Why Reducing Electrode Diameter and Amperage Is Actually Making Distortion Worse
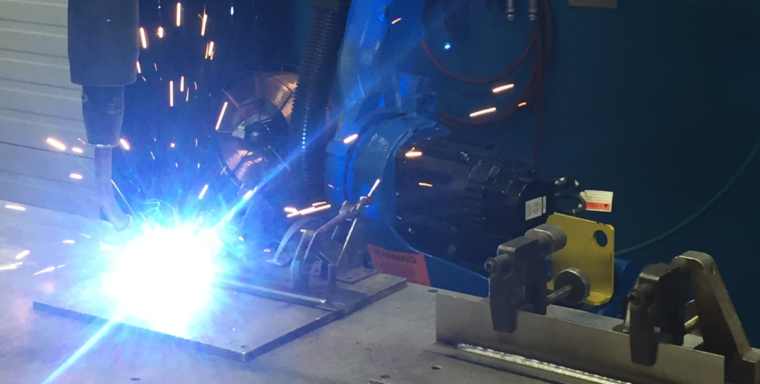
One of the best solutions for welding distortion may seem counterintuitive. Many times, when a fabricator is experiencing distortion from welding, they often believe they are welding too hot. Their initial instinct is to reduce the heat input by lowering the amperage. So, they try it, only to find out the problem persists or even […]