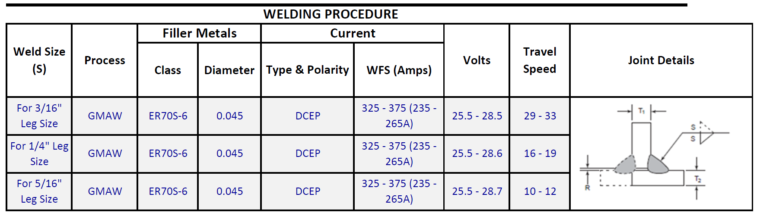
When writing a welding procedure one of the most critical steps is selecting our welding parameters. This means determining the appropriate amperage and voltage as well as other critical aspects that the welder must adhere to such as travel speed and travel and work (transverse) angles.
What follows is an explanation as to the importance of each of these. This is an exerpt from our guide: Welding Procedure Development for Non-Welding Engineers.
Amperage (Current)
Amperage, or welding current, is one of the most important variables in a welding procedure specification. Regardless of the welding process, amperage has a direct impact on penetration. The higher the amperage the deeper the penetration. See Figure 13.4 below.
Figure 13.4 – All three welds were made with the GMAW process using .045” ER70S-6 and 90Ar/10CO2 shielding gas. The only difference was the amperage.
As seen above, as the current (amperage) goes up penetration increases. In GMAW and other wire processes amperage is increased by increasing wire feed speed. When we increase wire feed speed, the deposition rate increases and thus the travel speed must be proportionally increased to maintain the same weld size.
In constant current processes such as SMAW and GTAW we set amperage on the welding machine. In wire processes such as GMAW, FCAW-G, FCAW-S and MCAW we set wire feed speed. Wire feed speed is directly correlated to amperage. The higher the wire feed speed the higher the amperage.
Amperage may also have a significant effect on productivity. As amperage goes up so does our deposition rate as stated above. So the more amperage the more pounds per hour we deposit. As long as we maintain the same weld size, our travel speed will increase, meaning we can weld more linear feet in the same amount of time.
Voltage
Voltage, when set in the correct range, has little effect on penetration. Within this range, the higher the voltage the lower the penetration. Higher voltage spreads the arc out and deposits a wider bead. Less energy density is exhibited as the voltage goes up, so penetration decreases. Keep in mind that if the voltage is too low and you get an erratic arc you will start losing penetration.
Figure 13.5 – These welds were all made with .045” ER70S-6 wire, 90% Argon/10% Carbon Dioxide shielding gas at 375ipm wire feed speed. The only difference was the voltage.
As you can see, voltage has little effect on depth of penetration. However, it significantly affects bead shape and penetration profile. When voltage is set low you will start getting excessive reinforcement in the weld. Reinforcement doesn’t add strength to the weld and may result in increased costs due to additional filler metal required, as well as additional time to make the weld. If reinforcement gets excessive the weld may fail the acceptance criteria of many codes, especially if the weld will be subjected to fatigue loading.
When voltage is set too high the weld puddle becomes very fluid and the weld may sag as can be seen in Figure 13.5 (C). When voltage is excessively high you can also get undercut. When undercut exceeds a certain depth it becomes a defect which must be repaired.
Figure 13.6– Excessive voltage may cause undercut as seen in this weld. The arc energy melts the base material but there is not enough filler metal to fill that void which then results in undercut. Undercut is dangerous as it can significantly reduce the fatigue life of a welded connection.
In constant current welding processes such as SMAW and GTAW the voltage varies based on the welder’s arc length.
Travel Speed
Travel speed impacts more than just productivity. It is a variable which must be stated in the WPS and must be followed. Most welders don’t really look at the WPS for a travel speed. They are just used to the muscle movements required to make a weld of the right size. And here is where some problems may occur.
Travel speed has an effect on many aspects of a weld. If all other variables are held constant (i.e. amps, volts, wire feed speed, shielding gas, etc.) you can expect what is shown in Figure 13.7 below.
Figure 13.7 – These welds were all made with the same welding parameters with the exception of travel speed.
Travel speed will affect the following:
- Weld size – as travel speed increases weld size will decrease. Conversely, as travel speed decreases weld size increases. This can be seen on Figure 13.7 above.
- Heat input – as travel speed increases, heat input decreases as long as the amperage and voltage don’t change and vice versa. Heat input is a critical variable which is affected by amperage, voltage and travel speed.
- Penetration – within the acceptable range allowed by the WPS, increasing travel speed will slightly decrease penetration. However,if the WPS was properly qualified, the range of travel speed shown in the WPS should be adequate to achieve root and side wall fusion within that entire set of values. If travel speed gets excessively slow there is a chance that the puddle may run ahead of the arc and penetration will decrease or even result in lack of fusion. Figure 13.7 shows how the slower travel speed (C) yielded lack of root fusion.
