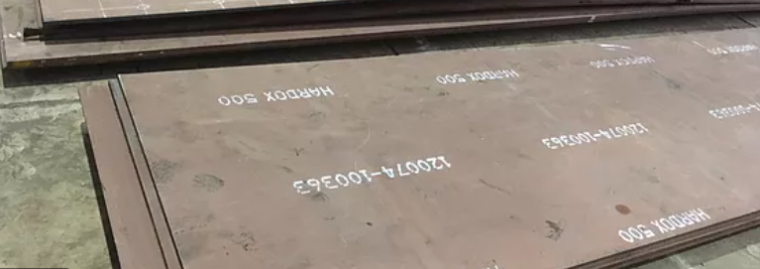
Abrasion resistant (AR) steel plate is used in applications requiring abrasion and impact resistance. It is alloyed with high levels of carbon in order to attain high levels of hardness through the quenched and tempered process. AR plate is primarily used in conveyors, buckets, dump liners, construction attachments, grates, body armor and ballistic plates.
AR plate is not used in structural applications due to its high hardness and low ductility. Using in structural applications would make the structure susceptible to brittle fracture. Although not used in structural applications, it is very common that we need to weld AR plate either to itself (or other hardened steel) or to mild steel such as ASTM A36. Care must be taken in order to avoid hydrogen induced cracking.
Below are the 6 keys to successfully (no cracking) welding AR plate.
- Use low hydrogen consumables – electrodes with designation of -H2 or -H4 must be used when welding AR plate. These designations mean that the deposited weld metal will have a maximum of 2 or 4 mL of hydrogen per 100g of weld metal. Keeping the hydrogen level low will reduce the probability of hydrogen induced cracking, also known as hydrogen assisted cracking and cold cracking.
- Preheat – preheating AR plate is necessary to avoid rapid cooling. The faster the cooling rate the higher the probability of cracking due to the formation of martensite. Martensite makes the heat affected zone (HAZ) hard and brittle. This creates an even more favorable microstructure for hydrogen induced cracking. Always follow the preheat requirements stated by the manufacturer of the AR plate. Using excessive preheat can anneal the base material and reduce its effectiveness in resisting abrasion and impact.
- Slow cool – slow cooling the part is achieved by preheating the base metal. However, the cooling rate can be slowed even more by the use of heat resistant blankets.
- Use undermatching filler metal when permitted – a common mistake is making the assumption that the filler metal must match the strength of the AR plate, that is that the filler metal’s minimum specified tensile strength matches that of the plate. The requirement to match the strength of the AR plate is very rare. When the design of the fabricated product allows you should use an undermatching filler metal. Using a 70 or 80ksi filler metal is typically sufficient. The use of undermatching filler metal will provide a more ductile weld that will reduce residual stresses and perform better in highly restrained joints. If weld strength is a concern, fillet welds and partial joint penetration (PJP) welds can always be made bigger to compensate for the use of undermatching filler metals.
- Minimize weld restraint – if at all possible, minimize weld restraint. Restraint may be internal or external. Internal is due to the filler metal selected as explained in point four above. External has to do with the design of the fabricated product. Some designs don’t allow for the base metal to expand and contract freely. Most times this is due to the size of the parts. The thicker the parts the higher the level of restraint. Unfortunately this is not something that we are typically able to control. So focus on using the right filler metal.
- Peening – peening the weld (after every pass) can reduce susceptibility to cracking by reducing tensile residual stresses. Peening does this by introducing compressive stresses into the weld.
In cases where the weld needs to be abrasion resistance a hardfacing electrode may be used for the final layer. Bare in mind that some hardfacing electrodes require preheat temperature that may exceed those recommended for AR plates. Whenever possible use a buffer layer before applying the hardfacing layer. Follow the recommendations of the AR plate manufacturer for selecting the right electrode for the buffer layer.
Reference: Metals and How to Weld Them, 2nd Edition
Hi.
Do aluminium plate with Abrasive Resistant exists?
Aluminum is often used for ballistic applications but without any kind additional process to provide additional abrasion resistance. At least not to the extend of steel. However, it is possible to bolt AR plate to aluminum or use a process such as explosion welding to weld a dissimilar metal to aluminum which would provide additional abrasion resistance.