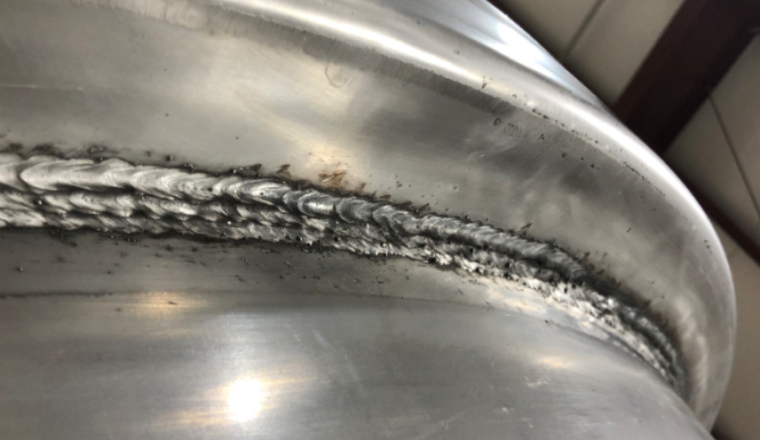
Rework is extremely costly, especially in welding. If you consider what happens when a weld is rejected it is essentially triples the amount of work. You weld, you remove the weld, you reweld. On top of this it may require additional inspection. So, reducing rework can save considerable amounts of time and money.
Rework in welding shows up in many forms. However, there are three main areas of welding problems that cause a lot of rework. These are:
- Distortion
- Spatter
- Discontinuities (cracks, undercut, porosity, etc.)
These welding problems can be complex. For example, spatter may be caused by incorrect welding parameters, base metal surface contaminants, poor fit up, lack of welder skill, incorrect torch angle, loss of voltage due to equipment issues, incorrect gas selection, and much more. Naturally, we can say that to reduce rework we must: select adequate welding parameters, properly prepare the weld joint, ensure good fit up, train welders, keep the right torch angles and ensure the welding equipment is in good repair.
All of these are good ideas. However, based on our experience, if we had to pick 3 minor changes that would have the biggest impact on rework it would be to stop overwelding, to use qualified welding procedures and to properly maitain welding equipment. Let’s look at each in a bit more detail.
Don’t overweld
The idea that a bigger weld is better is flawed. It does not just represent wasted filler metal, but can cause a lot of problems such as distortion, overlap, exceeding heat input maximums, premature corrosion in stainless alloys and much more. If you can do only one thing, control your weld sizes.
If the product you are welidng is your design then make sure you are taking advantage of minimum weld sizes and that your design engineers are properly trained in sizing welds if they don’t have software tools to do this for them.
If you are welding to a customer’s design, ask them to specify weld sizes. However, in most cases, your customers may not know what weld size to specify and will rely on you as a fabricator to determine that. Here’s where you can get in trouble and add cost to your operations in the form of wasted material and the introduction of rework. If you do not have the expertise in-house to determine weld sizes you should pay for this service from a reputable firm. We often see welds, mainly fillet welds, that are overwhelmed by 2 and 3 sizes, meaning that a fillet weld that should have a leg size of 3/16-in will actually be 5/16-in or even ⅜-in in production. If you want to have an idea of how costly this is read Bigger Welds Are Not Always Better.
Use properly developed and qualified welding procedures
When welding procedures are developed and qualified properly they provide reasonable assurance that a good weld will be deposited. Of course, welder skill is still essential. The best welding procedure can be worthless if the welder does not possess the skills to deposit a quality weld. This is why every welding quality program must include welder performance qualification tests. The use of welding procedures ensures that the many variables in welding don’t work against you, but for you.
Prequalified welding procedures provide a simple solution for fabricators that may not have a welding engineer or other welding expert to develop procedures for them. Prequalified WPSs are allowed by certain codes and standards because they must conform to many rules, limitations and requirements that assure quality.
Prequalified welding procedures can be purchased and used in production immediately; however, If you work with carbon steel and are interested in creating your own prequalified WPSs you can follow our simple guide on How to write AWS D1.1 Prequalified Welding Procedures. These step-by-step instructions will guide you in putting together welding procedures for carbon steel, more specifically base metal in Groups I & II based on AWS D1.1 Structural Welding Code – Steel.
Prequalified WPS can also be purchased for immediate use.
Properly maintain welding equipment
In our industry we sometimes pride ourselves on the age of our equipment. Although there is nothing wrong with welding machines that are 10, 20 or even 30 years old, many times we forget that welding machines need preventive maintenance (PM) just like the cars we drive. If we neglect this PM, our welding machines will continue to operate but will alter their output.
