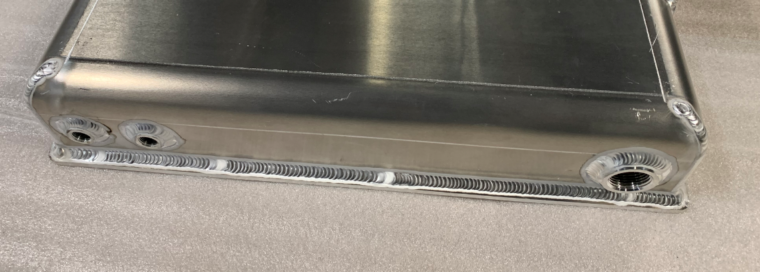
Welding aluminum and aluminum alloys does not need to be complicated. However, to successfully weld this metal there are a few things you need to know. First, you need to know how the properties of aluminum affect its weldability. There are four key characteristics of aluminum that make it quite different from carbon steel or stainless steel. These are:
- High thermal conductivity
- High solidification shrinkage
- High hydrogen solubility
- Oxide coating
These are further explained in Characteristics of Aluminum that Affect Weldability.
6061-T6 is one of the most common aluminum alloys. It is readily available and has excellent weldability. Its manufacturing process involves a solution heat treatment, followed by water quench and finally artificial aging to give it its end product characteristics.
Many mistakes can be made when welding 6061-T6 and other aluminum alloys, but below are 4 of the most common mistakes. Each of these mistakes is associated with one of the characteristics of aluminum described above.
Mistake 1: Welding with a procedure that does not provide enough heat input to achieve proper fusion. Due to its high thermal conductivity, aluminum dissipates heat extremely fast. This will often create “cold” starts, especially with the GMAW process, resulting in lack of fusion and unacceptable bead profile. Aluminum is best welded hot and fast. Some advanced equipment provides the option of a hot start. Take advantage of this if available.
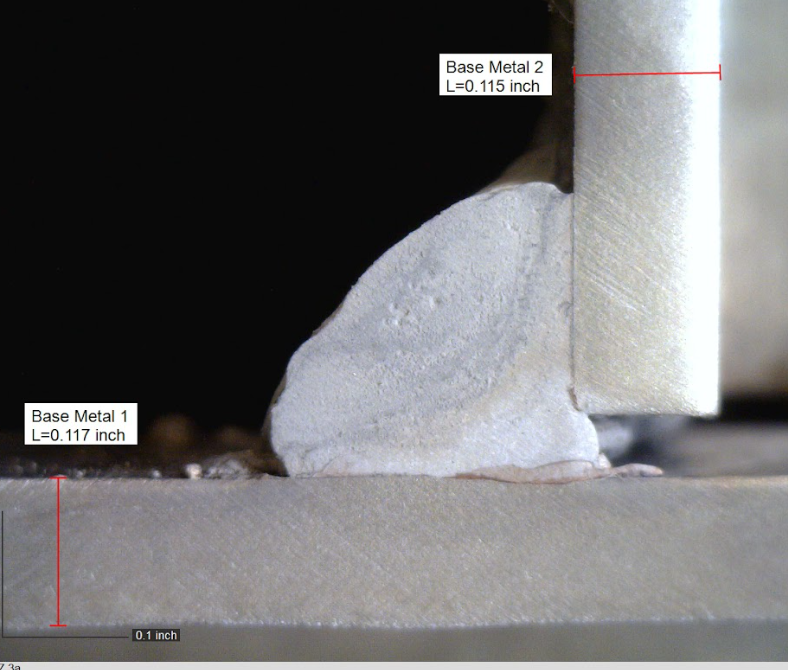
Cross section of a weld start on 6061-T6 aluminum showing lack of fusion. This weld was made at low amperage.
Mistake 2: Improper arc ending. Aluminum exhibits high solidification shrinkage. This creates a problem called “crater cracks.”. These cracks originate due to insufficient weld metal at the end of the weld creating a crater. An easy way to correct this issue is to use a backstep technique. When you get to the end of the weld simply weld in the opposite direction for ½ to 1 inch. Advanced equipment may have a crater fill option. This option consists of setting a specific welding procedure (wire feed speed and volts) for a specified amount of time. The crater procedure activates when the welder gets to the end of the weld and releases the trigger. The key with the crater fill option is that the welder must keep the welding gun at the weld termination, almost as if he or she was maintaining shielding gas coverage. This will allow the feeder to keep feeding wire at a reduced amperage/wire feed speed and fill the crater.
Mistake 3: Not paying attention to moisture. Aluminum has extremely high hydrogen solubility. This means that it will absorb hydrogen while in the molten state much more than carbon steel. To avoid porosity make sure there are no sources of hydrogen (moisture). This means cleaning the base aluminum properly, ensuring shielding gas lines do not contain moisture, ensuring there is no condensation on the filler metal, etc.
Mistake 4: Not removing the oxide layer. Aluminum forms an oxide layer as it comes into contact with the atmosphere. This aluminum oxide layer is very tenacious and provides excellent corrosion resistance. However, it negatively affects weldability. The welding arc will not always remove this layer and it can result in aluminum oxide inclusions and lack of fusion. It is important to properly prepare the base aluminum prior to welding. Follow this three steps to insure proper base metal preparation:
- Remove all moisture sources
- Degrease the base metal
- Mechanically remove the oxide layer
There are many more mistakes made in the welding of 6061-T6 and other aluminum alloys. However, the above four seem to account for the vast majority of weld discontinuities and defects.
Please note: I reserve the right to delete comments that are offensive or off-topic.