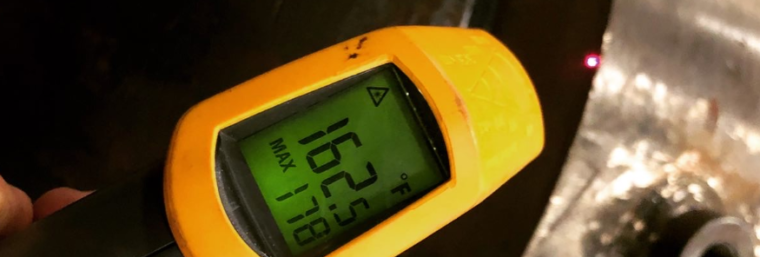
Cracking is a big problem in welding. Many of our customers experience cracking problems on an ongoing basis. Unfortunately, these cracks are not always detected in the shop. Many times cracking occurs once the product is in service. In these cases, cracking can lead to failure and at the very least an upset customer. In more dire cases, the failure may result in significant property damage, injury or even death.
Most cracks in steel weldments are a result of the following:
- Assuming all steels weld and behave the same
- Failure to preheat certain carbon steels
- Selecting the wrong filler metal
- Poor workmanship standards
The good news is that there are a few things you can do to reduce your chances of getting cracks.
To avoid, or at least significantly reduce cracking susceptibility when welding carbon steels, do the following 6 things:
- Know the steel you are welding – many cracks occur because we assume that the welding procedure we used on one steel will work on other steels. The problem is that steels like ASTM A36 weld very similarly to AISI 4140 and other high carbon steels. However, welding 4140 AISI without preheat and with the wrong filler metal will most certainly lead to cracking. High strength steels are more susceptible to hydrogen induced cracking than their low carbon steel counterparts due to their higher hardenability. It is imperative that you know the physical and mechanical properties of the steel you are welding on.
- Use preheat when necessary – as thickness increases, preheating may become necessary, even when welding low carbon steels. The application of preheat is necessary to slow down the cooling rate, which in turn prevents embrittlement of the weld and heat affected zone. Medium to high carbon steels almost always require preheat, regardless of thickness.
- Maintain the required interpass temperature – a common mistake is to apply the proper amount of preheat, but then fail to maintain the required interpass temperature. Believing that the heat produced by the weld will maintain the minimum interpass temperature is a big mistake. Especially in large sections. Some application require the application of heat during the entire welding process.
- Learn how and where to take preheat and interpass temperature readings – when preheat is required, the entire area surrounding the welding joint should be preheated, not just the start. Additionally, the temperature reading should be taken at least 3 inches away from the joint when the thickness of the parts being welded is 3 inches or less. On sections exceeding 3 inches in thickness, the temperature reading must be taken at a distance from the joint equal to the thickness of the members being welded. The same applies to measuring interpass temperature.
- Use low hydrogen practice – adhering to low hydrogen practice eliminates the potential for hydrogen induced cracking. Low hydrogen practice aims at eliminating all sources of hydrogen that may be introduced into the weld by the welding arc. This starts with using a low hydrogen process. Then the selection of a low hydrogen electrode (this is especially important in SMAW and FCAW). In addition to this, properly cleaning all surfaces to be welded is critical. Oil, paint, grease and other hydrocarbons present on the surface of the steel can lead to the introduction of hydrogen into the weld. Proper storage of consumables is also vital.
- Be more scrutinous with cyclic loading applications – structures and weldments that will be subject to cyclic loading should be dealt with even more scrutiny when it comes to inspection and allowance for different weld discontinuities. While certain amounts of undercut may be acceptable for static loading conditions, they may not be for cyclic loading applications. Consult the code or standard that governs your work to understand the requirements.
REFERENCE: Weld Troubleshooting for Non Welding Engineers
Are you tasked with developing, qualifying and approving welding procedures? Are you in need for procedures that adhere to AWS D1.1 Structural Welding Code – Steel? If so, the use of prequalified Welding Procedure Specifications will help you save time and money. It will also help with quality and consistency. Qualification testing for a single welding procedure can cost over $1,000 depending on the necessary tests. Prequalified WPSs are exempt from testing and ready to use.