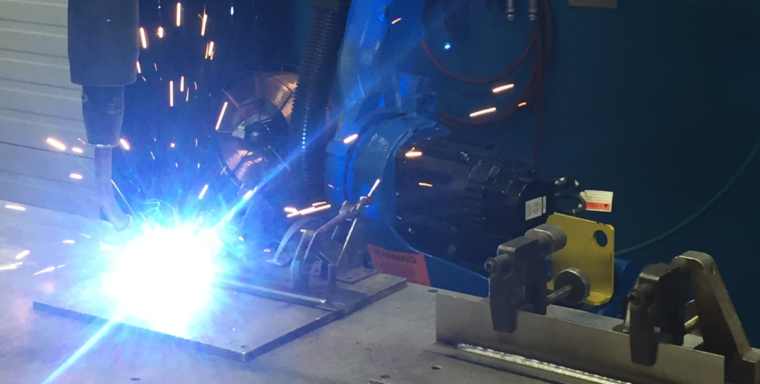
One of the best solutions for welding distortion may seem counterintuitive. Many times, when a fabricator is experiencing distortion from welding, they often believe they are welding too hot. Their initial instinct is to reduce the heat input by lowering the amperage. So, they try it, only to find out the problem persists or even worsens. Then, they might try switching to a smaller electrode, for example, moving from a .045 ER70S-6 GMAW filler to a .035 ER70S-6. But this often doesn’t solve the problem either.
Then, someone might suggest the seemingly crazy idea: switch to a larger diameter electrode, like an .052 ER70S-6, and run it at a higher amperage. Surprisingly, for many, this approach can actually make the distortion problems disappear.
Understanding the Root of the Problem: Weld Size and Heat Input
Distortion is a significant challenge in welding. While numerous factors can contribute to it, the size of the weld is consistently the biggest culprit. However, assuming we are welding to the correct specified size, the next logical step to minimize distortion is to reduce the heat input during the welding process. This is where many fabricators go wrong in their approach.
The common misconception is that “welding colder” – simply reducing amperage – will inherently lead to less distortion. This idea stems from the understanding that lower heat input generally translates to less distortion. However, the crucial misunderstanding lies in how to effectively reduce heat input.
The Heat Input Equation and the Amperage Trap
The formula for heat input in welding takes into account three key variables: amperage, voltage, and travel speed. The critical mistake many make is not realizing the interconnectedness of these variables, particularly the relationship between amperage and deposition rate.
When we choose to reduce the amperage, we are also reducing our deposition rate – the amount of weld metal deposited per unit of time. To achieve the same required weld size with a lower deposition rate, the welder is forced to travel slower along the joint.
Here’s the catch: travel speed is inversely related to heat input. So, while reducing amperage might seem like a step towards lower heat, the necessary decrease in travel speed often negates this reduction, resulting in little to no change in overall heat input. In some cases, traveling significantly slower can even increase the heat input.
The Counterintuitive Solution: Higher Amperage for Less Distortion
The seemingly paradoxical solution to distortion often lies in increasing the amperage significantly. When we increase the amperage, our deposition rate also increases proportionally. To maintain the same specified weld size with this higher deposition rate, we need to travel along the joint much faster.
While adjustments to voltage may occur, they are typically not as drastic as the change in travel speed. The net effect of significantly increasing amperage and consequently travel speed is often a slight decrease in overall heat input.
This approach sounds counterintuitive, but fabricators who understand this principle often achieve greater success in minimizing distortion.
The Ultimate Key: Weld Size
It’s crucial to reiterate that the single biggest contributor to distortion is the size of the weld. If you are experiencing distortion and suspect you might be overwelding, instead of focusing solely on adjusting amperage and travel speed, first consider simply reducing the size of the weld to the minimum required by the specifications. In essence, the bigger the weld the higher the heat input and thus, more distortion.
Reducing the weld size directly translates to a significantly lower heat input and, more importantly, reduces the volume of molten metal that undergoes thermal expansion and contraction during the heating and cooling cycle. This reduction in weld volume directly minimizes the internal stresses that lead to distortion.
