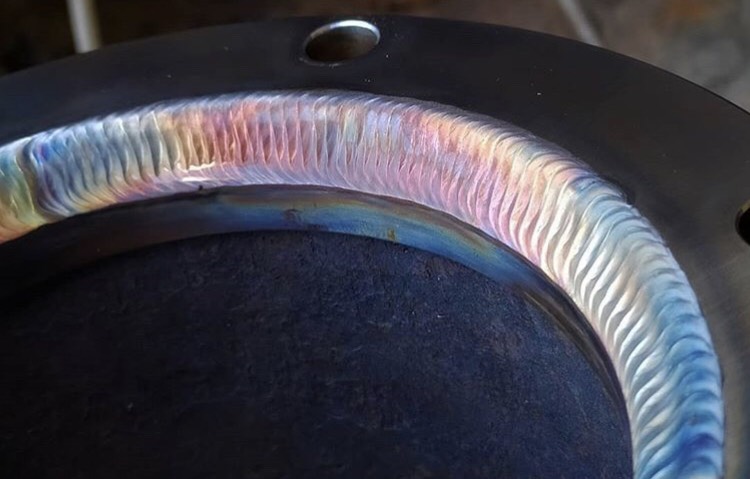
We receive several calls about welding stainless and the beautiful rainbow colors, or lack thereof, on the weld and heat affected zone. Is the tinting an indication of quality? Are these colors acceptable? Do they show that the weld had enough heat to penetrate? Why do they need to be cleaned? The questions are endless.
If you are one of the thousands that base their quality standards on Instagram posts please stop right now. All the beautiful pictures of stainless welds are emphasizing the beauty of the rainbow colors in GTAW and GMAW welds. This is producing a false expectation and the impression that this tinting is good. It may not be bad in some cases, but it is never good. There is more to the weld than what it looks like from the outside.
For instance, take a look at the weld below:
This is a beautiful GTAW weld. More than likely the quality is excellent. The colors are beautiful as well. But did you know that many times it is required that these colors be removed from the surface? This tint is nothing more than oxidation. But we call it ‘rainbow colors’ which makes it seem desirable.
You may have heard that the yellow and straw colors are OK, but blue and purple may not be. The color depends on the temperature experienced by the weld and HAZ. It is also affected by the heat input which determines cooling rates. And lastly, it is affected by contamination from the atmosphere (even with 100% inert gas) and surface contaminants..
Corrosion resistance is reduced by oxidation. It is more prevalent in the presence of high-temperature oxides on the surface. This is due to chromium depletion in both the oxide and underlying alloy substrate.
So if your weld does not look as pretty as the one above don’t worry. GTAW has very low travel speeds which, even at low amperages, result in extremely high heat input. Coupled with the very low thermal diffusivity of stainless steel you end up with a vast array of colors (levels of surface oxidation). The good news is you can remove it. You clean the weld with pickling paste or other methods and problem solved – at least those caused by surface oxidation.
Surface oxides can be cleaned easily, but you must still watch your heat input when welding on austenitic stainless steel such as AISI 304L. The higher the heat input the slower the cooling rate. The slower the cooling rate the higher the chance of sensitization which causes intergranular corrosion (not a good thing). Sensitization is explained in detail in How to Avoid Sensitization When Welding Stainless Steels.
So in summary, do not worry if your stainless welds don’t show all those pretty rainbow colors. Their absence can be a good thing. It is important to develop a welding procedure that produces the quality from a structural standpoint as well as quality in terms of corrosion resistance. Once the procedure is qualified, follow it and don’t deviate.
Take a look at the weld below.
This was a mig (GMAW) weld done at a travel speed of about 35 inches a minute. The welding procedure was .045” ER308LSi at 400 ipm and 26.7 volts with 98/2 (Argon/Carbon Dioxide) shielding gas. The resulting heat input was 10.6 KJ/in which is relatively low. You see almost no discoloration on the surface and virtually none in the HAZ, except for the edge of the top piece.
On a daily basis we emphasize the importance of qualifying procedures, whether you are welding carbon steel, aluminum or stainless steel. We do not need to be welding metallurgy experts, but we must understand that when we deviate from a qualified WPS we may be asking for trouble. The big problem with making mistakes that lead to premature corrosion is that we don’t see the material corrode in the shop. It corrodes prematurely. This means it may corrode in 6 months rather than 3 years. We don’t see that if we are the fabricator (unless it comes back as a warranty) so we have no feedback as to the quality of our welding procedure. Thus the importance of qualification.
Reference: Welding Metallurgy and Weldability by John C. Lippold
Please note: I reserve the right to delete comments that are offensive or off-topic.