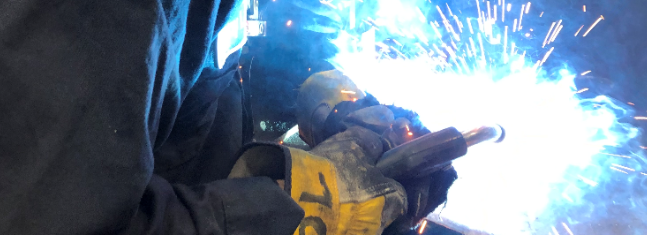
Selecting the best welding process is a critical step in developing a welding procedure that attains the desired quality and optimizes productivity. Many times we look for the welding process that can give us the highest deposition rate to optimize productivity. However, every welding process has limitations. For example, submerged arc welding (SAW) has extremely high deposition rates, but it is limited to the flat and horizontal positions, it is not feasible for short welds and it requires the use of flux which adds complexity to the process. So it may not always be the best option.
The following is an excerpt from WELDING PROCEDURE DEVELOPMENT FOR NON WELDING ENGINEERS
Here are 7 of the most important factors to consider when selecting the best process. These are not listed in any particular order.
1. What equipment is available?
In the vast majority of cases the determinant factor in selecting a welding process is the equipment that the fabricator has available. This makes perfect sense, but you must always consider other processes. There are times when purchasing new welding equipment can lower the total cost of the project by increasing productivity and quality (less rework).
2. What joint types and welding positions will be seen in production?
There are 5 types of joints: Tee, butt, corner, edge and lap. Certain joint types lend themselves better to certain processes. For example, SAW can be used in butt and tee joints, but not really feasible for most edge, lap and corner joints.
The welding position (flat, horizontal, overhead or vertical) further narrows down the processes which may be used. If you have a butt joint that is in the vertical position it would render SAW useless. All other processes are still options, but then you can look at deposition rates for out of position welding. Typically, processes that produce slag (FCAW and SMAW) are good options for out-of-position welding. GMAW and GTAW may be used but they would most likely result in lower deposition rates.
3. Will welding be done indoors or outdoors?
Whether welding is being carried out indoors or outdoors may also dictate which welding process we use. Any process may be used outdoors provided proper shielding from the elements is provided; however, this isn’t always practical.
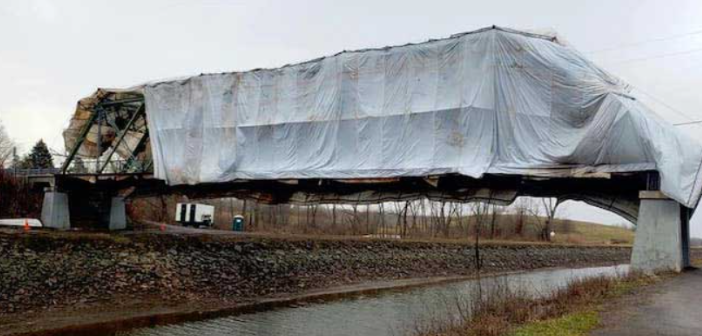
The Albion Canal bridge is seen here covered by a huge canvas in order to undergo construction. These canvases allow for the use of gas-shielded welding processes as they block the wind. In the winter months in cold climates these covers also permit the use of heat in order to maintain an ambient temperature in the vicinity of the weld which would still permit welding.
The best processes for welding outdoors are stick (SMAW) and self-shielded flux-cored (FCAW-S). These processes can handle winds of up to 35 mph [56 kph] without experiencing negative effects. If you need to use GMAW, FCAW-G or GTAW outdoors you would need to have barriers that block the wind as shown above in Figure 2.3. Even a 5 mph [8 kph] draft is enough to cause porosity by blowing the shielding gas away when using gas-shielded welding processes.
4. What is the skill level of the welders?
The skill level of the welders is another important factor. Certain processes such as GTAW and SMAW require a higher level of welder skill as compared to the GMAW and FCAW. SAW is done automatically in which case the welder skill may not be overly important as this person is a machine operator rather than a welder. Furthermore, all processes can be automated by the use of robots or hard automation. In this case, welder skill is not as critical of a factor.
5. What are the Quality and Acceptance Criteria?
Certain processes are better than others at obtaining certain levels of quality. If products need to be x-rayed it may be more beneficial to use a process without slag. However, x-ray quality welds may be attained with all processes. The joint type comes into play here as well. For example, in a 45-degree included angle for a groove weld butt joint SAW may be a great option. If the bevel is then decreased to 25-degrees SAW, or other slag-producing welding processes may generate slag inclusions. In this case you may want to consider a process that does not produce slag, such as GMAW.
Some welding processes may achieve deeper penetration than others. In some cases this is important since certain welds may require a specific amount of penetration. Processes that provide deeper penetration may reduce costs by not having much joint preparation, such as beveling, in order to achieve the desired results. They may also allow the user to reduce the root opening which in turn would reduce weld volume.
6. What are the productivity requirements?
Productivity is one of the most important factors which must be considered when developing a WPS. The deposition rate of the different arc welding process should be taken into consideration. But keep in mind that welding speed alone is not all you need to take into account. Processes that produce slag require clean up and also have a lower electrode efficiency as is the case with FCAW and SMAW.
Below are typical deposition rates of arc welding processes. These ranges are what’s considered practical. We could certainly deposit 20 lb/hr with the GMAW process but it would not be practical.
GTAW → 0.5 to 4 lb/hr
SMAW → 1.0 to 7.0 lb/hr
FCAW-SS → 4.0 to 12 lb/hr
FCAW-GS → 4.0 to 15 lb/hr
GMAW → 2.5 to 15 lb/hr
MCAW → 4.0 to 15 lb/hr
SAW → 12 to 35 lb/hr
7. Is there a return on investment (ROI) target?
Once we understand the productivity factors of each process we can run a return on investment calculation. This can include the purchase of new equipment. If we determine that SAW is the most productive process we may consider buying the equipment if we don’t already have it. A SAW system can run between $20,000 and $80,000. You will need to determine if the investment has a rate of return that is acceptable to your company.
REFERENCE:
Welding Procedure Development for Non Welding Engineers