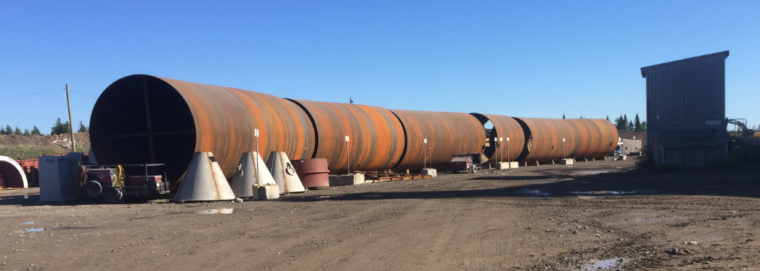
A question we often ask of our customer is “how to do you determine the minimum level of quality for your welded product and how do you verify you are reaching or exceeding that quality level?”
Responses included comments such as:
- We just weld and know our welds will hold because we know our trade
- We drop the part on the floor and if it doesn’t break we ship it
- We perform ultrasonic testing and/or radiographic testing of all weldments to assure quality
- We have a CWI on staff that reviews all welds
- We follow a structural welding code
- We follow our customer’s defined weld quality standards
- We have developed our own standards; in some cases referencing existing codes
The responses we received were all different, but can be grouped into a few methods of assuring quality.
Comments were also made regarding the challenges we face today in order to have adequate quality control. A big challenge is the shortage of skilled welders. This is a worldwide problem. This shortage creates a huge need for training. Training adds costs on the front end, but hopefully provides a good return on investment. But in many cases the struggle then becomes finding a trainer. Can we rely on welding schools and vocational programs to train welders properly? And if we can, can they handle more students without the program’s quality suffering?
Our favorite comment came from one of our readers from Chile. He said “the [hardest part] is to enforce those standards.” This is a challenge we face every day in helping our customers improve their quality standards. You can have a perfectly defined specification for weld quality, but if it cannot be implemented it is totally useless. It is always challenging to adopt new standard, after all, no one likes change. Sometimes the skill level needed from our welders isn’t there. Other times it is equipment that is simply not adequate for the demands. Other times it simply becomes a matter of producing at a high rate to meet customer demand and having quality assurance take a back seat.
The reality is that everyone has a quality standard, whether written or not. In our last post we mentioned the quality standard of a large fabricator we are working with: no porosity and no lack of fusion. It may not be a good quality standard, but it is one.
In our years of experience in helping customers improve quality we have categorized quality standards as follows. Interestingly enough the emails and comments we receive all fall within these:
- No quality standard – nothing is documented and there is no defined way to accept or reject a weld. However, as stated earlier, everyone has a quality standard, even if unwritten or unspoken. After all, if the welds are missing you go back and weld those joints. So there always is a minimum level of quality assurance. The minimum weld standard would be “weld where a weld is needed and make sure the parts stick.”
- Quality based on weld appearance – this is by far the most common weld quality standard. We accept or reject a weld based on how it looks. The biggest problem with this method is that it is subjective. We can tell a few things about a weld from its outward appearance, but without a properly qualified WPS behind it we have no real assurance that the weld is good.
- Quality based on visual inspection – visual inspection by a welding inspector is a means of quality control. This goes beyond considering weld appearance which is mostly subjective. This method is still limited as an inspector is only looking at the outside of the weld. He or she can measure the size of the weld and look for discontinuities such as cracks, undercut and overlap. But the inspector cannot detect lack of fusion, lack of penetration, inclusions and other subsurface discontinuities. This goes back to the comment made earlier, if we don’t know if a sound welding procedure is being used, we cannot be sure the weld is achieving the desired level of quality.
- Quality based on other Nondestructive Testing (NDT) methods – when we can add volumetric inspection to visual inspection we can detect many, if not all of the possible welding defects. There isn’t a single NDT method (visual, radiographic, ultrasonic, leak, dye penetrant, etc.) that can detect all discontinuities. A combination of these must be employed to have 100% assurance that the weld has no discontinuities. This is great, but as you can imagine this can become extremely expensive. The goal would be to institute measures that would decrease the amount of NDT required to assured 100% compliance with the specified quality standards.
- Quality based on structural welding codes – Following structural welding codes such as AWS D1.1, D1.2, D1.6 and others, provides a cost effective method of producing quality welds. The premise here is that you will qualify a welding procedure by testing to prove that it is capable of producing sound welds. You could also use a prequalified welding procedure if allowed by the governing code. The qualified WPS then has to be used by welders who must have a minimum skill level. This minimum skill level is verified by a welder performance qualification test. Once these two items (qualified welding procedures and qualified welders) are in place they need to be complemented with a good weld inspection program. The three components below are the foundation for any weld quality standard provided by structural welding codes:
- Qualified (or Prequalified) Welding Procedure Specifications
- Qualified Welder Performance
- Clearly defined methods of weld inspection
- Internal quality standards – This is the one will possibly require the most work, but also the one that best optimizes quality. This means that it will assure the specified level of quality but not necessarily anything beyond that. It may utilize structural welding codes as the basis for developing quality standards, but includes more stringent requirements where needed. By the same token it will loosen up the requirements of said codes if they are unnecessarily restrictive for the products being manufactured.
We hope that this article gets you to think more about your quality standards. Do they need to be improved? Do you need to have one? Can one lower your costs by reducing rework?
Troubleshooting for Non-Welding Engineers
- Learn and follow the process used by welding engineers to find the root cause of welding problems and their solutions.
- This troubleshooting guide goes beyond your typical troubleshooting charts on the back of an owner’s manual. The goal is not just to help you solve a welding problem, but to teach the concepts and theory behind it. Understanding why a recommended solution worked is just as important as solving the problem.
- This guide addresses the most common weld discontinuities as well as the most common welding equipment problems.
- Use this publication as a training tool for welders, supervisors, inspectors, quality personnel and even seasoned welding engineers.
- Can help Welding Engineers as well. Most welding engineers are in charge of specific product lines, or work for a single company and are limited in terms of their experience troubleshooting welidng problems. They can be experts in a specific welding process and fixing issues related to the type and thickness of materials they deal with on a daily basis. But when a new application comes along that uses a different welding process or a type of material that i
welding TTLM
amazing,,this content and topics are very helpfull for me,,as a welding trainer i was surprice that these company is still looking for more welders,now i will be more active and more streghten to be a good welder trainer thank you and more power..