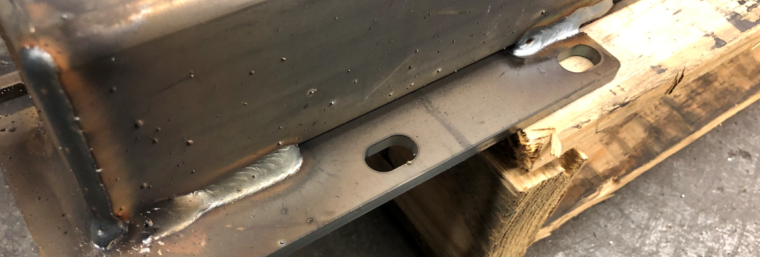
Certain industries that involve welding of their products have very strict quality standards to ensure the production of sound welds. Many others however, do not. They simply weld and unless one of their products fails they don’t pay special attention to welding procedures, detailed inspection of welds or testing the skill (performance) of their welders.
Instituting a quality control program seems to be the right thing to do. After all, there is nothing wrong with improving and verifying quality, right? There are two major problems with this.
- A large portion on fabricators don’t have sufficient knowledge of welding in order to create a quality standard.
- Paying a third party to create this standard can be very costly (upfront cost that is).
We are the first ones to promote the institution of such standards. Welding is our life, we strive to do it right and it is our desire that our customers do as well. So when a customer does not have a quality standard in place for welding we simply suggest that they follow a structural welding code that applies to their work. For example, for someone manufacturing aluminum utility trailers we would suggest following AWS D1.2 Structural Welding Code – Aluminum. There are times that these structural codes are excessively stringent or no stringent enough based on the products they manufacture. In these cases we help them develop their own standards.
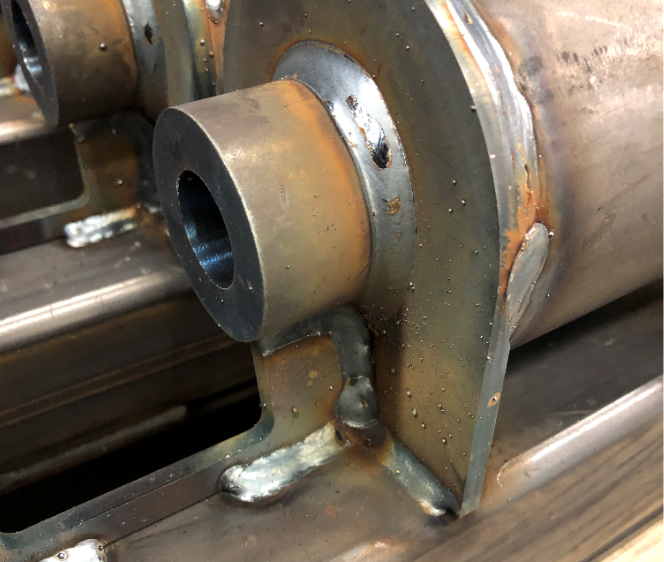
Spatter does not usually constitute a defect and may be acceptable even though it can increase costs (time to clean it). Is spatter acceptable in your products?
It is unfortunate that developing quality standards is often seen as a necessary evil. It is a cost we must incur to meet industry requirements. In some cases it is to show potential customers that we care about quality and have measures in place to ensure it. This results in companies going through the development of quality control standards and missing a great opportunity. We see companies develop standards for quality, develop welding procedure meeting the acceptance criteria of structural welding codes, but miss the opportunity to affect productivity and profitability.
If we can develop our quality standards and at the same time improve productivity and profitability why wouldn’t we? However, sometimes in order to improve quality our costs go up. And the improvements in quality do not show up in the profit and loss statement. No improvements to the company bottom line. And this is what brings us to the question: What is the acceptable level of quality?
We visited a customer yesterday that said their quality standard for welding is simply “no porosity and no lack of fusion.” This is tough since visual inspection can’t detect lack of fusion and they are not doing any other kind of nondestructive testing. Is this an acceptable quality standard? It could be if they could inspect for lack of fusion or have processes in place that make lack of fusion extremely improbable.
Here is where we leave it up to you. We want your opinion. We will take a few of the responses we get and discuss them on our article next week – 6 Levels of Welding Quality Standards. We will NOT display your name or that of your company if we feature your comment.
So if you have time, please tell us in the comments section below how you or your company determines the minimum quality requirements for a weld. Or, if there is no real quality control tell us why. What is preventing the company from instituting welding standards? Is it not needed? Is it too costly? Is there no expertise in this field? In the understanding of structural welding codes? Thanks in advance for your replies.
Kudos for addressing the crucial link between welding quality and standards. Embracing quality uplifts reputation and safety.
Usually the spatter must be removed in the final product. We weld big offshore and wind-power structures here in Shanghai. The requirements from customers became more and more higher-and once the quality required level of product get higher, it never get back to low level. I saw many customer inspectors asked for a perfect apperance of weldings-although it is totally unnecessary.
It makes the cost up! However, the inspector did not care, all he wanted is to make the weld looks better and he did a good job!
The inspector should only be concerned with the weld meeting the acceptance criteria. Spatter can at time be a quality concern. However, even when it’s not if the acceptance criteria says “no spatter” then you cannot have any. Many times spatter does not matter. This is when you need to get the engineer in charge to overrule the inspector.
Our product is in the public eye on a daily basis, so discontinuities (even if they fall within the applicable code) can be unsightly and bring the quality and safety of our product into question, so weld aesthetics became a consideration. We were forced to write a company standard that references the applicable code, but further restricts specific discontinuities. We disallow spatter as it can create an egress point for moisture on our painted weldments that quickly leads to rusting in marine environments.
Thanks for sharing! Many companies should take note of this and use a structural welding code as a standard, but further increase requirements and/or limitations if necessary.
Hi,
in reference to the above article:
1) Most of the times the company has the conctractdue to theyr lower bitting price.
2) Fabbrication cost: grind all the surfaces of the weld area of the mill scale\oxidize area, better quality filler wire\shielding gas etc etc.
Thanks for sharing. Bidding projects certainly becomes a challenging issue. Many companies struggle with enforcing quality due to this. However, in the long run having good quality control reduces costs and helps with the bidding process. Best of luck.