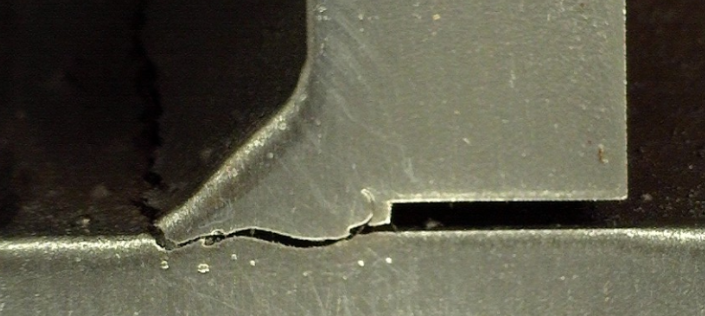
One of the first steps in analyzing cracks to find their root cause and take corrective action is to categorize the cracks. We categorize cracks based on three elements.
- Location
- Direction
- Timing
In today’s article we discuss the importance of crack location when trying to determine what caused it. What follows is an excerpt from Weld Troubleshooting for Non Welding Engineers.
The location of the crack is very important as it can provide a lot of information regarding its root cause. There are many types and names for cracks based on their location. To keep things simple we are mainly concerned with only three areas in which cracks occur: weld metal, heat affected zone and unaffected base metal.

Cracks can be categorized by their location: weld metal, heat affected zone and unaffected (by heat) base metal.
Let’s look at the types of cracks that can occur on each of these zones.
Zone 1: Unaffected Base Metal
Lamellar Cracks – these types of cracks are also called lamellar tearing and occur in the base metal away from the heat affected zone in the unaffected base metal. These cracks occur when the shrinkage stresses are perpendicular to the faces of the plate which have been rolled. It is driven by sulfur inclusions in the base material. In some cases the tear can occur in the HAZ. To prevent this, the amount of sulfur in steel must be kept below 0.005%. Better joint design can also help prevent this issue.
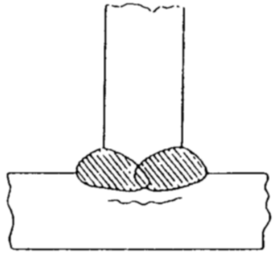
Lamellar tearing or cracking occurs as a result of sulfur inclusion in the base metal and shrinkage stresses introduced by welding.
Zone 2: Heat Affected Zone
Heat Affected Zone Cracks – Cracks in the HAZ can be longitudinal or transverse. Most of the cracks in the HAZ are cold cracks or hydrogen induced cracks. Cracks in this area are typically the result of excess hydrogen, inadequate preheat, inadequate maintenance of interpass temperature, cooling rate that is too fast, highly restrained joints, or a combination of two or more of these factors.
HAZ cracks will be very close to the fusion line but occur in the base metal, not the weld metal. Depending on their location relative to the weld, the cracks are also known as underbead cracks, toe cracks or heat affected zone cracks.
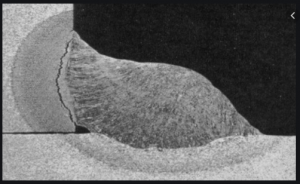
Heat affected zone crack induced by hydrogen. The crack originates at point of high stress as hydrogen diffuses out of the weld and heat affected zone.
When dealing with steel, cracks in the HAZ are typically the result of hydrogen induced cracking. This means that three conditions are present: a sensitive base metal microstructure, a highly restrained joint (a threshold level of restraint) and a source of hydrogen.
SPECIAL ANNOUNCEMENT: Weld Troubleshooting for Non Welding Engineers has been released!
Weld Troubleshooting for Non Welding Engineers goes beyond your typical troubleshooting charts on the back of an owner’s manual. The goal is not just to help you solve a welding problem, but to teach the concepts and theory behind it. Understanding why a recommended solution worked is just as important as solving the problem.