- Quality – naturally, if we have lack of fusion quality will be impacted. Travel speeds which are too fast can also produce other weld discontinuities such as undercut. Undercut may be caused by excessive voltage, not enough wire feed speed or a travel speed that is too fast.
- Productivity – the faster we weld the faster we get done, it is that simple. However, keep in mind that if we have a specific weld size we must achieve then in order to get that size of weld we must also increase our deposition rate by increasing wire feed speed in wire processes or amperage in constant current processes such as SMAW and GTAW.
Travel Angle
Travel angle refers to whether you push or pull (drag). There are certain processes and applications where one is more advantageous than the other. In processes that produce slag, it is advisable to have a pull/drag technique. Pushing these types of processes may result in slag inclusions similar to the one seen below.
Figure 13.8 – Slag inclusion preventing root fusion. This weld was made in the vertical (3F) position with downward progression. It was made with a pull/drag angle which is advisable. However, the puddle ran ahead of the arc and penetration was lost. This is similar to what happens when we push a flux-cored wire and allow the puddle to run ahead of the arc.
GMAW and MCAW are not slag-producing processes so slag inclusions are not a concern. In these welding processes pushing or pulling is acceptable as long as the angles are not excessively steep. A push or pull angle of about 10 – 15 degrees is acceptable.
There are subtle differences between pushing and pulling in GMAW and MCAW. Pushing provides a flatter weld face while pulling produces a bit of a crown. Pulling, however, achieves slightly deeper penetration than pushing. As just mentioned, the differences are very slight and the technique should not be chosen based on the amount of penetration required.
Transverse Angle
The transverse angle in a fillet weld or lap weld should be 45 degrees. There are times when favoring one of the two members being joined may be beneficial, but in general we always want to hit both sides equally even when welding different thicknesses.
The image below shows welding of significantly different thicknesses. The transverse angle was 45-degrees. A properly written WPS should not have the need to favor the thicker section in order to get adequate penetration into both members.
Figure 13.9 – Fillet weld joining ½” to ¼” ASTM A572 Gr 50 material. The transverse angle was 45 degrees.
Figure 13.10 shows the effects of changing the transverse angle.
Figure 13.10 – Effects of transverse angle. (A) has a steep angle favoring the bottom plate, (B) has a transverse angle of 45 degrees, (C) has a transverse angle favoring the vertical plate.
Contact Tip to Work Distance (CTTWD)
If you look at any of the structural welding codes you’ll notice that contact-tip-to-work-distance (CTTWD) is a variable which must be listed in welding procedure specifications. However, it is not an essential variable, meaning that changes to CTTWD of any amount do not require requalification. This can seem puzzling to some, especially those that understand how critical CTTWD is due to its effects on amperage.
CTTWD is extremely important because even slight changes can cause significant changes to our welding current. At a given wire feed speed we can have a swing of over 50 amps if we go from a ½-inch CTTWD to 1-¼-inch in the GMAW, MCAW and FCAW processes.
The reason why CTTWD is not an essential variable is because although it affects amperage, amperage itself is an essential variable. This creates a problem. A perfectly written WPS may call for a ¾” CTTWD. If the welder runs a 1-½” CTTWD the amperage may drop below what is allowed by the WPS. If there is no one monitoring current at the time, no one would know that a weld or welds were made in violation of the WPS.
To illustrate the importance of CTTWD take a look at Figure 10.2.
All three of these welds were made with the exact same parameters with the exception of the CTTWD. The procedure was .045” ER70S-6 at 375ipm 27.5V with 90Ar/10CO2 shielding gas. The desired weld size was ¼”. Below are the values for CTTWD and the resulting amperage.
- ⅜” CTTWD → 354 amps
- ¾” CTTWD → 278 amps
- 1-½” CTTWD → 219 amps
Figure 10.2 – Welds done with the same welding parameter with the exception of CTTWD. The values for CTTWD were (A) 3/8”, (B) 3/4” (C) 1-½”.
Welding procedure (A) provides very deep penetration, so when the CTTWD is increased and amperage drops significantly in procedure (B) we still achieve fusion to the root and even get a good amount of penetration into the root. By further increasing the CTTWD our amperage drops even further, but we still achieve root fusion as seen in image (C).
WARNING: This success with completely different CTTWDs is a testament to a properly developed WPS. However, if the WPS barely passed the qualification tests, meaning fusion to the root and side walls was achieved, but there was very little if any penetration, then slight increases to CTTWD may create lack of fusion.
The problem lies when our welding procedure is not this robust. Imagine we are using 0.035” wire and running at 140 amps. What happens if we increase our CTTWD too much and our amperage drops to 90 amps? Would we still get fusion to the root and sidewalls? What if on top of this change we also have mill scale? You are almost guaranteed lack of fusion.
