Controlling costs associated with welding operations does not have to be complicated. Yet, many fabricators miss out on savings substantial amounts of time and money simply because they are too busy to take some time to implement cost reduction initiatives. Some of the ways in which costs can be reduced are presented below. Some of these require very little work and are relatively easy to implement. Some are more complex.
You do not have to do all of them. Pick one or two that do not seem too daunting and go after it. The payoff can be huge.
1. Eliminate Overwelding – Make sure welds are properly sized by following what is called out on the print. Don’t have prints? Develop them! The savings can be huge. For more details take a look at The Outrageous Cost of Overwelding.
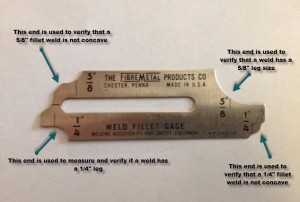
A fillet weld gauge costs less than $10 and can save you thousands. Are you measuring your fillet welds?
2. Reduce the amount of reinforcement – Multiple pass welds on a groove joint typically end up with a certain amount of reinforcement. The goal is to be just above flush to prevent underfill. However, a 1/8″ reinforcement will not be better than a 3/32″ or even a 1/16″ in most cases.
3. Use proper polarity – In applications were penetration is not important or desired, such as hardfacing, use DC- to achieve greater deposition rates.
4. Reduce gaps – Gaps increase the volume of weld needed in order to achieve the same load carrying capacity. Do you think not controlling gaps and fit up is not costing you money? Take a moment to read The Outrageous Cost of Poor Fit Up.
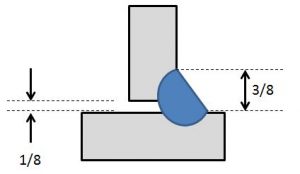
Some codes may allow up to a 1/16″ gap on fillet welds. Anything more than that and your fillet weld leg size must be increased by the size of the gap. Increasing a 1/4″ fillet to 3/8″ represents a huge increase in fillet metal needed.
5. Control Shielding Gas Usage – For processes that require shielding gas make sure no more flow than necessary is used. Too much flow will waste gas and can even create weld defects. Other ways in which you may be wasting shielding gas are surges and leaks. For more on this read Control Your Shielding Gas Usage.
6. Increase electrode diameter – Whether you are stick welding or mig welding, consider using a larger electrode to achieve higher deposition rates.
7. Consider intermittent instead of continuous fillets – This is a design consideration, so you may need to get your engineering group involved. Most fillet welds uses in welding do not transmit the full load of the structure. In some cases the welds are just there for rigidity or to hold things in place. In this case you may be better off making intermittent. welds rather that a long continuous weld.
8. Select the right process – Submerged arc welding can yield over 50 lb/hr deposition rate, but stick welding may be the best option at only 4-5 lb/hr. Why? because selecting the right process depends on the application. If you are mostly welding in the flat and horizontal positions then solid (GMAW) or metal-cored (MCAW) large diameter wires may be the best option. Welding a lot of overhead and vertical up then flux-cored (FCAW) or even stick (SMAW) may be the best alternative. Also, consider the skill level of your welders as well when selecting the right process. Above all, make sure the process selected will meet the quality standards.
9. Properly position the work for optimal efficiency – ideally we want to weld in the flat or horizontal position. Welding out of position (vertical up, overhead, 3 0’clock, etc.) reduces deposition rates because we are limited in puddle size.
10. Use fixtures – Fixtures can drastically minimize man-hours in welding operations. Most fixtures for semi-automatic welding are designed by welders as they are the ones in the trenches. Listen to the ideas your welders have on this matter. If you can make their job easier they will weld more which is what we want them to do. We do not want our skilled welders fitting up parts for hours.
11. Use procedures and processes that eliminate spatter – Consider using 90/10 gas instead of C25 or 100% CO2. Consider pulse welding instead of CV welding. Take a close look at your wire feeds speed and voltage if running a wire process. Can you use spray transfer rather than globular? For more on modes of metal transfer see our 4-part series on Modes of Metal Transfer.
12. Keep your welding equipment in good repair – Frayed cables, loose connection and undersized equipment can create voltage losses, erratic arcs and wire feeding problems. A proper preventative maintenance program can significantly reduce manufacturing costs. There are upfront costs of instituting a PM program, but it pays for itself rather quickly in reduced man-hours spent troubleshooting welding welding problems.
Many other ways exists to minimize welding related costs. If you have some of your own let us know. If you plan on using any of the above please leave us a comment.
It’s a great book to follow.
Very interesting read, thanks for posting this. The company I work for, virtually does the opposite of all these ideas.
Thanks Karo. I hope things turn around for your company. A lot of companies that hire us for consulting are unaware of how much money they are wasting by ignoring these concepts. Our job is to make them aware of it. Even after doing studies and proving to them how much they are wasting some still decided to do nothing.
Hola.
No tengo ningún entrenamiento formal, así que para aprender siempre estoy buscando información y trabajando con mi maquina lo mas posible para ir mejorando la calidad de la soldadura. Por lo que agradezco vuestro esfuerzo y los felicito por su Blog
Atentamente
R.Morrison
Ronald, un placer leer su comentario. Mis disculpas por no haber respondido anteriormente. Si ocupa algo por favor contactenos por email https://weldinganswers.com/contact-us/
Suerte!