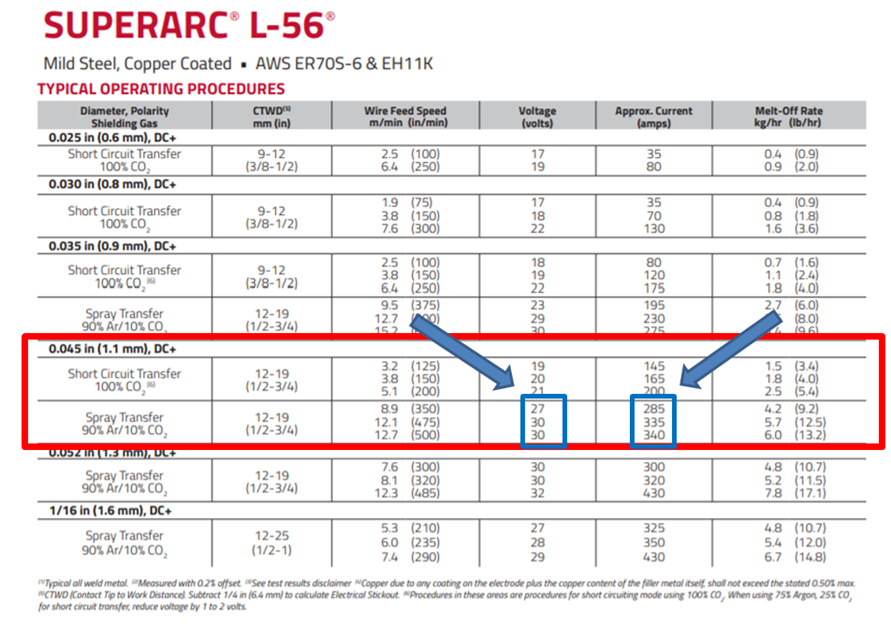
If you recall from one of the earlier lessons, short circuit transfer is not allowed in prequalified welding procedures. You are limited to spray transfer in this case. The blue arrows and boxes give us our parameter ranges.
So, our wire feed speed would be 350 to 500 inches per minute, our current 285 to 340 amperes and our voltage 27 to 30 volts.
One last check…Table 5.2 Essential Variables for Prequalified WPSs provides variable tolerances for prequalified WPSs. A welding procedure cannot have parameter ranges that are too wide, otherwise we would run the risk of running a voltage that may be way too low for a given current.
If you see Table 5.2 you’ll see that your range for amperage is +/- 10%. From the example above our current range is 285 – 340. This falls within tolerance allowed by AWS D1.1 as it would be 312 amps +/- 10% or 280 to 343 amps (with 312 being the middle value).
Perform these checks for voltage as well as you are all set.
Prequalified WPSs are also required to specify other variables such as contact tip to work distance (CTTWD). This is also a welding parameter provided by the filler metal manufacturer. For our example, the require CTTWD to run 285 to 340 amps is ½” to ¾”.
You are now ready to write your first prequalified WPS!!!
Just grab your copy of AWS D1.1 Structural Welding Code – Steel and follow the instructions above. If you do not have the latest copy of AWS D1.1 head over to the AWS Online Bookstore and purchase your copy.
We hope you enjoyed this FREE course on How to Write Prequalified Welding Procedures in conformance to AWS D1.1 Structural Welding Code – Steel.
WOULD YOU RATHER HAVE PREQUALIFIED WELDING PROCEDURE DONE FOR YOU?
You have been provided clear instructions on how to write prequalified WPSs in accordance with AWS D1.1 Structural Welding Codes – Steel. We hope that you now feel comfortable in writing your prequalified WPSs. However, not everyone will choose to do so. If you rather have the prequalified WPSs done for you we can help.
Our publication 322 Prequalified Welding Procedure Specifications for Steel Fabricators provides prequalified WPSs for SMAW, GMAW, MCAW, FCAW-G and FCAW-S.
If you only need prequalified welding procedures for a specific process those are available as well. Simply visit our online store to choose what you need.
322 Prequalified Welding Procedure Specification for Steel Fabricators
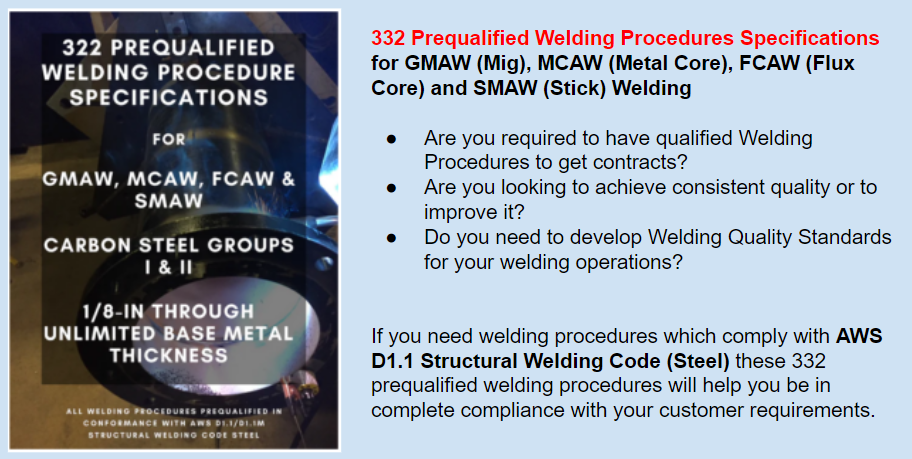