This guide addresses the most common weld discontinuities and defects as well as the most common welding equipment problems.
Reduce your downtime associated with troubleshooting welding defects and welding equipment problems by quickly identifying the causes and implemeting the recommended solutions. This guide will save you money and increase your productivity. Use it as a training tool increase the knowledge level of your welding personnel.
Zone 3: Weld Metal Zone
A large portion of cracks that occur in welding will be in or through the weld metal. Most of these cracks occur when the weld metal is still above 400˚F [205˚C] and are thus called “hot cracks.”
Crater cracks – these cracks occur at the end of a weld where the full cross section of the intended weld is not achieved. A crater is left behind. As the weld metal shrinks there is insufficient weld metal to resist the pulling form the base metal (shrinkage stress) and cracks developed. This problem is very common in aluminum, but can also occur in steel.
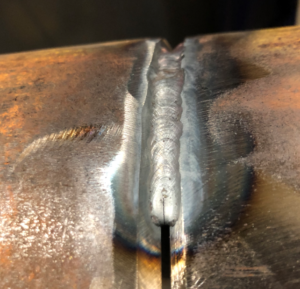
Craters at weld terminations are very common in aluminum, but can also happen in carbon steel as seen in this image.
Centerline Cracks – these cracks occur due to the presence of low melting point elements in the weld metal such as sulfur, lead, phosphorus, zinc and copper. The crack occurs longitudinally along the weld and is also called a solidification crack. To avoid this issue, filler metals with low levels of the above mentioned elements must be used. This problem can also occur due to pick up of these elements from the base metal due to high admixture.
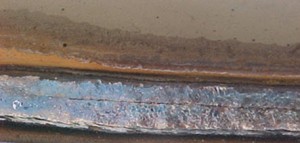
Top view of a centerline crack. Sometimes these cracks are barely visible to the naked eye and thus non-destructive inspection methods like liquid dye penetrant are used.
Throat Cracks – these cracks occur along the throat of a weld. They can be centerline cracks that develop during solidification, but can also occur in service after applied loads cause the weld to fail along its throat. This is a perfect example of the need to know the timing of the crack, the location and the direction. If you have centerline cracking which is longitudinal, and occurs immediately after welding, we know it is due to segregation of low melting point elements. However, if it occurs several days later when the weldment is in service we can start looking at other causes such as overload. Other issues may be welding defects that went undetected such as excessive concavity, lack of root fusion, lack of penetration, etc.
Root Cracks – these cracks originate at the root of the weld. They can manifest themselves as throat cracks or propagate in other directions. They are caused by weld imperfections at the root. Slag inclusions are usually the culprit; however, as is the case with throat cracks, lack of root fusion can also cause root cracks. Figure 3.5-9 shows an example of a root crack.
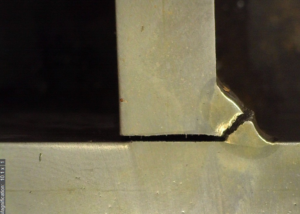
Root cracks originate at the root. They are a type of throat crack as the failure occurs along the throat of the weld.
There are many other names for cracks based on location. The key is to identify where the crack started: in the unaffected base metal, in the heat affected zone or in the weld. Then, combined with the timing and the direction of the crack, you can easily narrow down the possible causes and correct the issue.
REFERENCE: Weld Troubleshooting for Non Welding Engineers
Weld Troubleshooting for Non Welding Engineers goes beyond your typical troubleshooting charts on the back of an owner’s manual. The goal is not just to help you solve a welding problem, but to teach the concepts and theory behind it. Understanding why a recommended solution worked is just as important as solving the problem.
This guide addresses the most common weld discontinuities and defects as well as the most common welding equipment problems.
Reduce your downtime associated with troubleshooting welding defects and welding equipment problems by quickly identifying the causes and implemeting the recommended solutions. This guide will save you money and increase your productivity. Use it as a training tool increase the knowledge level of your welding personnel.