How to Weld ASTM A514 (T1 Steel) Without Cracking
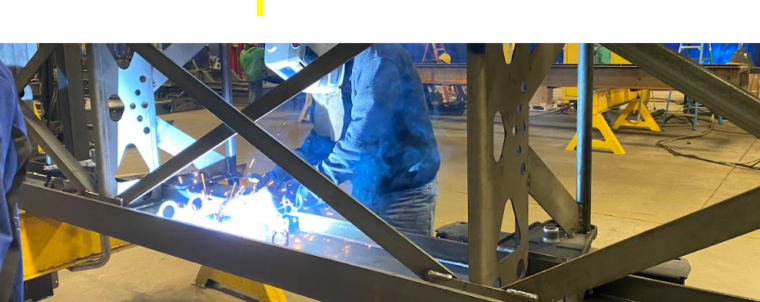
We frequently receive questions regarding the preheating, welding, and post-weld heat treatment of ASTM A514 and other quenched and tempered steels. If you’re working with these materials, the following guidelines will be extremely helpful for welding this steel and avoid cracking or other problems. Metallurgy, Uses, and Welding Challenges of ASTM A514 ASTM A514, often […]