In Summary
While the initial instinct to reduce amperage to combat welding distortion is understandable, it often overlooks the crucial interplay between amperage, deposition rate, and travel speed. By understanding the heat input equation and the impact of travel speed, fabricators can sometimes achieve better results by increasing amperage and travel speed. However, the most impactful solution for minimizing distortion often lies in adhering to the specified weld size and avoiding overwelding in the first place.
Reference: Weld Troubleshooting for Non-Welding Engin
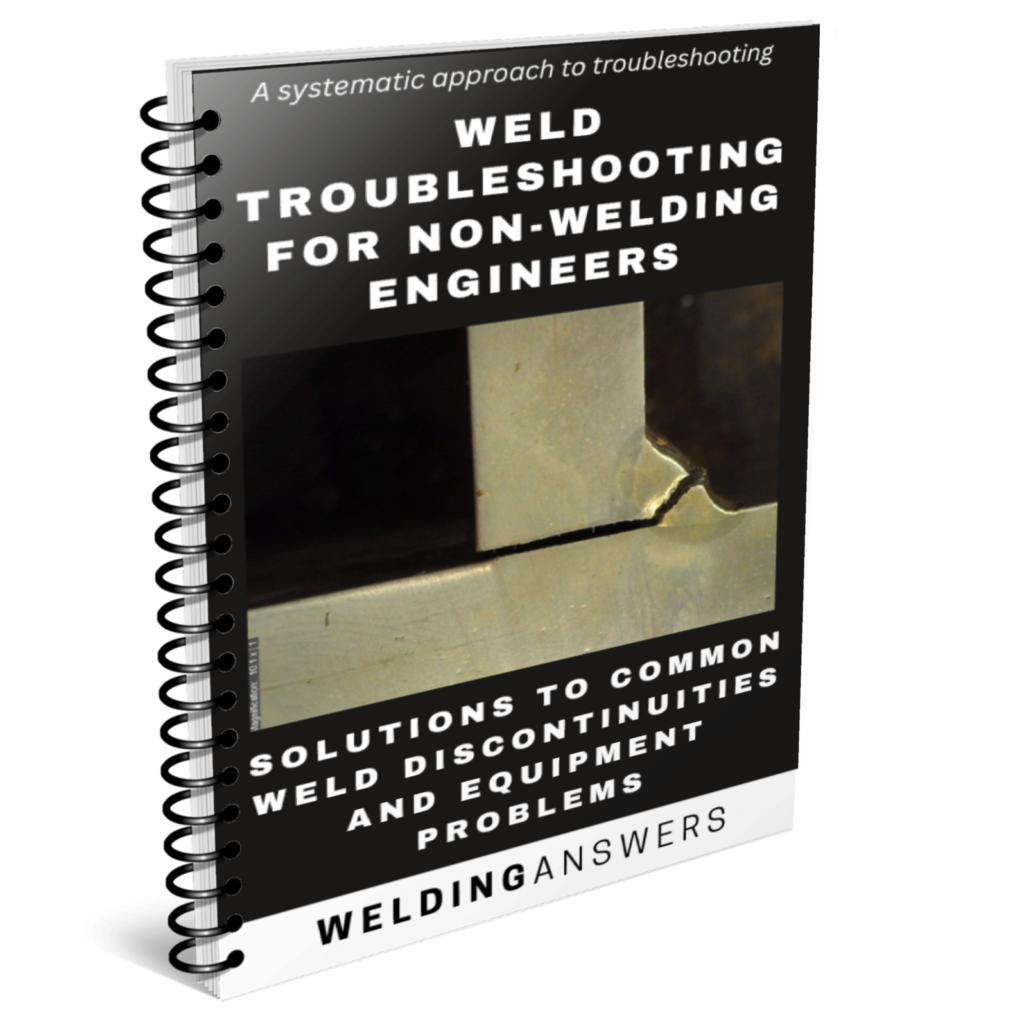
Please note: I reserve the right to delete comments that are offensive or off-topic.