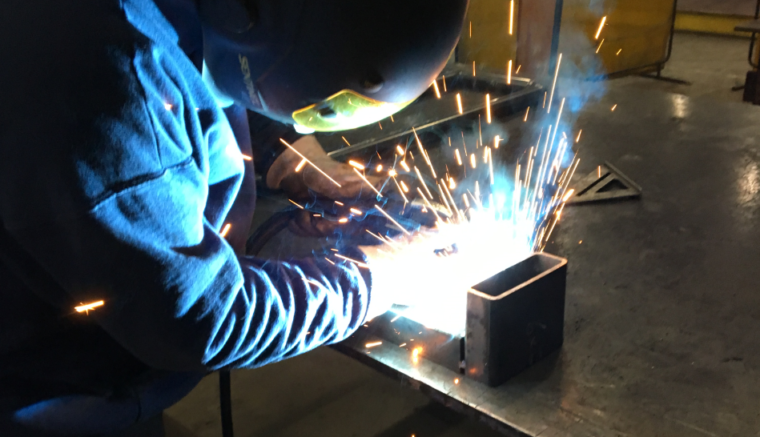
- Provide adequate fixtures – set up time (fitting/tacking) can sometimes take over 50% of the time spent by a welder. Many welders that do repetitive work end up creating their own fixtures to make common weld joints easier and faster to weld. It is typical that when a fabricator buys a robot, fixturing becomes very important and a great deal of money is spend in this area. They get great tooling so that the robot can spend time doing what they pay for, welding. It only makes sense that we should to this for our manual welders as well.
- Keep equipment in good repair – faulty equipment, even equipment that only has “hiccups” from time to time can create a lot of problems that cause the welder to stop welding. Maintenance problems can significantly reduce welder efficiency. Voltage drops due to undersized cables, loose connections or frayed cables may produce large amounts of spatter which require grinding time. These issues can also cause an erratic arc which decreases the life of contact tips, diffusers and nozzles. Increasing changeover occurences of these parts takes away from welding time. Keep equipment in good repair and see efficiencies increase.
- Develop welding procedures – providing your welders with adequate instructions on what parameters to use on different joints and material types is essential. Even the best welders will spend a lot of time fine tuning a procedure when parts, thicknesses of positions change. A written welding procedure allows the welder to set his or her machine based on the values set on the welding procedure specification and go, thus eliminating time with trial and error.
- Train your welders and welding operators – it is important for welders and welding operators (operators of robots and fixed automation) to understand what effect the many welding variables have on the weldment. An effective welder training program is an absolute necessity in any fabricating shop. By knowing what happens if you increase or decrease amperage, voltage, travel speed, travel and work angles, contact tip to work distance (in GMAW and FCAW), welders can more easily and quickly troubleshoot bad welds, make the necessary adjustments and get back to welding.
- Consider the quality of your materials and evaluate alternatives – there is a reason why some fabricators will pay a premium for certain consumables. There are certain applications that cannot tolerate any kind of variability such as wire flip or changes in wire diameter which affect feedability and weld current. A wire that may be OK for welding dumpsters may not be adequate for high-speed robotic welding. If your welders or your robots are having issues with wire tangling, clogging liners excessively, missing the joint (robots) and excessive tip usage consider evaluating alternative consumables. This concept is also true for other inputs such as welding guns, contact tips, nozzles, etc.
- Improve your fit-up – when parts don’t fit well the assumption is that the welder will fix it. He or she can simply add more weld metal and everything will be great. This is only partly true. While welders can definitely make some magic happen, this problem can cause significant increases in cost due to reduced efficiencies. It also may cause a violation of welding procedures if the joint tolerances are exceeded. To get a glimpse at how much bad fit-up can cost you read The Outrageous Cost of Poor Fit Up.
- Consider a different welding process – Are you using a welding process that produces slag such as SMAW (stick) or FCAW (flux-core)? Is it really necessary? We visit many facilities that use flux-cored wire because that’s what they have always used. Or becasue they do some out-of-position welding and don’t want to mess with having different wires to do their flat welds which in many cases comprise over 80% of their total welding. Electrode efficiencies of slag producing processes such as SMAW and FCAW are low compared to solid electrodes used in the GMAW process. On top of that you have slag clean up which adds a lot of time.
- Consider the use of manipulating equipment – This may be what allows you to get rid of slag producing welding processes used for welding out-of-position. If you can weld in the flat and horizontal positions then you can get by with using GMAW exclusively. A manipulator can costs thousands of dollars, but the increase in productivity may pay for the investment in a relatively short amout of time.
Are you looking to qualify welding procedure and/or welders? Are you using AWS D1.1 Structural Welding Code -Steel as your quality standard? “Qualifying Welding Procedures, Welders and Welding Operators” is a guide developed to help you perform your own qualifications in full compliance to AWS D1.1 Structural Welding Code. It provides step-by-step instructions on how to qualify welders and welding procedures. It also provide step-by-step instruction on the proper use of prequalified welding procedures.
Are you in need of AWS D1.1 prequalified welding procedures? This collection provides welding procedures for several arc welding processes. These procedure cover 14 of the most common welding joints, all positions and the most common wire diameters for each process.
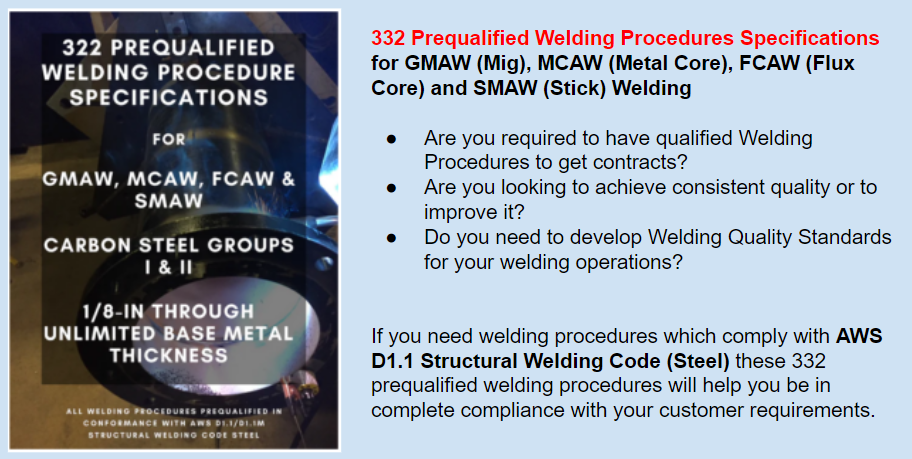
I like that you said that if you keep your welding equipment in good repair you will see efficiencies increase. I think it would be smart to know of a good welding repair company that could help you make sure that everything in your workshop was working the way it was supposed too. I think that would also be a good idea because it would probably keep you safer too.
You are correct. Unfortunately many fabricators do not tend to their equipment until it is too late. Something as simple as blowing out the machine with compressed air once a week can help keep grinding dust and welding fumes out of the machines. When machines get covered in these they overheat quicker as the grinding dust and any other airborne particulate that has attached to the insides of the machine will act as an insulator.
I like how you suggested keeping welding equipment in good repair. My dad is a welder and is always looking for ways to increase efficiency. Thanks for the tips on increasing welder efficiency.
What is mig welding speed to make 4mm weld bead
This will depend of the diameter of the wire and how fast you want to make the 4mm weld. Also, is the weld a fillet? or a groove weld? The volume of weld metal needed will determine your travel speed at a specific wire feed speed. What diameter of wire are you running?
thank you for the post and very interesting facts