Welding is a very complicated industrial process with many different variables. Because of this there are an innumerable amount of problems we can experience when we weld. From porosity and spatter to cracked welds, welding problems cost us a lot of money. In some cases welding problems are severe enough to cause significant delays adding to our cost and in some cases even causing us to lose jobs.
Below is a short list of some of the most common welding problems. Would you please do us a favor and leave us a comment letting us know what is your biggest challenge is in welding?
- Spatter
Spatter is sometimes believed to not be a welding discontinuity or welding defect. However, some codes and standards will not allow it outside of the welding zone. More often than not spatter is just a nuisance. We need to clean it up and it adds to costs. If you have spatter it is an indication that something is wrong. That can be your welding procedures (amps, volts, gas, angles, travel speed, etc.), your equipment upkeep, your fit up, your base metal preparation, the skill level of your welders, and many other issues.
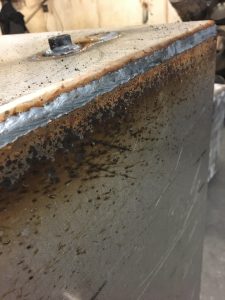
Spatter does not affect the structural integrity of a weld in most cases, but it almost always has to be removed adding to total cost.
- Porosity
Like spatter, porosity is does not affect the integrity of a welded structure significantly. If it becomes excessive it can certainly reduce the effective area of the weld and reduce its strength. For the most part, porosity is an aesthetics issue. No one likes to see holes in their welds. The main reason for getting porosity is lack of shielding gas. However, before you go increase the flow you should be aware that porosity can also be caused by the following.
- Contaminants in the base metal (surface and internal)
- Contaminants in the filler metal
- Moisture in the shielding gas or shielding gas delivery system
- Moisture in the filler metal (stick electrodes, flux-cored wires and fluxes are very susceptible to moisture pick up)f
- Welder skill
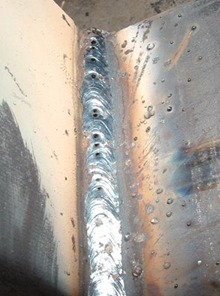
Although porosity is not a major problem affecting structural integrity, it looks bad and must be avoided.
- Undercut
Undercut is a more serious problem that the two above. Undercut is an indentation on the base metal at the toe of weld which creates a stress concentration. Although not as severe as a crack, undercut has extremely low allowances under welding codes, especially in cyclically loaded structures Undercut is typically caused by one or a combination of the following:
- Voltage too high
- Travel speed to fast
- Transverse angle too steep
- Welder skill
Keep in mind that undercut forms a mechanical notch which in turn concentrates stresses. It is a very serious discontinuity that should be addressed immediately.
- Lack of Fusion
When we are unable to get the weld to fuse to the base metal we have lack of fusion. When we weld we want our weld and base metal to become one. When we have lack of fusion we don’t have this and this creates a big problem. Stresses cannot jump gaps, so lack of fusion drastically reduces weld strength. Lack of fusion is usually associated with procedures that don’t provide enough current to penetrate the base material. Other than low amperage lack of fusion can be caused by any of the following:
- Mill scale on the base material
- Welder skills (most commonly having a large contact-tip-to-work-distance (CTTWD) which reduces amperage)
- Excessive travel speed (we see this in vertical down welds)
- Very low travel speeds (when welding to slow we allow the puddle to run ahead of the electrode and we lose penetration)
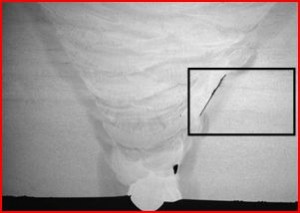
Lack of fusion can be caused by excessive mill scale in the base metal, incorrect welding procedures and welder skill.
- Cracks
Perhaps the most severe of welding discontinuities are cracks. With very few exceptions there is zero tolerance for cracks. Some transverse cracks in hardfacing applications are OK as this is the weld stress relieving itself. Many issues can cause cracks. The first step in troubleshooting cracks is to categorize them. You can do this in one the following three ways.
- By timing: Hot or Cold cracks
- By location (i.e. HAZ, underbead, centerline, toe, etc.)
- By direction (longitudinal or transverse)
After making this identification you will be able to narrow down the potential causes and begin your troubleshooting process and development of corrective action.
In many cases cracks are caused by not paying close attention to welding procedures. Violating preheat and interpass requirements, not following low hydrogen practices and not knowing the base material properties are big issues. You need to know what you are welding before assuming that what works on low carbon steel will work on something else.
As stated above we would love to get a comment from you telling us which is your biggest welding problem. Welding problems are not limited to quality issues as the ones detailed above. They can be related to productivity, or lack thereof. They can be in getting skilled welders. Regardless of what it is we would like to hear it.
This is very helpful. Will follow your site from now on.
can i ask about how to weld seam line and how many distance to attached another joint? Thank you
What is your question? What welding process? Resistance Seam Welding, Gas Metal Arc Welding? Or are you looking for a recommendation of welding process? If so, please let us know what base metal you are welding, dimensions (thickness, length and width) and any other details of this application.
smaw/fcaw process
Good information and first approach thought process suggestions to prevent welding flaws.
Thank you
Thank you TR. I’m glad you found the information helpful.