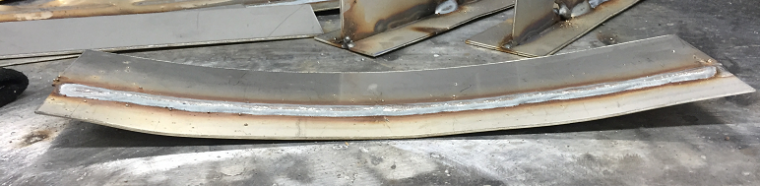
Most types of stainless steels have good weldability and can be welded with all arc welding processes (GMAW, FCAW, GTAW, SMAW and SAW). Stainless is used in many different applications for its strength, abrasion resistance and corrosion resistance. Unfortunately, many assume it can be welded just like carbon steel.
In fact, this is the first and worst mistake that can be made: assuming it will weld (and behave) like carbon steel.
There are many grades of stainless steels which have very different mechanical and chemical properties. Getting a sound understanding of stainless alloys, their properties, how to weld them and how to select the right one for a given application is a science that very few have mastered. This post will not attempt to provide a crash course in welding stainless steels. Instead, we want to focus on 5 of the most common mistakes made when welding stainless steel. Mistakes you should definitely avoid.
Mistake #1: Assuming it welds just like carbon steel.
Stainless steels have very different physical properties than carbon steels. With higher thermal expansion and much lower thermal conductivity than carbon steel, stainless steels have a tendency to distort, warp and create all sorts of fit up issues. If you are welding stainless steel sheet metal for the first time you will definitely struggle with this. For tips on controlling distortions read 7 Ways To Control Distortion and 4 Material Properties That Affect Distortion.

Stainless Steel’s high coefficient of thermal expansion and low thermal conductivity makes it distort easily when welding.
Mistake #2: Using the same tools for both stainless steel and carbon steel.
Stainless steel welding must be completely segregated from carbon steel. Many problems can occur when both are welded in the same stations. For instance, if you use a stainless steel brush on your carbon steel welds and then use it on your stainless welds you will be introducing iron to your stainless weld. This will lead to premature corrosion. It is best to have separate tools.
Mistake #3: Not knowing the type/grade of stainless you are welding on.
There are many grades of stainless, each has its own characteristics and mechanical properties. Some are readily weldable, others are prone to cracking. Using the wrong filler metal can be disastrous. Always know the base material so you can select the right filler metal.
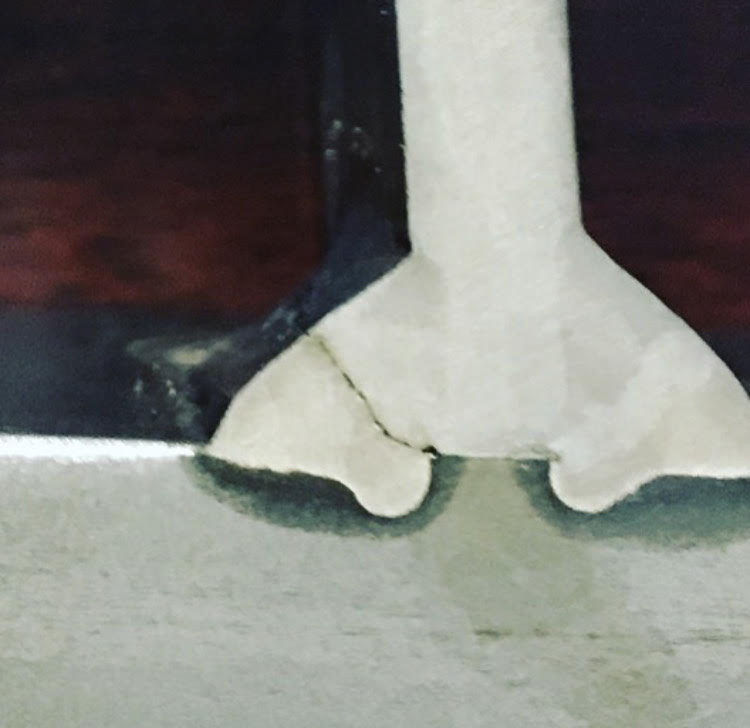
Solidification cracking (hot cracking) is a problem with stainless steel welding. Proper filler metal selection is essential. Seen above: 304 welded to A36 with 308 filler metal.
