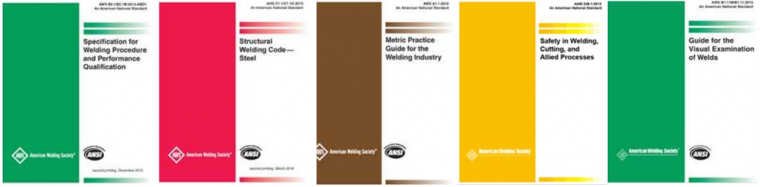
If you have been reading our articles for some time you know how strongly we feel about having documented welding procedure specifications which have been qualified by testing or prequalified in conformance with code requirements. Yet when we recommend that these very important documents be developed and used in production we get a lot of pushback.
Have you ever heard, or have you ever said the following comment: “…we have always done it this way and nothing has ever failed.”
The statement above is 100% true, until the first time there is a failure. One of the biggest problems in welding is that it may only take one failure for something catastrophic to occur. Unfortunately, in some cases, these failures result significant monetary losses, injuries and/or death. Failures will happen; we cannot guarantee that weldments and welded connections will never fail. What we can do is make sure we do our due diligence when setting up and managing welding operations.
What is due diligence? According to the Merriam-Webster dictionary the term “due diligence” means “required carefulness” or “reasonable care” in general usage, and has been used in this sense since at least the mid-fifteenth century. So what are the steps we need to take in order to fabricate with reasonable care?
Any fabricator, whether big or small, should have standards they follow to ensure quality. These standards are typically outlined in a Specification for Weld Quality. Sometimes these specifications are developed internally by the fabricator and other times they are supplied by the customer. Other names for this document may include Weld Quality Control Program, Weld Quality Manual, Welding Standard Operating Procedures, etc. The name doesn’t matter, what matters is the information in it. The depth and breadth of this document can vary depending on what’s being built. A fabricator making pressure vessels will probably have a more extensive specification for weld quality than someone building racks for the automotive industry.
So what should a specification for weld quality include? As a bare minimum it should include:
- Methods for the qualification of Welding Procedures
- Methods for the qualification of Welder Performance
- Methods for the inspection of welds (acceptance criteria)
- Fabrication methods and special instructions
A critical component of any specification for weld quality is its applicability. A document, regardless of how complete it is, will do us no good if it is not applied in production. Having qualified the best welding procedures won’t help us if our welders are not given a copy to follow in production. If we allow our welders to weld outside of the allowed ranges to compensate for their skill level, to compensate for equipment shortcomings, to meet deadlines or simply due to lack of supervision, our welding procedures are completely useless.
When we help customers create their welding quality standards our first choice is to use an applicable structural welding code as our basis. The American Welding Society has structural codes that govern welded structures, should the owner of the project demand it. However, even when not required, following a structural welding code is highly recommended. Codes such as AWS D1.1 Structural Welding Code – Steel are in essence a specification for weld quality which can be adapted and followed.
The code you choose should be applicable to your application. If you are welding aluminum structures then use AWS D1.2 Structural Welding Code – Aluminum. If you are welding stainless steel structures then follow AWS D1.6 Structural Welding Code – Steel. Welding pressure vessels? Follow the ASME Boiler and Pressure Vessel Code.
In some cases these codes can provide a framework for your quality control program, but your application may not quite fit it perfectly. If this is the case use the main building blocks as shown in the codes, but specify your own requirements. These building blocks are the different clauses in the structural codes. If you have never looked at a code book, or if you have never seen it as a quality guide you can read The Clauses of AWS D1.1 Structural Welding Code Explained to get a feel for what to include in your specification for weld quality.
The development and qualification (or prequalification) of welding procedure specifications is by far the most important action you can take in ensuring quality. This is probably why most people that have used AWS D1.1 or other structural welding code primarily deal with the clauses covering qualification of welding procedures and welder performance. When you add inspection (acceptance criteria) to qualified welding procedures and qualified welder performance you’ll have a strong base to ensure production quality.
Next week we’ll touch on the importance of having documented welding procedures specifications. Having these documents and using them in production can:
- Increase productivity
- Decrease costs
- Assure quality and consistency of products
- Prevent costly mistakes
- Defend against litigation
This last one is a big one. We don’t promote the use of welding procedures to defend against someone trying to sue after a failure. We promote the use of welding procedures to assure quality and prevent defects and failures. But should there be a problem with a weldment, if you do not have an established specification for weld quality which includes welding procedures and welder performance records it will make it extremely hard for you to defend your case should it go court.
Please note: I reserve the right to delete comments that are offensive or off-topic.