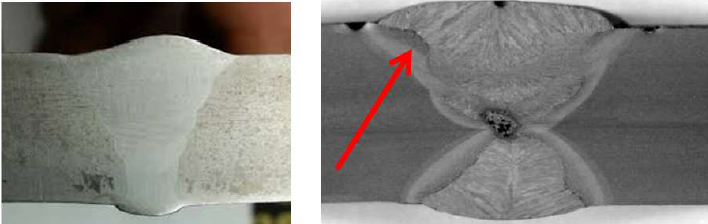
Quality and cost go hand in hand, or at least they should. Poor quality may be cheap during the fabricating process, but very costly when it comes to warranty repairs and potentially losing customers. Many of the companies we work with have seen substantial cost reductions when we help them address quality concerns. For the past many years we have not been in a situation where our customers’ manufacturing costs increased in order to improve quality.
Granted, there are times that costs will increase, but that tends to happen with quick fixes that disregard productivity. For example: a fabricator is having defects associated with poor bead appearance in out-of-position welds and chooses to replace their solid wire (ER70S-6) with flux-cored wire (E71T-1) which is much easier to run. This is a great idea and in fact one that should reduce costs. Better bead appearance yields higher acceptance rates. However, if the developed welding procedures lower the effective deposition rate compared to what was being attained with solid wire, welding productivity will go down. Not to mention the added cost of having to clean the slag produced by the flux-cored wire. On top of that, flux-cored wires are generally more costly than solid wires.
The above is a situation in which improving quality may end up costing more; however, this does not need to be the case. Let’s discuss 3 key areas of welding operations that can have a significant impact on both quality and productivity, but which are not always considered, especially in general fabrication shops (job shops).
- Lack of Quality Standards
- Lack of Welding Procedures
- Lack of Welder Training
Lack of Quality Standards
In our article that discusses the 6 Levels of Quality Standards we state that having no quality standards is in fact a quality standard. Just not a very good one. Many job shops see so much variety that the idea of having a quality standard seems daunting. The reality is that quality standards, regardless of materials to be welded, are not difficult to create. Implementing them may be more difficult, but will yield great results.
Consider the most widely used welding code: AWS D1.1 Structural Welding Code – Steel. This code is in fact a quality standard. So, for a shop that predominantly welds steel products this can be a great starting point. Or even THE quality standard for the shop. Having a clearly defined quality standard will reduce rework and increase productivity and profitability. Unfortunately, many fabricators see implementing a quality standard such as AWS D1.1 as restrictive and very costly.
Many shops will follow a specific welding code and comply with its quality requirements for specific jobs. Yet, they will not follow any quality standards for other jobs. If their customer requires it they will use the code or standard, but if not they won’t. And even when quality problems are prominent in these “non-code” jobs, they continue to operate as is. This may seem insane, but it happens all too often.
Lack of Welding Procedures
Welding procedures are one of the basic building blocks of a welding quality standard. These are the documents that tell the welder what parameters to run, provide information on proper technique, torch angles, travel speed and machine settings. They provide instructions on proper preheat and post weld heat treatment if necessary. They clearly specify the wire type, diameter and the appropriate shielding gas or flux. When welding procedures are used they bring about consistency in both quality and productivity.
Many welders like the settings they are used to and when given a new welding procedure they choose not to follow it because it is “too cold”, or “too hot”, or “it generates too much spatter” and many more reasons. The fact is no one likes change. The key is to not just develop a better welding procedure but to manage the change. Companies that have gone from not using welding procedures to requiring their use in production have seen incredibles gains in productivity and quality. But it does require a bit of work to implement. Company culture is very important.
Lack of Welder Training
Finding time for training shop personnel is difficult. Everyone is always busy and taking welders or other production personnel off the floor can be very costly. But more costly can be the amount of rework associated with low levels of skill. It’s a bit of a catch 22. However, training of welders is so important that many fabricators are willing to pay overtime for welders to stay and participate in training programs. Others simply plan adequately and build up work-in-process inventory and finished goods inventory to compensate for loss of production time due to training.
When we think about implementing quality standards and welding procedures we must also be thinking about welder training. This is not training welders how to weld (although that may be necessary in some cases), it means training them on the reasons behind the implementation of quality standards and welding procedures.
Training that yields great savings are those that reduce downtime. One of the biggest time wasters in welding shops is downtime associated with “faulty” equipment. Having welders that understand how welding power sources and wire feeders work, how to do proper preventive maintenance and how to identify what equipment issues can cause different weld discontinuities is vital. Welders that have a clear understanding of the effects of welding variables such as amperage, voltage, travel speed, contact tip to work distance, gas flow rate and many more are the ones that are better able to troubleshoot welding problems quickly and get back to production.
There are many other factors that can impact quality and productivity, but the above three are the main ones we find missing from most general fabricating shops.
References