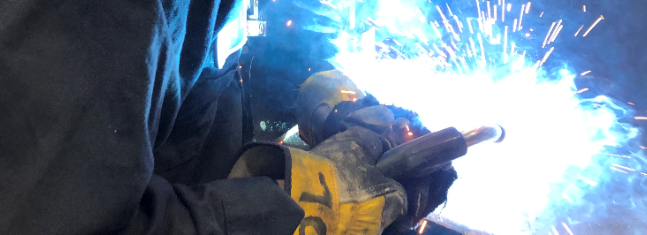
We all know welding fumes are bad for your health. Companies that do a lot of welding are paying special attention to this matter and trying to create better working environments not just for welders but for everyone in the shop. Has your company taken any steps to reduce or control fume generation? In this article we outline in specific order the steps that must be taken reduce and control welding fume exposure.
Before talking about the steps there are two important things you need to understand in relation to exposure limits. There are two things that industrial hygienists are concerned about when doing an audit.
- The concentration of the toxic elements in welding fume, mainly the metals that are vaporized and can enter our breathing area.
- The amount of time workers are exposed to welding fumes.
So naturally it makes sense that our goal should be to reduce the concentration of the fumes and reduce exposure times. Again, not just for the welder but for everyone that works in or walks through the shop.
OSHA sets specific engineering and work practice controls which must be to control welding fumes. The use of personal protective equipment should be the last resort. Many companies jump straight into providing powered air purifying respirators (PAPRs) to their welders, but they forget that doing this only protects the welder. So the correct approach is as follows:
Engineering Controls
- Substitution – this involves examining whether we can substitute the welding process to one that generates less welding fumes. An example would be switching from flux-cored arc welding (FCAW) to gas metal arc welding (GMAW), or switching from globular GMAW transfer to spray transfer. You can go as far as going from welding to using bolts for some connections.
- Isolation – this involves physically separating welding activities from all other activities in a fabrication shop.
- Ventilation – this involves controlling how the welding fumes move through the shop. This can be creating drafts that move the welding fumes to specific location within the shop or out of the shop (if you vent be careful with the EPA). Ventilation also includes source capture which is the use of fume extractors that remove the welding fumes right at the source (the arc) or that can be placed throughout the shop to clean the air.
Safe Work Practice Controls
Safe work practice controls deal with how a specific job is performed. For example, you can train and/or instruct your welders to keep their head out of the plume as to avoid having the welding fumes enter his or her breathing area. This can also mean performing jobs on a specific scheduled or place to limit exposure.
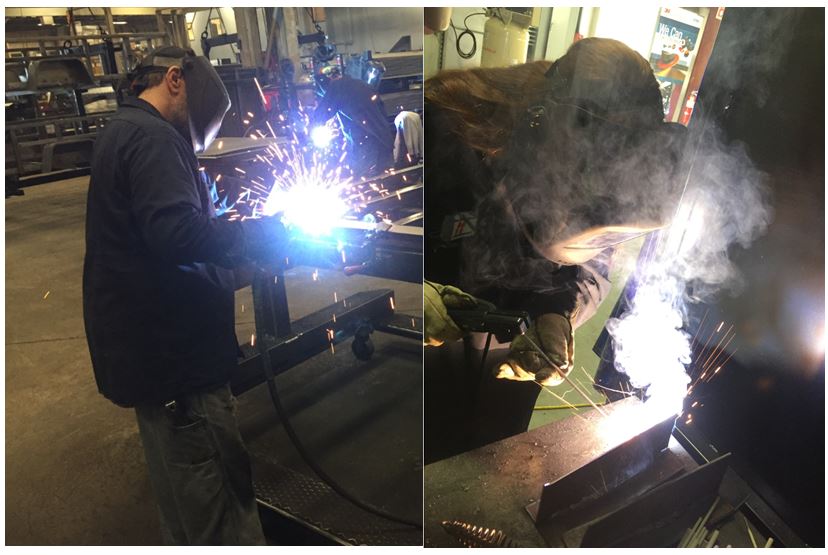
Example of safe work practices – the welder on the left is keeping his head out the welding plum while the one on the right is breathing in a higher amount of fumes due to head position.
