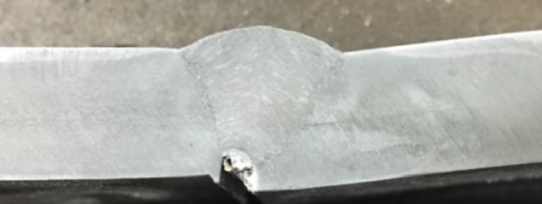
A repair procedure is necessary any time there is a defect in welding that must be corrected. The repair procedure is not just a welding procedure specification, but rather a set of instructions and rules on how to repair different types of defects.
There is no standard format for a repair procedure, or a standard name for that matter. For some it is a Standard Operating Procedure for Weld Repair, for others it is simply Instructions for the Repair of Weld Defects.
The amount of information contained within these repair procedures depends on the fabricator. However, the amount of information is not as important as the quality. Repair procedure should be part of your product and process specifications. As with welding procedure specifications, the value in having a repair procedure is to follow it! If a repair procedure is simply written to comply with a requirement to obtain a contract or a certification, such as ISO:9001 and it is then never looked at, it is essentially a wasted opportunity.
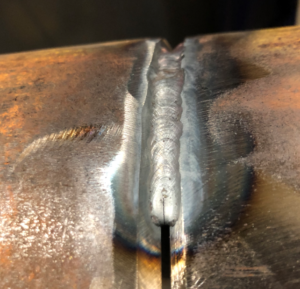
Understanding how to repair welding defects can be accomplished through the implementation of repair procedures.
Repair procedures, if written properly and followed, provide two invaluable benefits to the fabricator.
- It assures that all repairs are done properly in order for the welded structure to meet the acceptance criteria. Through documentation it also allows for learning and avoiding having the same problem in the future.
- It allows welders to make most repairs without the need to wait for a supervisor, quality person or a welding engineer to ascertain the severity of the defect and decide on how to repair it.
Although the goal is to have no defects and therefore no repairs, it is almost a certainty that defects will occur. Having repair procedures will save you time and money. If applied properly, these repair procedures will reduce downtime and help with productivity.
So what should a repair procedure include? Here are the basic building blocks. But remember, the best repair procedure is one that is clear and easy to follow. You should include as much information as you deem necessary.
SPECIAL ANNOUNCEMENT: Weld Troubleshooting for Non Welding Engineers has been released!
Weld Troubleshooting for Non Welding Engineers goes beyond your typical troubleshooting charts on the back of an owner’s manual. The goal is not just to help you solve a welding problem, but to teach the concepts and theory behind it. Understanding why a recommended solution worked is just as important as solving the problem.
This guide addresses the most common weld discontinuities and defects as well as the most common welding equipment problems.
Reduce your downtime associated with troubleshooting welding defects and welding equipment problems by quickly identifying the causes and implemeting the recommended solutions. This guide will save you money and increase your productivity. Use it as a training tool increase the knowledge level of your welding personnel.
A repair procedure should include:
- Scope – this is why the repair procedure exists, what it covers, and who it is for.
- Normative References – these are documents such as welding codes, standards, specifications or other instructions that are mandatory and must be followed, but which are not included within the repair procedure document.
- Definitions – any terms that need to be defined to add clarity to the instructions in the repair procedure. For example, defining “weld discontinuity” and “weld defect” so that users understand the difference.
- Responsibilities – some repairs don’t require engineering approval, such as repairing undercut. Other repairs may require approval from the engineer in charge before they are done. Being clear on this is essential.
- General Procedures – this section contains the meat of the procedure. It details how repairs must be done according to the weld defect.
- Welding Procedure Specifications – the repair procedure must reference the welding procedures that shall be used to make repairs. These procedures may be the same as used in production or may be welding procedures developed specifically for certain repairs.
Is your company currently using repair procedures? Do these procedures allow your welders to quickly repair defects without having to wait for minutes or even hours for an inspector, supervisor or engineer to determine the severity of the issue and how to fix it?
If this is not the case, it is highly recommended that you create your Repair Procedure.
Nice Blog