In the example in Figure 10.2, our PQR was run at the 278 amps. Following AWS D1.1 we would have an acceptable range for amperage in our WPS of +/- 10% or 250 – 306 amps. As you can see, the changes to CTTWD create an issue where we are outside of the allowable range for amperage and thus in violation of the WPS. An inspector may have an issue with welds made when the amperage is 219 as in (C) above, even though it produces acceptable results. The inspector will only know that the weld is outside the allowable range and mark the weld as suspect even though visual inspection of the weld was acceptable.
Skilled welders are able to maintain an adequate CTTWD. And when this CTTWD gets too large there are changes to the arc characteristics that the welder can see and immediately correct. However, sometimes this excessive CTTWD is not due to welder skill, or lack thereof, but due to reach issues. There are many reasons why our CTTWD can change dramatically. It is important to understand the implications of this. If it happens too often it may be time to reevaluate how welding is being done.
Reference: Welding Procedure Development for Non-Welding Engineers
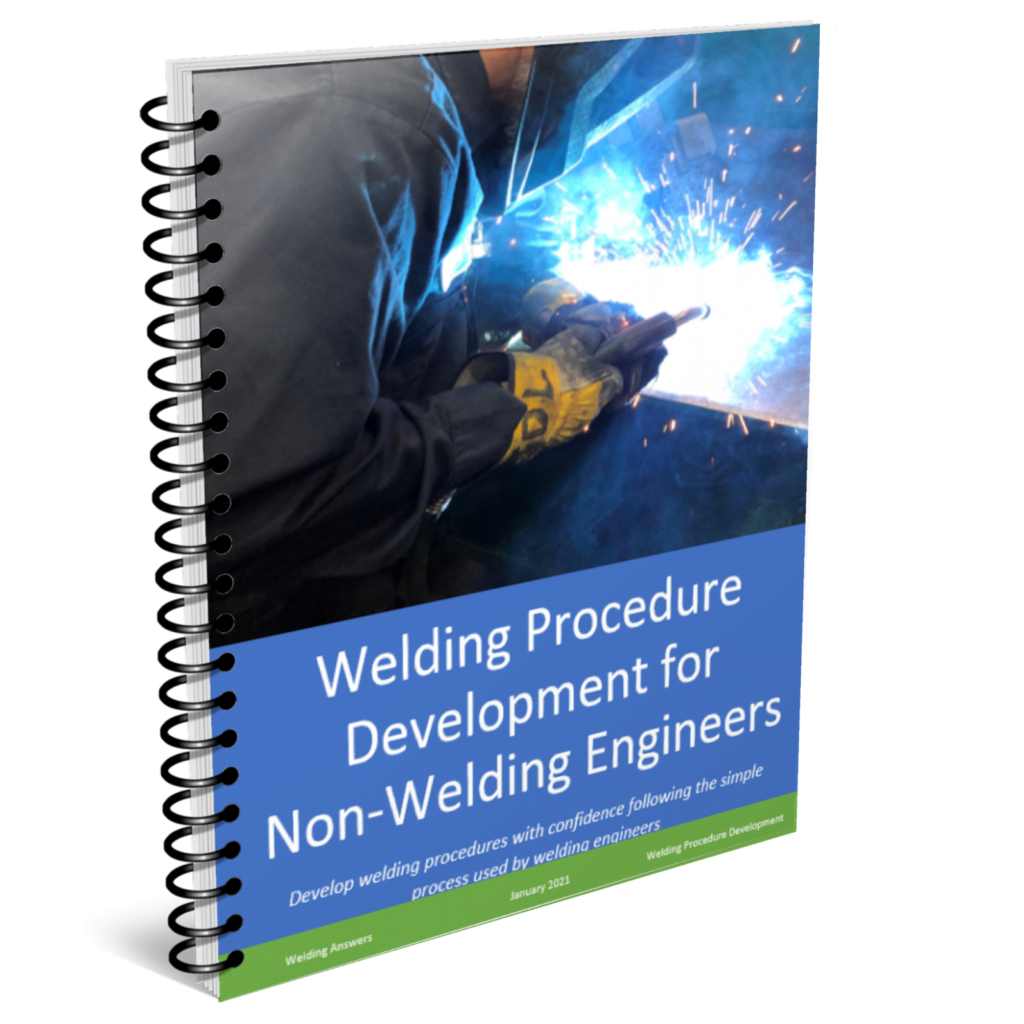
Very informative article. The picture illustrations makes it even more easy to follow.
Thank you.
K Mohlala
Mpumalanga, South Africa
To Andrew & the Team
Well, done an excellent technical article – very informative.
Interesting to note that CTTWD is not an essential variable considering the impact it can have on penetration. Also, the longer the stick out there is a potential risk of porosity.
Thank you
Please keep up the excellent articles.
Phil Richardson
Perth Western Australia