Personal Protective Equipment (PPE)
The use of PPE may be necessary if engineering controls and safe work practices are unable to provide a safe work environment for the welders. Please know that OSHA requires that employers that go this route develop a respirator program that includes items such as medical evaluations, training, recordkeeping and fit testing for the personnel that will be using PPE such as PAPRs.
The reason PPE is the last step is because this will only protect the welder. PPE should be used in conjunction with general ventilation in order to provide a safe environment for all.
How are you controlling welding fumes in your facility?
Are you looking for a guide to troubleshooting and solving the most common welding and welding equipoment problems? Our guide: Weld Troubleshooting for Non-Welding Engineers will definitely help. It provides a systematica approach to troubleshooting problems such as porosity, cracks, lack of fusion, undercut, overlap, burn-through and equipment problems such as erratic wire feeding, birdnesting and more.
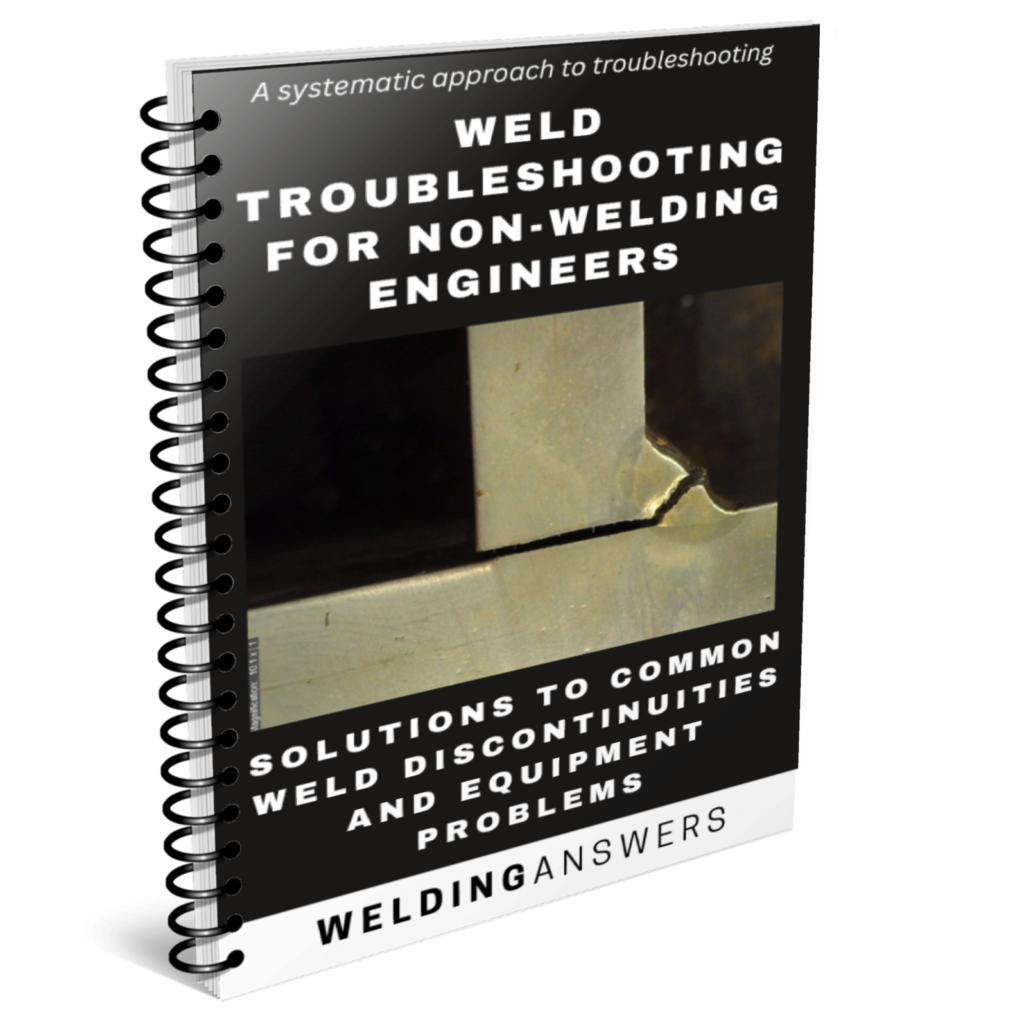