Can our selection of shielding gas affect the strength of a weld and other important mechanical properties? Absolutely! The difference is more pronounced when using flux-cored (FCAW) wires than when using mig (GMAW) wires, especially as the wire’s tensile strength goes up. Although we can affect strength by using different gases, what we should be concerned about is preventing failures by using the wrong gases. Choose the wrong the gas with high tensile strength FCAW wires and you can have a catastrophic failure in your hands.
We typically don’t select a specific shielding gas to attain a certain strength level; we do this by selecting the right filler metal. However, because some gases such as carbon dioxide and oxygen are reactive; our weld deposit will differ in chemical composition as compared to the filler metal being used. Other gases like argon and helium are inert (non-reactive) so the weld deposit chemistry will essentially be identical to that of the filler metal.
This is very important to know. Not so much to increase the strength of our weld by better gas selection but to prevent a weld failure.
If you have welded on high strength steels and selected filler metals to do so, you have probably noticed that once you get over 100ksi minimum tensile strength your only choices are flux-cored wires. A mig (GMAW) wire gets all of its alloys from the green rod (raw material). The manufacturer is not able to alloy the steel any further to give it more strength. However, with flux-cored wires, manufacturers have the ability to add all the alloys they want to attain whatever chemical and mechanical properties are desired.
The more alloying elements in the wire the more the deposit chemistry and mechanical properties of a weld are affected by the amount of argon and carbon dioxide in the shielding gas. As the argon content goes up more of the alloys in the wire will remain in the weld. This happens because argon does not react with the molten metal. The more carbon dioxide we have the higher the alloy losses due to chemical reactions in the molten metal. But what does this mean and why is it important?
Take a look at the images below. These are two certificates of conformance for the exact same wire, Lincoln Electric 1/16″ Outershield 71M (AWS Classification E71T-1/9). The first image shows the test results when using 100% carbon dioxide. The second image shows the results when using 75% argon/25% carbon dioxide. Do you notice any difference?
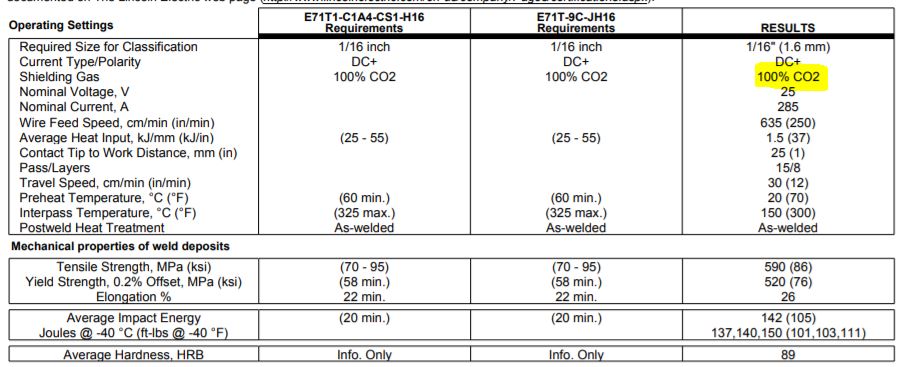
Certificate of conformance showing test results for Lincoln Electric Outershield 71M with 100% carbon dioxide shielding gas

Certificate of conformance showing test results for Lincoln Electric Outershield 71M with 75% argon/25% carbon dioxide shielding gas
What changed?
- Tensile strength went up from 86 to 94ksi
- Yield strength went up from 76 to 85ksi
- Impact energy when down from 105 to 85 Joules at -40˚F
- Hardness went up from 89 to 94 HRB
Are these changes good or bad? The true answer is neither, as long as these values are considered in the design phase. What’s important to note is what increasing argon does to our mechanical properties. As we increase argon content we retain more of the alloying elements which increases our weld strength (tensile and yield strength) and our hardness. This can be considered a good thing, right? Not quite. Our impact energy, which measures the weld’s ability to resist crack propagation, went down significantly. This is because as we increase tensile strength and hardness we reduce toughness. We also lose ductility as can be seen in the elongation numbers dropping from 26 to 24%.
Outershield 71M is designed to run with straight carbon dioxide or mixes having argon content up to 75%. The values attained with both gases meet the AWS requirements. What is dangerous is to use a gas that has higher than 75% argon content. If you by mistake use a C10 (90% argon), your tensile strength will increase further and your ductility and toughness would go down. This significantly increases cracking susceptibility. If you have a highly restraint joint, cracking is almost a certainty if you have poor ductility and high hardness. Many weld failures with the FCAW process can be traced back to using the wrong gas. What’s worse is that these failures do not occur right away, they tend to occur when the welded assembly is in service, making these extremely costly failures. When using FCAW wires always use the gas recommended by the manufacturer.
And remember, the higher the minimum tensile strength of the flux-cored wire, the more critical it becomes to run the recommended shielding gas.
Reference: The Procedure Handbook of Arc Welding – 14th Edition
Quite Interesting and good. Enhances my knowledge by many folds.
Thanks .looking forward for more article of this nature.
oooh thanks for the info