Mistake #4: Using the shielding gas as used for carbon steel.
Believe it or not this is extremely common. When welding stainless steels we want to make sure we do not exceed a 2-3% content of carbon dioxide and/or oxygen. A lot of shops will use the gas they use for carbon steel (such as 90% argon/10% carbon dioxide when mig welding) on stainless. What hides this problem is that it welds fine, and it looks fine. But that high content of carbon dioxide will lead to premature corrosion. The worst part is that it will pass visual inspection and leave your shop, but you’ll get a call from your customer in just a few weeks or months saying the welds are rusting.
Mistake #5: Welding too hot.
We see this specially with TIG welds. When you weld too hot you are essentially depleting the levels of chromium. Chromium is what provides corrosion resistance, thus you will get premature corrosion if you don’t control your procedures. This is especially true with austenitic stainless steels (think 300 series). Welding with very high input leads to a slow cooling rate which increases the amount of time spent in the sensitization range. This problem sometimes create the need to quench after welding. Fortunately, 300 series stainless steels are not susceptible to embrittlement like carbon steels. When welding stainless try to minimize heat input.
Reference: Metals And How To Weld Them
Welding Procedure Development for Non-Welding Engineers
Are you tasked with creating welding procedures?
Not being a welding engineer is not an excuse for avoiding due diligence. The principles needed to properly develop a welding procedure are clearly explained in this publication. The intent is to provide the knowledge necessary to make the right selection of the many welding variables. It has been written in order for anyone, regardless of level of education, to read and apply it. Welding Procedure Development for Non-Welding Engineers can also be used a troubleshooting guide, as it clearly explains the effects of all welding variables.
Thanks for enrolling me
You’re welcome! We are glad to have you and very happy you’re getting value out of our articles.
Hallo im Shoaib
I need a job. I’m a mig welder!
stick welder
I was told Clamps, Heat Sink, turn up the gas, turn down the heat, and don’t try to repair what should be replaced unless you can afford to buy them a new one.
I found a crack that went all across the weld (GTAW) of a stainless steel pipe. I turned out that the welder used the wrong electrode. Will this always be the result of welding stainles steel with the wrong electrode?
Not always, but it certainly is a possibility. In some cases it is the presence of sulfur and phosphorus (and other low melting elements) that solidify last and towards the middle the of the weld nugget. These elements penetrate grain boundaries in the weld and Heat Affected Zone as as the weld cools they cause cracking due to shrinkage stresses. You must use filler metals that provide a ferrite number (FN) of at least 4 to prevent hot cracking. What you seek to achieve is to adjust the composition of the base and filler metals to end up with a microstructure with a small amount of ferrite in the austenite matrix.
We are going to PQR for 4145 to 4140, groove weld pipe , 4145 to a36 plate 4140 to a36 plate.
its PWHT Required or not after the welding test coupon. please advise.
31.3 not required
When performing the Procedure Qualification Record you should use preheat and PWHT if that is what the base material needs. In this case you do need to preheat and PWHT according to what you expect to run in production. Remember that the qualification process is making sure that what will be done in production works, so your WPS must be based on the procedure used for your PQR. 4140 and 4145 typically don’t require PWHT other than simply slow cooling, but this may depend on the final properties you want out of your welded material.
The Procedure Handbook for Arc Welding suggests using a preheat of 400-500F for thickness up to 1/2 inch and 600-700F for thickness of 1/2 inch to 2 inches.
If this weld requires multiple passes make sure your interpass temperature is the same (minimum) as your preheat.