Spatter in welding is very common, we see it everywhere. We assume that it is something we have to learn to live with and cannot get rid of. Or, if we can get rid of it, we think that it is more trouble than what it’s worth. If you want to know the causes for welding spatter check out the post on 7 Causes of Spatter and How to Eliminate It.
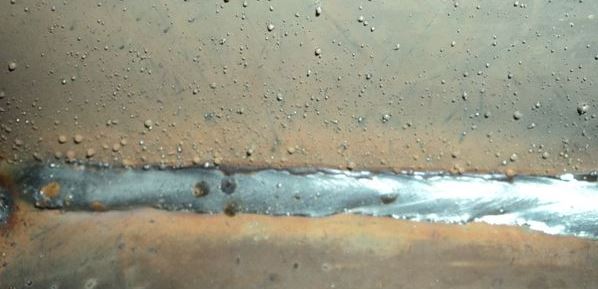
Spatter is more of a cosmetic problem than a weld integrity problem. However, it may be costing you dearly.
The reason why there doesn’t seem to be much effort put into eliminating spatter at a vast number of manufacturing facilities is that most people don’t know the true cost of it. We know spatter looks bad, we know it requires time to grind it off, we may even know that it increases the amount of welding consumables needed for a job. But ask yourself, have I ever sat down to evaluate what spatter is costing me?
The example below is simply meant to get you thinking about what spatter is costing you. The numbers can be changed as you please, but be mindful of the percent reduction in total cost. You may have a special situation where this does not apply, but it would be more the exception rather than the norm.
Spatter Reduction Guide
Subscribe to get our latest content by email and receive your FREE Spatter Reduction Checklist!
Scenario: ACME Welding uses the GMAW process with C25 shielding gas. They use the short arc and globular modes of metal transfer which generate significant spatter. They cannot have spatter on their finished assemblies since they will be painted, and paint makes spatter stick out like a sore thumb. They manufacture the same part day in and day out. This example looks at the cost during a 3-week period, before and a 3-week period after changes were made.
Material and Labor Costs
740# of .045 ER70S-6 Wire ($1,295)
32 Grinding Wheels ($224)
2-gal Anti-spatter ($68)
C25 Shielding Gas ($277)
Labor = 15days x 7welder x8hours = 840 hours @ $45/hr (labor & overhead) = $37,800
Total Cost: $39,664
After switching gas to 90%Ar/10%CO2 and adjusting welding procedures spatter is reduced by 85%. This reduces grinding wheel usage, anti-spatter usage and even amount of wire needed. The wire is reduced because spatter is lost filler metal. About 40# on this job. The gas is more expensive by about 10%. Although in this case better procedures also improved deposition rates, for the sake of the example they were kept the same (7.2#/hr).
Spatter was reduced following the guidelines in 7 Causes of Spatter and How To Eliminate It.
New numbers:
700# of .045 ER70S-6 Wire ($1,225)
32 Grinding Wheels ($90) – not all grinding was for spatter so reduction is not as much percentage-wise.
2-gal Anti-spatter ($68) – shop practice is to use it, so it is still being used although it could have been limited to specific applications.
90/10 Shielding Gas ($304) – upgrade to a more expensive shielding gas that allows for spray transfer.
Labor = 11.8days x 7welder x8hours = ~660 hours @ $45/hr (labor & overhead) = $29,700
New Total: $31,387
This change reduced the cost of this job by $8,277 or 21%. We continually forget about the cost of labor and focus to much on the cost of raw materials. Most companies keep using 100% CO2 or even C25 because it is cheaper than a 90/10 gas shielding mix. A simple switch to a better gas and improving your welding procedures can lead to significant savings.
This example is real. But feel free to plug your own numbers in and see how it applies to you. Sometimes this type of change may require better or bigger (or both) welding power sources. But remember that the savings go on forever because you are reducing spatter and the cost associated from removing it.
Have you undertaken a project to reduce welding spatter? What are your thought? Did you see significant savings?
I work in a plant that struggles with weld spatter. I find it difficult to justify spending money on new equipment/better consumables because I haven’t determined a good way to measure the improvement.
In the example you mention that spatter was reduced by 85%. How do you measure the reduction in spatter?
In the scenario above the customer went from a globular transfer to spray. Theoretically, a spray transfer has no spatter (it has sparks, but no spatter will stick to the adjacent base material that cannot be wiped off with your glove). However, it in real life you cannot get rid of spatter 100% unless you are tig welding and have perfectly clean material. So 85% is a more realistic number. Steel with light amounts of surface contaminants such as oil, dirt, rust and mill scale will produce spatter. Bad fit up will do this too.
The only true way to measure spatter reduction would be to collect all the spatter that sticks to the piece, this is very difficult and time consuming. The best way is simply to run side by side comparison to show the difference in spatter generation and also keep a tally of how long it takes to grind off the spatter. In this way you are not calculating the reduction in spatter but rather the cost of removing it. This is a more powerful calculation if you are trying to justify new equipment.
Keep in mind that there are plenty of ways to minimize spatter without having to spend money on equipment or better consumables. The free checklist you can download on this post will get you started. Good luck and let us know if you have any follow up questions.
Our shop switched to a 90/8/2% Ar/CO2/O2 tri-mix blend for ER70S-6 a number of years back. There is essentially no spatter when using spray arc settings, and if there is a wire wheel and a little chipping with a file makes simple work of it. No anti-spatter required, just have to make sure there’s as little loose oxide/rust on the material as possible (wire wheel or cup works great).
You’re absolutely right about the labour costs. Funny that welders rarely consider it until they’re in a management position though.
Thanks for the comment Scott. It seems that trimix is working very well for you. Do you feel the addition of oxygen to the traditional Ar/CO2 mixes provides a smoother arc or just provides a flatter bead contour? I like how the 95%Ar/5% Oxygen mix flattens out and runs very smooth, but not a fan of the penetration profile (finger-like profile). Seems like this trimix would give you the best of both worlds (CO2 providing a broader penetration profile and better at dealing with small amounts of contaminants and the oxygen smoothing out the weld and possible reducing the amperage needed to reach spray transfer). Would love to hear if you have compared this trimix to 90/10. Have a great day.
There is still something not right with the numbers:
Before
Labor = 15days x 7welder x8hours = 840 hours @ $45/hr (labor & overhead) = $37,800
After
Labor = 15days x 7welder x8hours = 840 hours @ $45/hr (labor & overhead) = $29,700
Hello Ken. Thank you! You are correct. The second line is wrong. There was a reduction to just shy of 12 days due to much less clean up. The dollar amount was right but the number of days was a typo. We have corrected it above. Really appreciated you spotting that issue.
I won’t argue that by changing the gas you can reduce spatter and create a large savings but…. the numbers don’t match the math. The difference in the math is only $177 during the 3 weeks. Or did I miss something?
Hello Branden, $177 is the different in material costs (gas, wire, grinding wheels, anit-spatter. The difference comes due to reduction on wire needed (due to reducing loss to spatter), fewer grinding wheels and less anti-spatter. The gas is a bit more expensive. However, the real savings come from labor hours. Eliminating nearly 85% of the cleaning reduces man hours dramatically as you can see above. This makes the cost savings $8,277.
Usted afirma que $8.100 del ahorro son solamente de mano de obra en el trabajo?
tengo algunas dudas.
Atte
Ronald Morrison
Ronald, que dudas tiene? Por favor mandeme detalles. Si tenemos algo incorrecto lo queremos corregir.
Gracias.