Many fabricators spend thousands of dollars in new welding equipment every year. They look for the latest and greatest technology that will allow them to reduce manufacturing costs. We have seen some of our customers justify the purchase of robots and other types of advanced welding equipment relatively easily. Some pieces of equipment pay for themselves in less than two years. But what is the best tool or piece of equipment to buy to enhance productivity? What is the best use of your money? What is you don’t have much to spend?
Would you buy a $100,000 robot if it will save $50,000 per year for ever? Or a $20,000 welding system that would pay for itself in 8 months? Recently, a consulting client told us they increased welding speeds by 1 7% by going to waveform technology.
This is a fabulous increase in speed and welding productivity. They consume about 50,000 of mig wire a year. This is how they calculated their savings:
By use of waveform technology they were able to increase travel speed by 17% by allowing their welders to increase melt-off rates from an average of 8.9 to 10.4 pounds per hour. The waveforms were more user-friendly and allowed less experienced welders to maintain high melt-off rates and good weld appearance. This meant their welding time decreased from 5,618 hours per year to 4,807. A savings of 811 hours. Their labor and overhead rate was $47.85/hr. The 811 hours saved constituted a savings of $38,806 per year. They would see these savings every year. The cost of implementing this technology was about $65,000 for a total of 8 welding machines. A payback period of 20 months. Well within their 2-year payback period required for all capital expenditures.
This is great! Great savings. But now let’s take a look at another tool to increase productivity. A previous customer of ours of very modest size (they consume about 15,000 of mig wire per year) came to us for help. Their request was to recommend equipment that would increase productivity and reduce their costs. They were planning for next year and had $250,000 budgeted for new equipment. They wanted to spend at least $50,000 in welding equipment provided it made sense.
After surveying their facility we proposed that they spend about $200 in a few tools, one tool actually: fillet weld gauges. Why? They were a structural steel shop making I-beams and welding all sort of attachments and bases for erecting the structures in the field. Their designs called for the minimum allowed weld size per AISC and AWS D1.1 Structural Welding Code – Steel. This meant that 95% of their fillet welds were designed to be 3/16” in leg size.
Our survey revealed that over 90% of those fillet welds were actually welded to a leg size of 5/16” as can be seen in the images below.
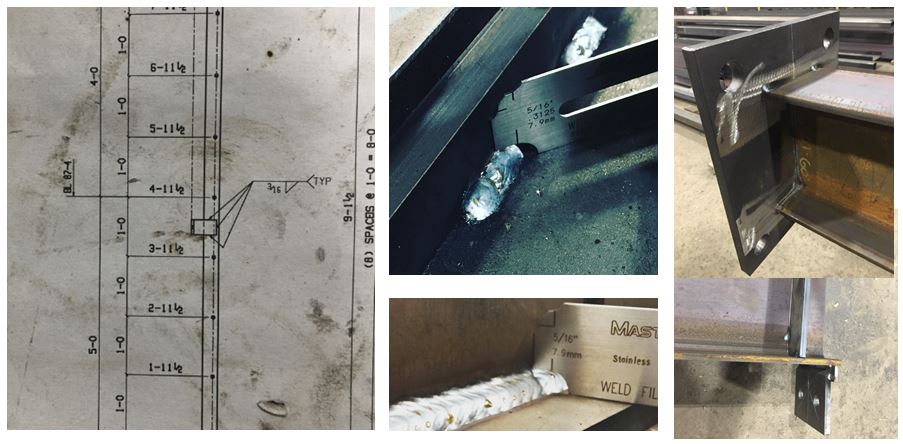
Putting downa 5/16″ fillet weld when the print calls for 3/16″ constitutes overwelding by 177%. The leg size is increased by 67% but the volume is increased by 177%. Overwelding is costing the welding industry millions of dollars a month.
Using the fillet gauges and with reassurance from their engineering department that the 3/16” weld provided plenty of strength, they reduced their weld wire consumption by 64% (going from a 5/16” to a 3/16” leg size is an increase of 177%!!!). All this while still producing the exact same amount of linear feet of weld. This meant a reduction from 15,000 down to 5,415 pounds. A savings of 9,584 pounds of mig wire. Their welding procedures stayed the same, being able to melt-off about 9.2 pounds per hour. This mean a reduction in labor cost of 1,042 hours strictly from reduced welding time. Their labor and overhead rate was reported to only be $32.00/hr which meant the savings amounted to $33,344. This from investing $200 in weld gauges and about $2,500 in training (travel speeds had to increase and minor adjustments to voltage had to be made). A payback period of 29 days! Not even one month.
Please don’t think that we are saying that new equipment is not necessary. Once the reduction in weld sizes generate significant savings and further improvements are needed perhaps better welding technology will help. However, as an industry, we are too quick to find the answer to cost reduction in new equipment when we could be doing very simple things like making sure we are welding to the size specified in our drawings. For more ways to reduce welding costs without capital expenditures read 12 Ideas to Reduce Welding Costs.
Reference: Procedure Handbook for Arc Welding – 14th Edition
Are you looking to qualify welding procedures and/or welders? Are you using AWS D1.1 Structural Welding Code -Steel as your quality standard?
“Qualifying Welding Procedures, Welders and Welding Operators” is a guide developed to help you peform your own qualifications in full compliance to AWS D1.1 Structural Welding Code. It provides step-by-step instructions on how to qualify welders and welding procedures. It also provide step-by-step instruction on the proper use of prequealified welding procedures.
Please note: I reserve the right to delete comments that are offensive or off-topic.