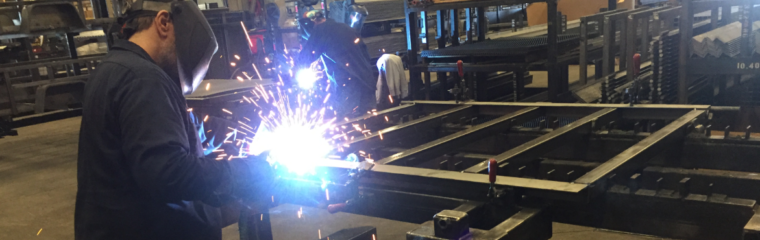
One of the most common questions we get around the topic of welding procedure qualification is regarding the differences between qualified and prequalified welding procedures. The main question is typically: is one better than the other? Before we answer this question, let’s first discuss the need for qualified, or prequalified, welding procedures.
If you have been welding for while you know that you are able to weld two pieces of metal with relative ease. You may get a specific look, whether that is the stacked dime look or simply a flat stringer. Or you may be able to put down a big weld or a small weld. And you can use a wide range of amperage and voltage as well as weld with many different shielding gases. However, all these freedoms we take when welding yield very different results. Quality and cost of manufacturing differ widely.
To start, let’s provide a brief explanation of each…
A Qualified Welding Procedure is one which is proven by testing (destructive and nondestructive). A Prequalified Procedure is one that achieves qualified status without the need for testing as long as a long list of requirements are met.
Qualified Welding Procedures
The purpose of qualifying a welding procedure is to ensure that the procedure is capable of producing sound welds. This is accomplished through a combination of nondestructive and destructive testing. Some of these tests include:
- Visual Inspection
- Tensile tests
- Bend tests
- Fillet break tests
- Macro etch test
Each of these tests have their own acceptance criteria which must be met in order to qualify the welding procedure.
In certain cases additional tests are required, such as hardness tests and toughness tests. The purpose of all these tests, as expressed above, is to assure that the procedure is capable of producing quality welds.
For example, if we want to ensure that the procedure can achieve fusion to root in the case of a fillet weld, a macro etch test is necessary. This test will show a cross section of the weld and we’ll be able to see if the requirement was met. A fillet break test accomplishes the same thing, but does it over a length of 4 to 6 inches rather than a single spot in the test coupon. Fillet break tests are predominately used for welder performance qualification tests, but could be specified for welding procedure qualification as well.
Whether you are looking to qualify or prequalify welding procedures for the welding of Carbon Steel, AWS D1.1 provides all the information you need. Our guide Qualification of Welding Procedures, Welders and Welding Operators was developed to guide the user in navigating all the requirements of AWS D1.1 Structural Welding Code – Steel.
Prequalified Welding Procedures
So, if these tests described above are required to assess whether or not a welding procedure will produce sound welds, how can a prequalified welding procedure be trusted to do the same without any testing?
The answer is: if you follow all the rules, all the requirements and adhere to the limitations imposed by the governing structural welding code it is expected that the welding procedure will produce sound welds. This long list of requirements can be hard to follow and understand for someone that doesn’t work with welding codes and standards, but whoever uses prequalified welding procedures will still have reasonable assurance of the effectiveness of such procedures to deposit quality welds.
For example, AWS D1.1 Structural Welding Code (Steel) permits the use of prequalified welding procedures. The use of prequalified welding procedures can save you a lot of time and money by avoiding costly testing, but you must make sure you follow all the requirements specified in the prequalification clause of this code. Some of the main requirements are:
- Using a prequalified welding process
- Using a prequalified welding joint and adhering to specified tolerances
- Using matching filler metals
- Using proper preheat and interpass temperature
- Using the filler metal manufacturer’s recommended welding parameters
There are many more requirements such as maximum fillet weld sizes in a single pass depending on welding position, minimum root pass thickness, minimum fill pass thickness, etc.
As you can see, restricting all these variables ensures that the user is welding with parameters, with a welding process and using joint details that have been proven time and time again to produce sound welds. Because of this, you are able to bypass testing to reach qualified status.
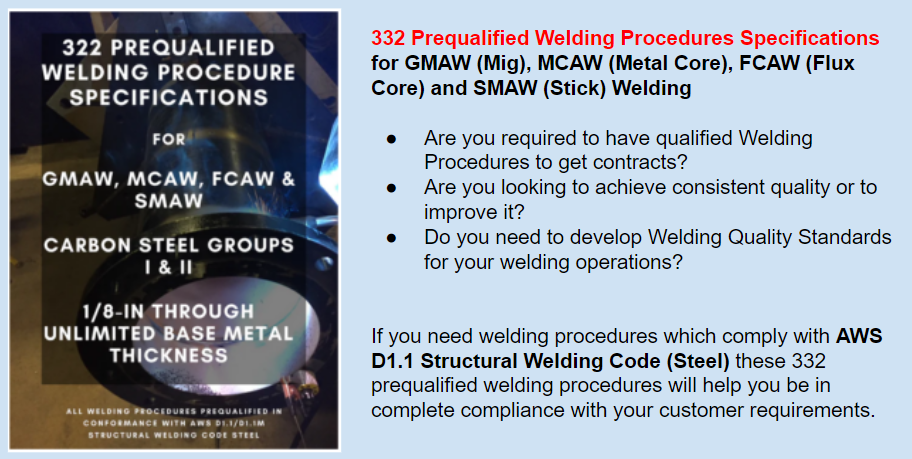
So, which one is better?
As you probably figure out already, it depends. Using prequalified welding procedures can be very advantageous in most structural welding applications. Prequalified welding procedures will save a fabricator a lot of money as they can be developed by a knowledgeable professional in an hour or two rather than spending 2-3 hours to run the weld test and then anywhere between $1,000 to $3,000 for lab testing.
This seems really good right? Quicker and cheaper. But there are a couple of scenarios in which you would opt for qualifying by testing.
- If a prequalified welding procedure is not permitted
- If qualifying by testing allows you to use different parameters and/or joint details which reduce fabrication time and thus becomes more cost effective.
Let’s explain these two scenarios.
The first one is simple. Let’s say you need to weld out of position with the GMAW process. To do this you’ll probably need to run short circuit transfer. This type of transfer mode (GMAW-s) is not permitted for use in prequalified welding procedures. So you must qualify by testing.
Another example would be when using codes that don’t allow prequalification of welding procedures, such as AWS D1.2 Structural Welding Code – Aluminum.
The second scenario is one that is often missed. Although a prequalified welding procedure can save you a lot of time and money upfront, it may be more advantageous to qualify by testing to minimize the amount of welding. For example, a prequalified joint for a CJP V-groove weld will require an included angle of 60 degrees. This is a very wide groove, but it is required because it facilitates root fusion. If you reduce the included angle to 45 degrees you are no longer able to prequalify the procedure, and must qualify by testing. However, this significantly reduces weld volume. So if this is a weld that you make every day you will save money in the long run by taking the time (and expense) to qualify the groove details under a welding procedure.
In conclusion, both qualified and prequalified welding procedures accomplish perhaps the most important thing: quality welds. But consider the cost of each. If you need to have procedures in a hurry to start or get a contract then prequalified procedures are a great option. But consider if making changes to joint details can save you money in the long run to make your final decision.