
Stainless steels possess many properties that make them different from those of carbon steels. These differences provide certain advantages, such as corrosion resistance, but we must be aware of some of the intricacies of welding stainless steel to avoid problems.
Many welding professionals, including welding engineers, that have worked primarily with carbon steels develop welding procedures for stainless steels without considering the properties below. This can lead to many problems.
Properties of special interest are:
- Thermal conductivity
- Thermal expansion
- Corrosion resistance
- Oxidation resistance
- Hardenability
Thermal conductivity of stainless steels is much lower than that of carbon steels. This makes stainless steels very susceptible to local overheating and distortion when welded. Special attention must be paid to the heat input generated by the welding procedure used. Distortion and buckling is very common when welding stainless steel, especially thinner gauges. Minimizing the weld size and keeping heat input as low as possible can help mitigate these problems.
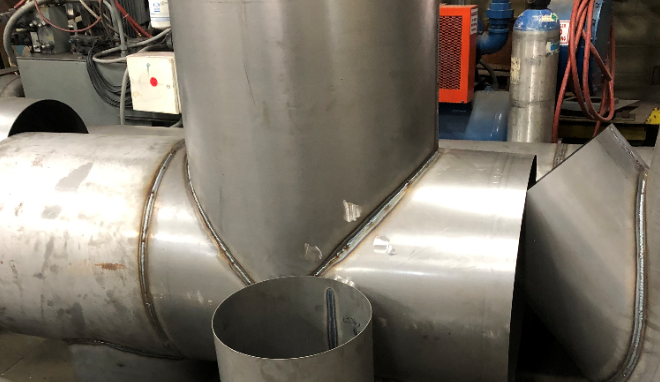
Thermal expansion is higher in stainless steel than carbon steels. This also facilitates distortions due to the larger increase and decrease in volume due to the heating and cooling cycle introduced by the welding process. Additionally, this higher thermal expansion produces higher residual stresses on welds during cooling. It is important to be aware of this especially when welding stainless to carbon steel. Using a 309 filler metal is always recommended, primarily because it prevents cracking that can occur due to the significantly different coefficients of thermal expansion.
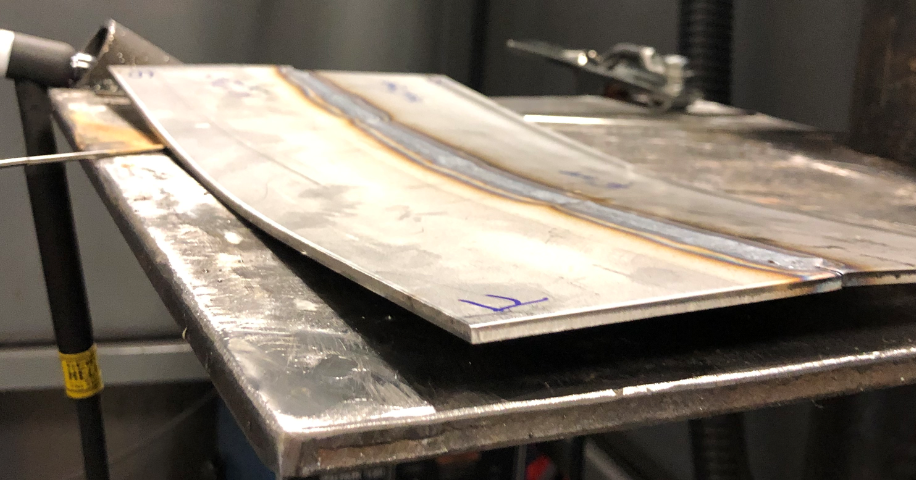
Corrosion resistance is much higher in stainless steels than carbon steels. This corrosion resistance is aided by the high levels of chromium and nickel. The welding process can affect this corrosion resistance. If high heat inputs are used which result in slow cooling rates a situation called sensitization may occur. This can lead to cracking in the sensitized zone.
Oxidation resistance is important because it facilitates cutting by oxy-acetylene. Because stainless steels resist oxidation until heated to temperature near or above their melting point in the presence of air, it requires the use of plasma cutting, laser, waterjet or other cutting processes. Do not attempt to cut stainless with the oxy fuel cutting process.
Hardenability is usually something that we care about in carbon steels. After all, high carbon content is the main driver for hardenability. However, martensitic stainless steels have very high hardenability. This can result in embrittlement with the heating and cooling cycle of the welding process.
As you can see, these characteristics of stainless steel force us to be very careful when developing welding procedures. Assuming it welds similar to carbon steel is a big mistake that can lead to problems such as premature corrosion, distortion and cracking.
It is imperative to understand that stainless steel and carbon steel are completely different. We must always approach welding procedure development with a sound understanding of the physical and mechanical properties of the base metal we are welding.
Have you had any issues with welding stainless steel? Do you struggle with distortion or premature corrosion?
References:
Welding Metallurgy and Weldability by John C. Lippold
Do you need weldnig procedures for welding stainless steel? Do you need to comply to AWS D1.6 Structural Welding Code – Stainless Steel? This collection of 280 Stainless Steel Prequalified WPSs contains procedures for SMAW, GTAW, FCAW and GMAW for welding autenitic stainless steel. Developed in full conformance with AWS D1.6.

Looking for information on how to develop your own welding procedures? Following basic principles and having an understanding of the effects of welding variables is fundamental. Welding Procedure Development for Non Welding Engineers was written to help those developing welding procedures.
Welding of stainless steel generally creates different degree of colors or tints along and adjacent to weld heat affected zone. How can we distinguish them to indicate if the area has excessive heat exposure, and what color condition will it be considered as rejectable due to high probability of getting corrosion.
What is the recommended method of preventing occurrence of iron oxide (rust-like indications) on weld areas and heat affected zones of welded stainless steels?
Great questions. The colors you see in stainless welds indicate oxidation. Ideally you would get zero discoloration. The acceptable amount depends on the base metal. For example, are you welding austenitic stainless steel or some other alloy. The acceptable amount is dictated by the specific code or standard that is followed. Most of this discoloration can be removed after welding and is an acceptable method to meet the acceptance criteria. It can be through mechanical ore chemical means. Read the linked article for additional information: https://weldinganswers.com/rainbow-colors-in-stainless-steel-welding/
In regards to minimizing susceptibility for corrosion the best advice is to use a welding procedure that has been qualified by testing and for which corrosion tests have been conducted. Austenitic stainless steels is what is used most often. In the case of these 300 series stainless steels, the best thing you can do is control your heat input (minimize heat input) in order to minimize the amount of time spent in the sensitization range. Read the linked article for additional information: https://weldinganswers.com/how-to-avoid-sensitization-when-welding-austenitic-stainless-steels/