Of concern to welders is that when machines have output fluctuations it changes the arc characteristics and also essential variables such as amperage and voltage. Poor equipment maintenance coupled with the lack of a daily maintenance check by the welder can result in significant rework. Even something like a loose work clamp connection can result in a significant loss of voltage which may lead to spatter, excessively convex welds, lack of fusion and other problems.
To know if you must address this very important item simply do a walk-through of your shop and look at the condition of the equipment. Are connections tight? Are there any splices in your leads? Are cables frayed at connection points? Are your cables undersized? Do you have loose electrode and/or work cable connections? Do you see a lot of electrical tape being used in welding leads? All of these things are indicators that you may have rework associated with poor equipment maintenance.
The above three recommendations may seem too simple to make an impact. However, if you can do these three consistently you will reap the benefits.
How well is your shop controlling rework?
References:
Weld Troubleshooting for Non-Welding Engineers
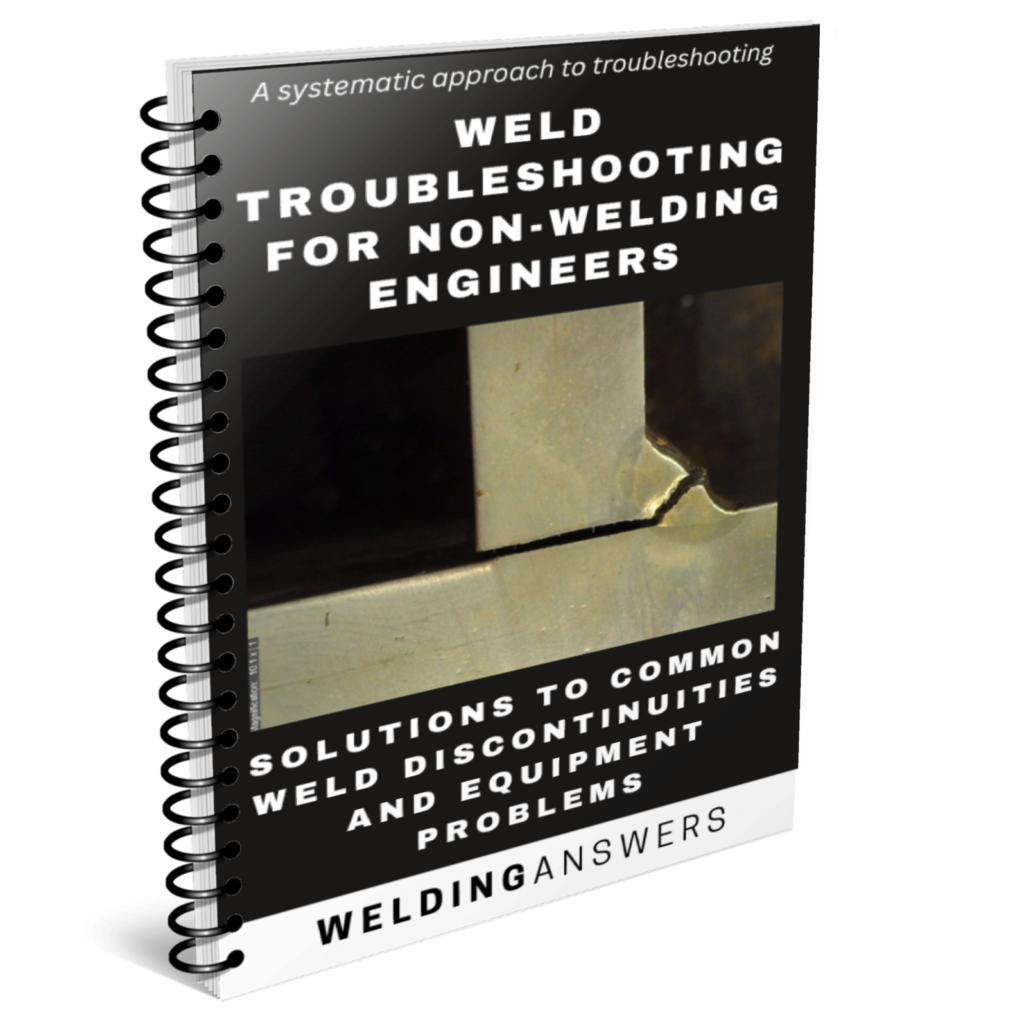