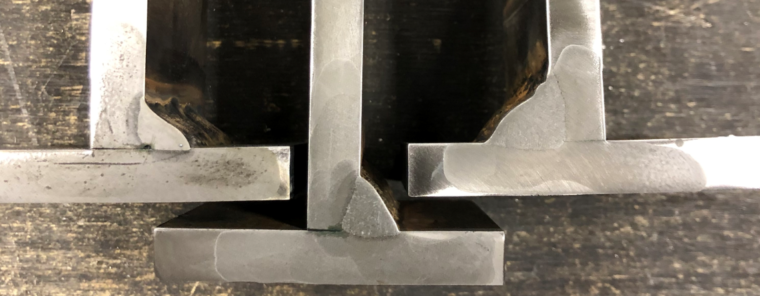
The use of prequalified welding procedures has many advantages as well as many disadvantages. One danger of using prequalified welding procedures is that AWS D1.1 allows for quite a bit of freedom in weld sizes. If you look at Table 5.1 –Prequalified WPS Requirements of AWS D1.1/D1.1M:2020 Structural Welding Code (Steel) you’ll see that in the horizontal position (2F) you can deposit a fillet weld having a maximum size of 3/8” for the flux-cored arc welding process (FCAW). If you have ever run an .045” E71T-1 you know you can deposit a very good looking weld and you can certainly make it big since the slag holds the puddle very well. But can you deposit a 3/8” fillet weld and consistently achieve one of the main requirements of AWS D1.1: achieving root fusion? What about a 5/16″ fillet weld?
The reality is that this is extremely challenging. Yes, it can be done, but not consistently. When you add the fact that welder skill varies tremendously we cannot be assured that even following all the strict requirements of prequalified welding procedures as dictated by the code that we would deposit a weld that achieves root fusion.
We ran a few welds using an .045” E71T-1 at 500 ipm (259 amps), 26.0 volts, ¾” CTTWD and 75/25 gas (argon/carbon dioxide) in the horizontal position. These parameters are recommended by the manufacturer of the filler metal. The weld measured at 5/16” for both legs as shown on the image below.
The weld had good appearance – good wetting at the toes and a relatively flat face. However, we did notice the effects of trying to make a large weld – the beginning stages of overlap on the bottom toe. Certainly not enough to constitute a defect, but we see the effects of gravity even with a welding process that produces slag and should theoretically hold the weld puddle. See the image below.
As you can see there is no root fusion. What you see is not a slag inclusion, the electrode simply did not reach the root because the puddle was too big and it began to run ahead of the wire. This was necessary in order to achieve the leg size of 5/16”. The parameters that were used are towards the high end of this wire, so they were not “cold” by any means.
This is a perfect example of the dangers of using prequalified welding procedures. We are not saying you shouldn’t use them. You absolutely should as they provide many benefits. What we are trying to get across is that you should not use them blindly. Understand where the code pushes the limits and use sound judgment in determining what WPSs you will follow.
You can expect similar results with stick welding (SMAW). Trying to do a 5/16” fillet weld in the horizontal position makes it tough to achieve root fusion. The code allows for up to 3/8″ leg size for FCAW in the horizontal position using the most common diameter, 0.045″. This may be one for you to try. If you get root fusion please let us know and send us an image of the macro.
For fun, we tried the exact same parameters in order to make a 5/16” fillet weld but in the vertical position (3F) with upward progression. The results were what we expected, definite penetration into the root of the joint as can be seen in the image below.
It may be surprising to some that we can get much better results welding out of position. What happens here is that gravity, which normally works against us when welding out of position is actually helping us. By keeping the puddle behind the wire (wire is always on the leading edge of the puddle) we are able to directly hit the root of the joint with the wire. This weld was done as a stringer (no weaving). Now, if you look at Table 5.1 of AWS D1.1 again you’ll see that the maximum allowable size for a fillet weld with the FCAW process in the vertical position is not 3/8” but 1/2”. So we tried it.

FCAW weld done in the 3F positions with upward progression. Leg size of 1/2″ achieved by weaving. Macroetch shows fusion to the root and beyond.
Again the results were satisfactory. Fusion to root and even a good amount of penetration into the root. Again, aided by gravity. By welding in the vertical position with upward progression our travel speed goes down, it is easy to weave and make a big weld which in turn causes our heat input to go up. With good technique this weave can still get great penetration into the root as seen above. So the limitations of AWS D1.1 in this case produce excellent results.
In conclusion, using prequalified welding procedures can be very advantageous. However, this does not exempt you from needing to have a sound knowledge of welding processes. You must understand the limits of each welding process. If you see a prequalified WPS with huge range of amperage and voltage you must be careful. There are a lot of people in our industry that write procedures following the requirements of the code, yet they don’t have much understanding of welding. This can be a recipe for disaster. So good luck and be careful.
Reference: Qualification of Welding Procedures, Welders and Welding Operators per AWS D1.1
Do you want more information on how you can perform your own qualifications?
“Qualifying Welding Procedures, Welders and Welding Operators” is a guide developed to help you peform your own qualifications in full compliance to AWS D1.1 Structural Welding Code.
Are you looking for welding procedures for E6010 and/or E7018 stick processes? Click the image above to get 48 Prequalified WPSs for SMAW in conformance with AWS D1.1 Structural Welding Code.
Greta article and very informative!!
Just looked at Table 5.1, it states maximum single pass fillet weld size of 3/8″ for the horizontal position using the GMAW/FCAW process not 5/16″
Hello Michael. You are correct. The maximum size allowed is in fact 3/8″. This would make achieving root fusion with an .045″ E71T-1 even harder. We really appreciate you pointing out the error. We will get it correcte ASAP.