Thousands of manufacturing shops are full of old welding equipment. We all want to be good stewards of our money or our company’s money, and we want to make things last as long as possible. We sometimes even take pride on the fact that we have had a specific welding machine for 20-25 years. Most of the time we keep these old machines because they still work and there is no need to spend money on a new one. However, many times we are unaware of the real cost of keeping old equipment.
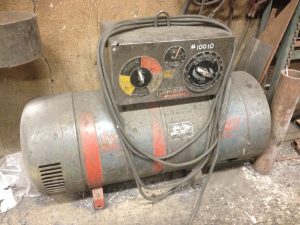
There is no denying some old machines have a magnificent arc, but can they be costing your serious money?
We are big proponents of not spending money in welding equipment until we have exhausted all other costs savings projects. However, sometimes replacing old equipment may be the right thing to do. Pay attention to these issues to see if that oldie-but-goodie is costing you money.
- Repair costs – most shops do not keep track of maintenance costs per machine, rather they only see total spend on welding equipment maintenance. This is dangerous because a few pieces of equipment may be accounting for most of the expense, the old 80/20 rule. If you are servicing a welder more than once a year it may be time to retire it and get a new one. Keep in mind, the cost of the repair is only part of the problem, down time is the killer. If a machine is down 3 times a year and and you lose 2 days of production each time (if you don’t have a spare) you just lost at least 24 hours of production. Keep track of individual machines.
- Productivity – Is your shop full of Miller CP-302’s and Lincoln CV-300’s? Those machines are good and they last forever. But you may be hurting yourself if your work allows for bigger diameter wire to be used. If you can weld with .052 or even 1/16 diameter wire why keep that old CP-300 which limits you to .045? You may be talking an increase of 30-50% in dep0sition rates. A new welder may pay for itself in less than 12 months.
- Pulsing Capabilities – Are you required to do a lot of mig welding out of position and all you have is a conventional straight CV welder? Pulse can increase deposition rates out of position in the neighborhood of 20-40%! That’s quite a bit. By cycling through peak and background currents, pulse cools the puddle a lot quicker than CV which allows you to carry a bigger puddle (higher wire feed speed). Pulse can also help bridge gaps associated with poor fit up.
- Production Monitoring – Do your products need traceability? Newer machines, such as the Lincoln Power Waves and the Miller Continuums have the ability to track all sorts of data. These machines can track arc-on time, numer of welds, idle time, down time, equipment utilization, wire usage, etc. This technology can even alert you to the possibility of a bad weld by providing a weld score.
- High Electric Bills – Inverter technology isn’t new, but not all shops have it. Switching to inverters can save you up to $500 a year per machine in electricity cost. This may yield a 10+ year payback, unless you are billed on peak demand. If this is the case, reducing your peak draw can save you thousands of dollars per year.
- Spare Parts – is it getting harder to find spare parts? Running old Hobart or Airco welders? Those machines last forever, but spare parts will not always be available.
- Code Work – Are you doing work governed by a specific code? Can your current machines be calibrated? Some older units cannot be calibrated without a major overhaul.
- Welding Process – Are you still stick welding when you could be running a wire process? Running a self-shielded flux-cored wire can increase deposition rates by over 100% compared to stick. Consider what a wire process can do for your productivity. Are you tig welding parts that can now be easily welded with GMAW using advanced waveforms? You can now mig welds parts less than 1mm thick. It may be time to look at a new mig welder to replace some or all of your tig operations.
- Safety Concerns– Are your welders getting shocked by the unit? If the case is hot it can create a very dangerous situation. This can be fixed, but if it is an inherent problem due to the machine’s design it may be time to replace it.
- Duty Cycle – Are you often exceeding the duty cycle of your machine and causing it to go on thermal shutdown? Those two to ten minutes you have to wait are costing you a lot of money in loss production. A heavier duty machine with better duty cycle may save you quite a bit of money in the long run.
- Skills Gap – Newer technology in welding machines can help less experienced welders by compensating for irregularities in their technique.
- Portability – Are you hauling welding equipment from job to job or around the shop? Inverter technology has taken a 400-pound 400-amp welding machine and turned it into a 500-amp, 90-pound machine. Ligher and smaller machines may be somethign worth looking into.
Please note: I reserve the right to delete comments that are offensive or off-topic.