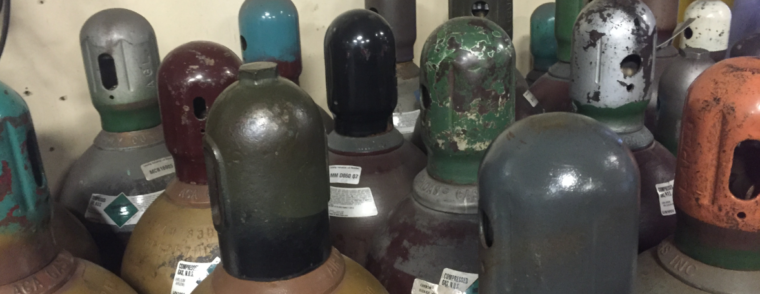
In our previous article we mentioned that a customer was inquiring about running their 98% argon / 2% carbon dioxide (98/2) shielding gas on mild steel. This gas is used on stainless as it maintains the amount of reactive gas (in this case CO2) under 3%. Our quick answer was “yes, you can weld carbon steel with 98/2, but we don’t recommend it.”
Shielding gas does more than just provide protection from the atmosphere while the puddle is molten and a stable medium for the arc. It also affects all of the following:
- Weld strength
- Amount of spatter generated
- Amount of silica islands
- Penetration profile (depth and width)
- Corrosion resistance
- Transition currents (current at which spray transfer is achievable)
Many times a particular welding application can be handled with different shielding gas mixtures. Choosing the best one depends on the specific requirements of the weldment. In many cases not choosing the best gas mix does not bring about negative consequences. However, there certainly are instances in which this can be detrimental. Examples of this are provided in our article on How Shielding Gas Affects Weld Strength.
Back to the issue at hand, can we weld carbon steel with 98/2 gas. The reason why this is not recommended is because to be successful (achieve fusion to the side walls and root) consistently the steel must be very clean (no mill scale, rust, or other surface contaminants). Also, if the welding procedure is not adequate lack of fusion is possible.
Below are two welds on the same material with roughly the same procedure (voltage was higher on the weld on the right to maintain an adequate arc with the much higher CO2 content).
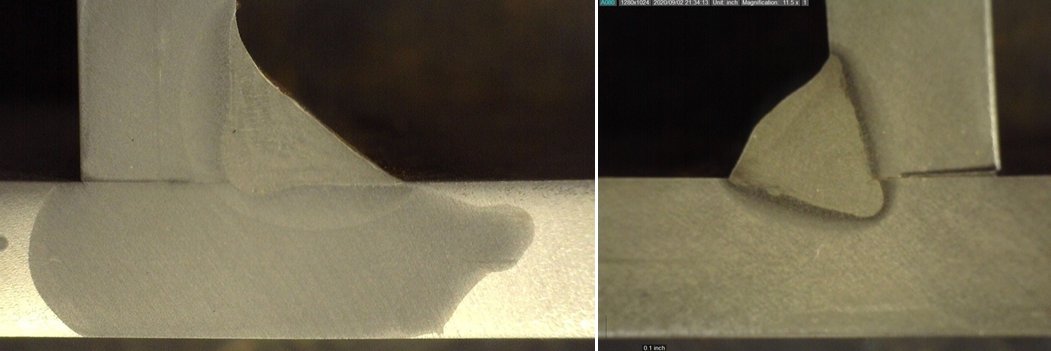
The weld on the left used 98Ar/2CO2 as a shielding gas. The one on the right used 85Ar/15CO2. Both were ran at the same amperage.
As you can see the weld made with 98/2 was able to achieve fusion to the side walls and even penetrate slightly into the root. This is a good weld. But what happens if we have mill scale? Or if our procedure wasn’t well developed? The weld on the right was done with 85% Argon / 15% Carbon Dioxide. Although the amperage was the same our penetration is much deeper (both into the side walls and the root).
With a properly developed procedure and proper work instructions to clean the base metal using 98/2 could be acceptable. But take a look at the image below. This is very common on our studies.
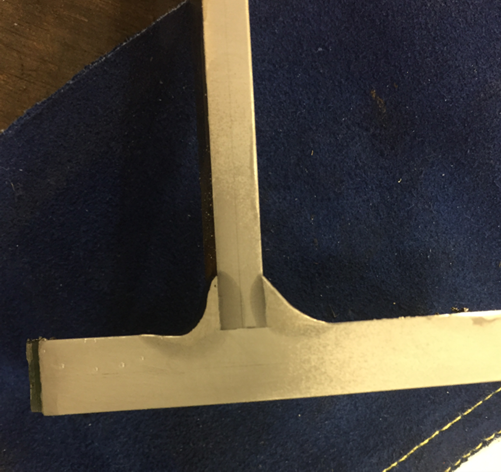
Macro etch showing lack of fusion. Shielding gas used was 95Ar/2O2. Weld was done vertical down with the GMAW process.
These welds were made with 95% Argon / 5% Oxygen. An acceptable gas for carbon steel, but not when we have heavy mill scale. This particular weld was made worse by the fact that it was in the 3F position with a vertical down progression. You can see that there is no fusion to the vertical member. If the weld was made with 98/2 this would be even worse. But could using a blend with 10-20% carbon dioxide prevent this lack of fusion? We can’t be 100% certain because the welding procedure was not adequate and it was done vertical down, but our chances of success definitely would be higher.
As a final note let’s look at this question in reverse. Can I weld stainless steel with a high CO2 content, say 90/10. The answer is you can weld it, but it will rust prematurely. However, we still see a lot of this and the reason always is “because it works, we don’t get any corrosion and the gas is cheaper.” The problem is that you will not see the rust appear right away. Or even within a few days. But it will rust prematurely. This corrosion will happen when the product you build has been in service for a while and may or may not come back to you as a warranty. But it will create a problem for someone. This is one of the common Mistakes Made When Welding Stainless Steel.
As stated above, if you are welding austenitic stainless steels you must have at least 97% inert gas (argon or argon/helium mix) with the balance either carbon dioxide or oxygen. A popular gas for short circuit welding of stainless steel is 90% Helium / 7.5% Argon /2.5% Carbon Dioxide. As you can see it has 97.5% inert gas.
There are situations where only a small portion of the welding done in a facility requires a different shielding gas and this is why the questions of using non-optimal gases come up. There are few cases in which this would present a huge problem. In other cases, such as using 98/2 for steel, it is not recommended but can be done as long as you qualify your welding procedure by testing to ensure you are getting the quality that’s required.
Reference: Welding Metallurgy and Weldability by John C. Lippold